流体输送用管检测的重要性及应用场景
流体输送用管作为工业生产和市政工程中的关键组件,广泛用于石油、天然气、化工、供水及供热系统等领域。其性能直接影响输送效率、安全性和使用寿命,因此需要依据相关标准进行系统性检测。检测项目涵盖材料性能、制造工艺、耐压能力及耐腐蚀性等多个维度,目的在于确保管道在高压、高温、腐蚀介质等复杂工况下长期稳定运行,同时预防因管道失效引发的泄漏或安全事故。
核心检测项目及技术要求
1. 材料成分与力学性能检测
通过光谱分析、化学滴定等方法验证管道材料的化学成分是否符合标准(如GB/T 8163、ASTM A53等),重点控制碳、锰、硫、磷等元素含量。力学性能测试包括拉伸试验(测定抗拉强度、屈服强度)、冲击试验(评估低温韧性)及硬度测试,确保材料具备足够的承压能力和延展性。
2. 耐压与密封性试验
采用液压试验或气压试验模拟管道实际工作压力,验证其短期耐压强度和长期疲劳性能。试验压力通常为设计压力的1.5倍,保压时间根据标准要求执行。同时通过气密性检测(如肥皂泡法或氦检漏技术)排查焊缝和连接部位的泄漏风险。
3. 腐蚀性能评估
针对输送腐蚀性介质的管道(如酸液、海水),需进行晶间腐蚀试验(如硫酸-硫酸铜法)、盐雾试验或电化学腐蚀测试。对于埋地管道,还需开展土壤腐蚀性分析及涂层附着力检测,综合评估防腐措施的可靠性。
4. 几何尺寸与表面质量检查
使用超声波测厚仪、卡尺等工具检测管径、壁厚、椭圆度及直线度偏差。表面需无裂纹、折叠、结疤等缺陷,焊缝区域需通过目视检查或磁粉探伤(MT)、渗透探伤(PT)确认无未熔合、气孔等缺陷。
5. 无损检测技术应用
对关键部位采用X射线检测(RT)、超声波检测(UT)或涡流检测(ET),实现焊缝内部缺陷的非破坏性排查。例如,超声波探伤可识别分层、夹渣等缺陷,检测灵敏度需达到行业标准规定的级别要求。
检测标准与质量控制体系
检测过程需严格遵循GB/T 3091、API 5L、ISO 3183等国内外标准,同时结合工况需求制定个性化检测方案。第三方实验室需通过CMA/ 认证,确保检测数据的权威性。企业应建立从原材料入厂到成品出厂的全流程质量控制体系,定期开展工艺审核与设备校准,以保障流体输送管的全生命周期安全性。
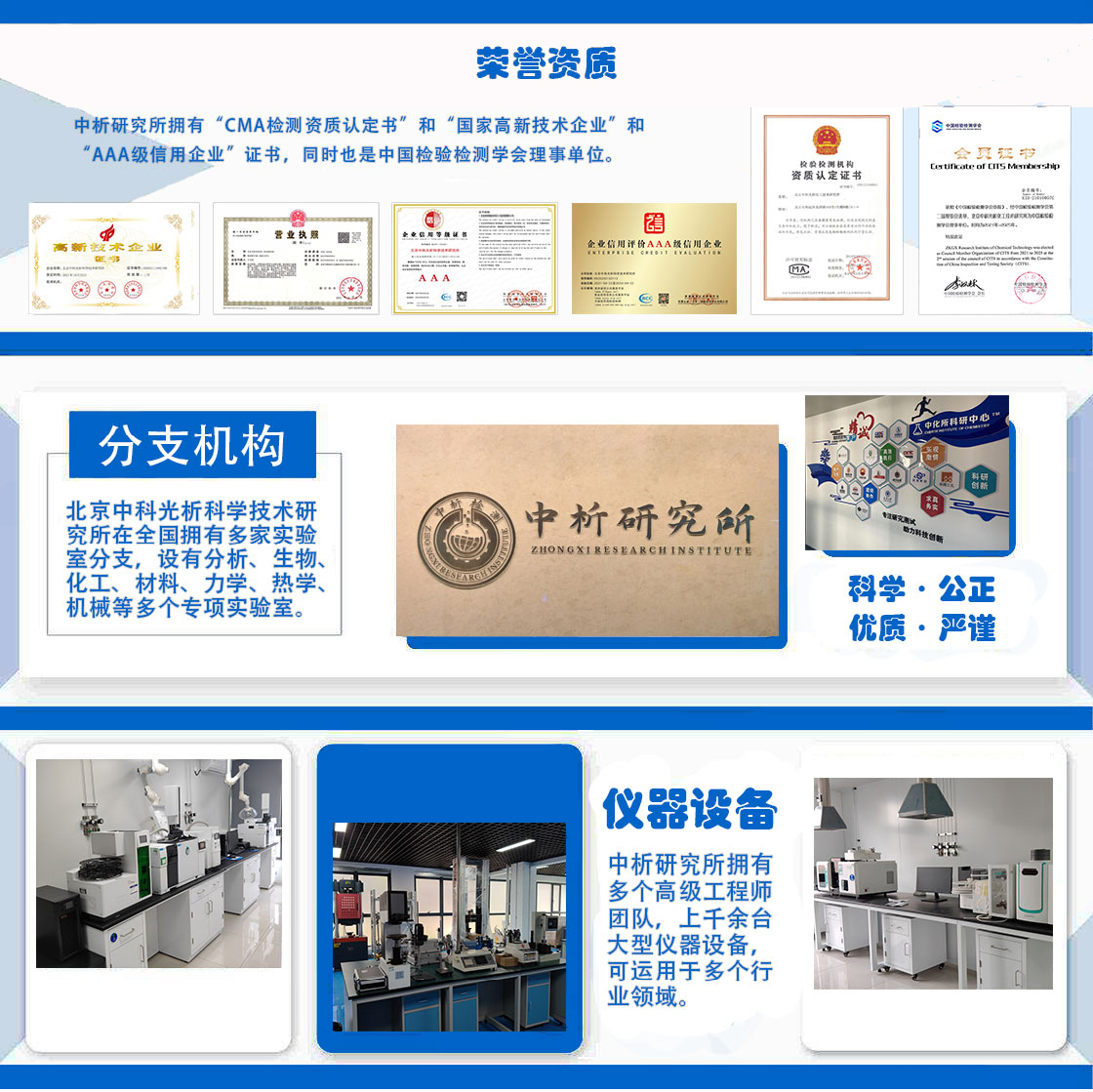
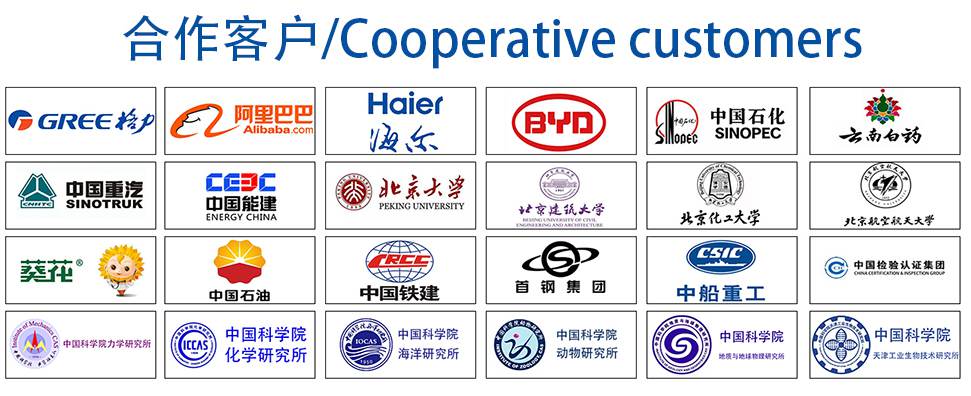