高钛渣与金红石检测的核心项目解析
高钛渣和金红石是钛产业链中重要的原料,广泛应用于钛白粉、海绵钛、钛合金等产品的生产。高钛渣主要通过电炉熔炼钛铁矿获得,其二氧化钛(TiO₂)含量通常在70%-95%之间;而金红石则是天然存在的钛矿物,TiO₂含量可达95%以上。两者的质量直接影响下游产品的性能,因此需要通过严格的检测项目确保其化学成分、物理性质及杂质含量符合工业标准。
1. 化学成分检测
化学成分是高钛渣和金红石检测的核心内容,主要包括以下项目: - TiO₂含量测定:通过X射线荧光光谱(XRF)或湿法化学分析(如硫酸高铁铵滴定法)定量检测钛氧化物含量,直接影响原料品位评估。 - 杂质元素分析:检测铁(Fe)、硅(Si)、铝(Al)、钙(Ca)、镁(Mg)等杂质元素,尤其是高钛渣中的Fe₂O₃和SiO₂需严格控制,以防止冶炼过程中形成难熔渣相。 - 放射性元素检测:针对部分金红石矿源,需测定钍(Th)、铀(U)等放射性元素的含量,确保原料符合环保法规。
2. 物理性质测试
物理性能对原料的加工适用性至关重要,主要检测项目包括: - 粒度分布:通过激光粒度仪或筛分法分析颗粒大小,粒度范围影响冶炼反应速度和能耗。 - 密度与孔隙率:使用比重瓶法或气体置换法测定,高孔隙率可能导致冶炼过程中气体滞留。 - 熔点与熔融特性:借助高温差示扫描量热仪(DSC)评估原料的熔融行为,为冶炼工艺参数优化提供依据。
3. 矿物组成与结构分析
针对金红石矿物及高钛渣的微观特性,需进行以下专项检测: - X射线衍射(XRD)分析:确定物相组成(如金红石型TiO₂、锐钛矿型TiO₂或硅酸盐杂质相)。 - 扫描电镜-能谱联用(SEM-EDS):观测颗粒形貌及元素分布,识别包裹体或共生矿物。 - 磁性物质检测:通过磁选分离法评估铁磁性杂质含量,避免对电炉冶炼产生干扰。
4. 工业应用指标检测
根据下游需求,还需进行针对性测试: - 氯化法适用性:金红石的CaO+MgO含量需低于1.5%,以防止氯化过程中结垢。 - 酸解率测试:针对硫酸法钛白粉生产,测定高钛渣在浓硫酸中的溶解效率。 - 还原性能评价:模拟电炉冶炼条件,检测钛渣的金属钛收得率及能耗比。
检测技术发展趋势
随着技术进步,电感耦合等离子体质谱(ICP-MS)用于痕量元素检测、原位激光剥蚀分析(LA-ICP)实现微区成分快速测定等技术逐步普及。同时,智能化检测系统可整合多维度数据,通过算法模型预测原料冶炼性能,为产业链提质增效提供科学支撑。
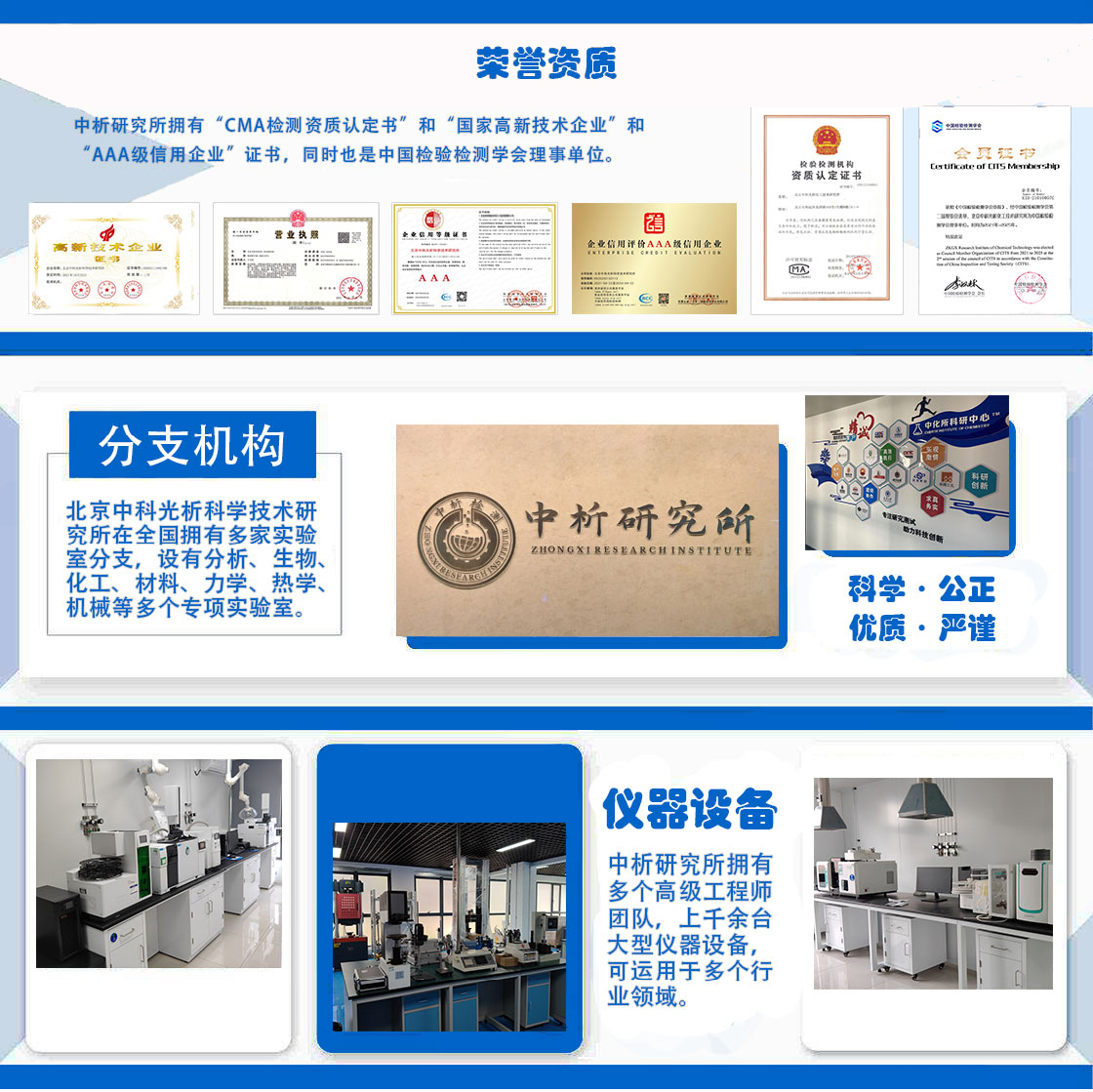
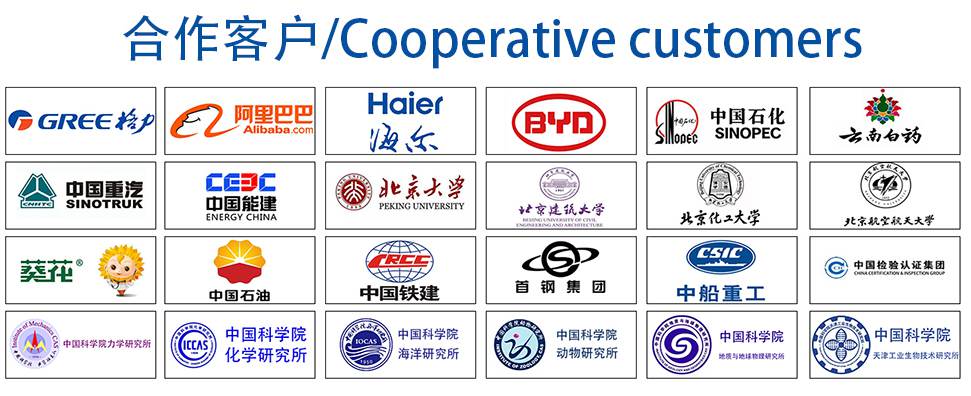