钢质储罐防腐层检测的重要性
钢质储罐作为石油、化工、能源等行业中存储液体或气体介质的关键设备,长期暴露于复杂环境中,极易因腐蚀导致结构失效甚至泄漏事故。防腐层作为储罐的第一道防线,其完整性直接关系设备的安全性与使用寿命。然而,防腐层在安装、使用过程中可能因机械损伤、老化、化学侵蚀等原因出现缺陷,若不及时检测修复,将加速罐体基材的腐蚀进程。因此,通过系统化的防腐层检测项目评估涂层性能,已成为储罐运维管理中不可或缺的环节。
防腐层检测的核心项目
钢质储罐防腐层检测需覆盖物理性能、化学稳定性及环境适应性等多个维度,主要包括以下关键项目:
1. 防腐层外观检查
通过目视或高清摄像设备对涂层表面进行全区域扫描,重点识别开裂、起泡、剥落、锈斑等可见缺陷。同时检查涂层颜色均匀性及边缘覆盖完整性,评估施工工艺质量。
2. 涂层厚度测量
采用磁性测厚仪或超声波测厚仪,按照GB/T 4956标准进行多点测量,确保平均厚度符合设计要求(如环氧涂料≥300μm)。局部过薄或超厚区域需标记并分析成因。
3. 附着力测试
依据ISO 4624标准,使用划格法或拉开法仪测定涂层与基材的结合强度。合格指标通常要求≥5MPa(环氧类涂层),若出现成片剥离则需针对性处理。
4. 漏点检测(电火花检测)
利用高压电火花检测仪(电压范围1.5-35kV)扫描防腐层表面,通过放电现象定位针孔、裂缝等隐蔽缺陷。检测电压需根据涂层厚度精准设定,避免击穿完好涂层。
5. 电化学性能评估
采用极化电阻法或电化学阻抗谱(EIS)分析涂层对基材的防护效率,测量涂层电阻、电容等参数,评估防腐层的抗渗透性及长期耐久性。
6. 涂层老化程度分析
通过傅里叶红外光谱(FTIR)检测有机涂层化学结构变化,结合硬度计测试涂层脆化情况,量化评估紫外线、温湿度等因素导致的材料性能退化。
7. 环境适应性验证
针对储罐实际工况,模拟介质浸泡、冷热循环、盐雾腐蚀等环境条件,加速测试防腐层的抗渗透性、耐温变能力及化学稳定性。
检测结果的应用与维护策略
综合检测数据后,需建立缺陷分级台账:微小划痕可通过局部修补处理,大面积剥落则需彻底铲除并重新涂装。定期检测周期通常设定为3-5年,临海或强腐蚀环境应缩短至2年。检测中发现基材腐蚀时,需同步进行壁厚测量与强度校核,确保储罐整体安全性。
通过科学的防腐层检测体系,企业可显著延长储罐服役寿命,降低突发性泄漏风险,同时为制定预防性维护计划提供可靠依据。建议选择具备CMA/ 资质的专业机构,结合自动化检测设备与人工复验,实现防腐层状态的全生命周期管理。
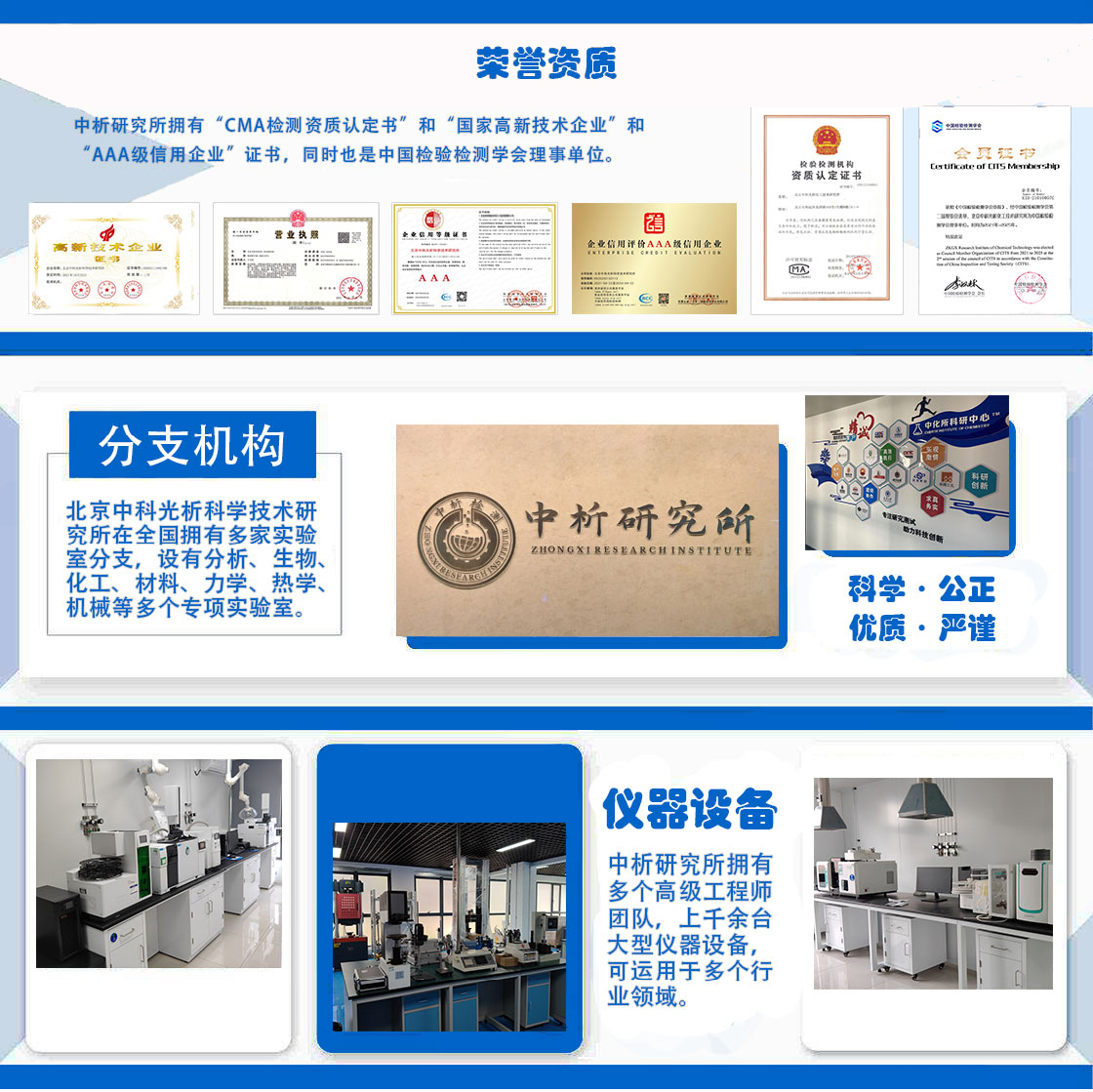
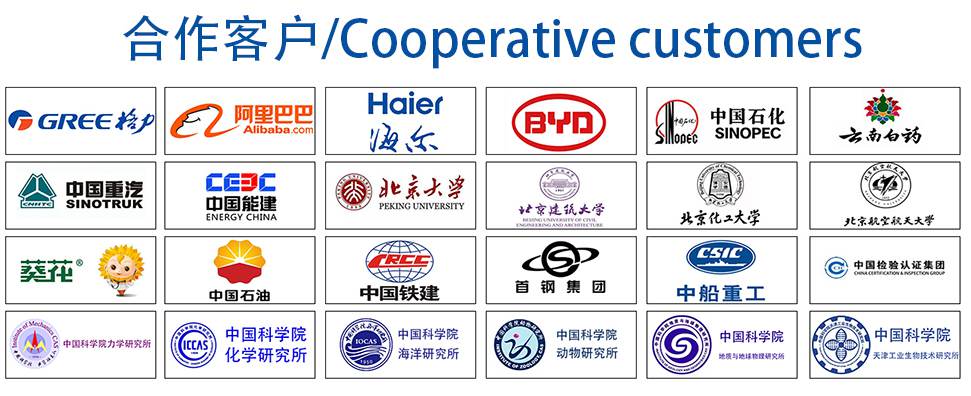