实验室扩大连续试验与半工业试验检测的核心意义
实验室扩大连续试验(Pilot-scale Continuous Testing)和半工业试验(Semi-industrial Testing)是科研与工业生产衔接的关键环节,尤其在化工、材料、冶金及新能源领域具有不可替代的作用。通过这两个阶段的试验,能够验证实验室小试成果的可行性,同时为工业化生产提供可靠的数据支撑。在这一过程中,检测项目作为核心评估手段,贯穿于试验设计、过程监控与结果分析的全流程,其系统性、精准性和全面性直接决定了试验的最终价值。
检测项目的分类与实施要点
在扩大连续试验与半工业试验中,检测项目主要分为工艺参数检测、产品性能检测及环境影响评估三类。工艺参数检测包括反应温度、压力、流速、转化率等动态指标的实时监测,需借助高精度传感器与自动化控制系统;产品性能检测则涵盖成分分析、物理特性(如粒度、密度)及化学稳定性测试,通常需要采用ICP-MS、XRD、SEM等精密仪器;环境影响评估需对废气、废水、固废进行合规性检测,确保工艺符合环保法规。
关键检测技术及标准化流程
为确保数据的可比性和可重复性,试验过程中需严格执行标准化检测流程。例如在催化反应体系测试中,需按照ASTM D3908标准进行催化剂活性评价,同时通过GC-MS连续采样分析产物分布。对于材料成型工艺的半工业试验,需依据ISO 178进行三点弯曲强度测试,并结合在线热成像技术监测材料内部缺陷。检测数据的处理需采用SPC(统计过程控制)方法,确保工艺波动处于可控范围。
典型检测案例分析
以锂电池正极材料的中试生产为例,需重点监测以下项目:1)连续混料过程中纳米颗粒的分散均匀性(通过激光粒度仪与TEM联用);2)烧结炉温度场分布的稳定性(红外热像仪+热电偶矩阵);3)极片涂布厚度的在线检测(β射线测厚仪)。检测数据需与实验室小试结果进行对比分析,若发现批次间容量差异超过5%,则需触发工艺参数调整机制。
检测技术的智能化升级趋势
随着工业4.0技术的渗透,试验检测系统正加速向智能化转型。基于机器视觉的实时缺陷识别、结合数字孪生的虚拟检测平台以及AI驱动的异常检测算法,显著提升了检测效率与准确率。例如某化工企业开发的半工业试验数字孪生系统,可将实际检测数据与虚拟模型动态比对,提前48小时预测管道结焦风险,使设备维护成本降低30%以上。
结语
实验室扩大连续试验与半工业试验的检测体系,既是科研成果转化的质量闸门,也是工业化生产的预演平台。通过构建多维度检测矩阵、采用齐全分析技术并实施严格的质控标准,能够有效降低产业化风险,为技术落地提供坚实保障。未来随着检测技术的持续革新,这一领域的精准化、智能化水平将迈上新的台阶。
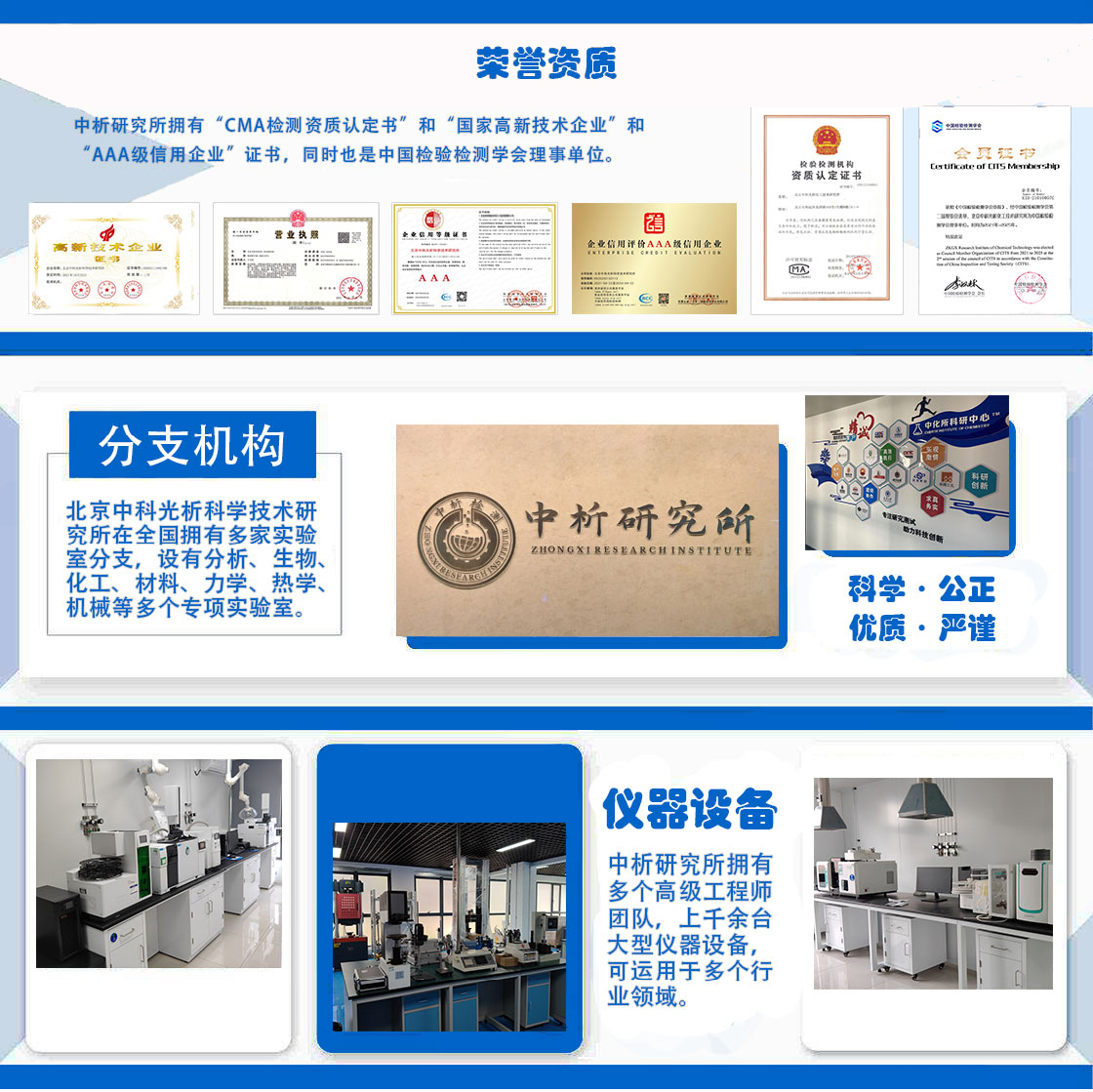
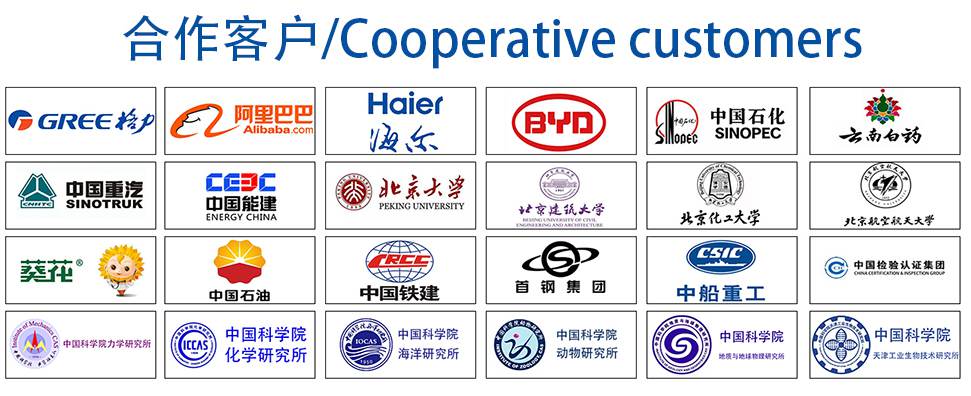