钢铁材料及其制品检测的重要性
钢铁材料及其制品作为现代工业的基础材料,广泛应用于建筑、机械制造、交通运输、能源装备等领域。其性能直接关系到工程结构的安全性、耐久性和经济性。然而,钢铁生产过程中可能存在的成分偏差、内部缺陷或工艺问题,可能导致材料强度不足、耐腐蚀性下降或脆性断裂等风险。因此,通过科学的检测手段对钢铁材料及其制品进行全面质量评估,是保障产品可靠性、满足行业标准与用户需求的关键环节。
核心检测项目分类
1. 化学成分分析
通过光谱分析法(如ICP-OES、XRF)或化学滴定法,检测钢铁中碳(C)、硅(Si)、锰(Mn)、硫(S)、磷(P)等元素的含量。精确的成分控制直接影响材料的力学性能和耐腐蚀性,例如碳含量过高可能导致脆性增加。
2. 力学性能测试
包括拉伸试验(测定抗拉强度、屈服强度、延伸率)、冲击试验(评估材料韧性)、硬度测试(布氏、洛氏或维氏硬度)。这些指标是判断材料在载荷下是否满足设计要求的重要依据。
3. 金相组织分析
利用光学显微镜或电子显微镜观察钢铁的微观组织结构(如铁素体、珠光体、马氏体等),分析晶粒度、夹杂物分布及相组成,评估热处理工艺的合理性及其对性能的影响。
4. 无损检测(NDT)
采用超声波探伤(UT)、射线检测(RT)、磁粉探伤(MT)或渗透检测(PT)等技术,在不破坏材料的前提下检测内部裂纹、气孔、夹杂等缺陷,确保制品结构完整性。
5. 耐腐蚀性测试
通过盐雾试验、湿热循环试验或电化学方法(如极化曲线分析),模拟不同环境下的腐蚀行为,评估材料的抗氧化、抗酸碱侵蚀能力,尤其是对不锈钢和特种合金的检测尤为关键。
6. 尺寸与形位公差检测
利用三坐标测量仪、激光扫描仪等设备,精确测量钢铁制品的几何尺寸、表面平整度、圆度等参数,确保其与设计图纸的符合性及装配适配性。
7. 焊接质量评估
针对焊接接头进行宏观/微观检验、弯曲试验和硬度梯度测试,检测焊缝是否存在未熔合、气孔、夹渣等缺陷,确保焊接工艺的稳定性和接头强度。
检测技术的现代化趋势
随着智能化技术的发展,检测领域正逐步引入自动化设备(如机器人探伤系统)和数字化分析平台(AI缺陷识别)。例如,X射线断层扫描(CT)可三维重构材料内部缺陷,而大数据技术则能实现检测结果的多维度关联分析,显著提升检测效率与准确性。
结语
钢铁材料及其制品的检测贯穿原料筛选、生产过程控制到成品验收的全生命周期。通过系统化的检测项目组合与技术创新,可有效预防质量事故,推动钢铁行业向高精度、高可靠性方向发展,为工业安全与可持续发展提供坚实保障。
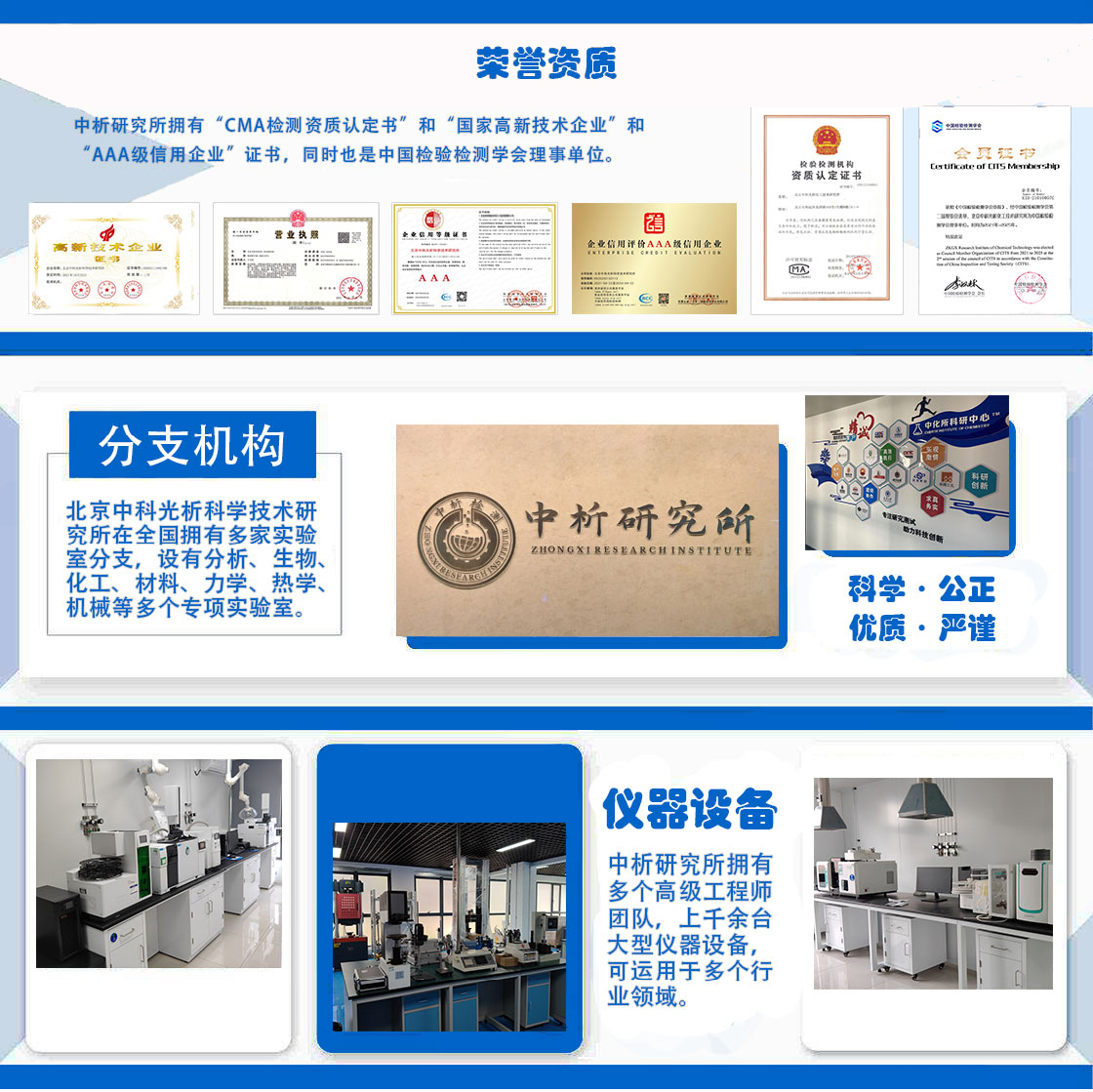
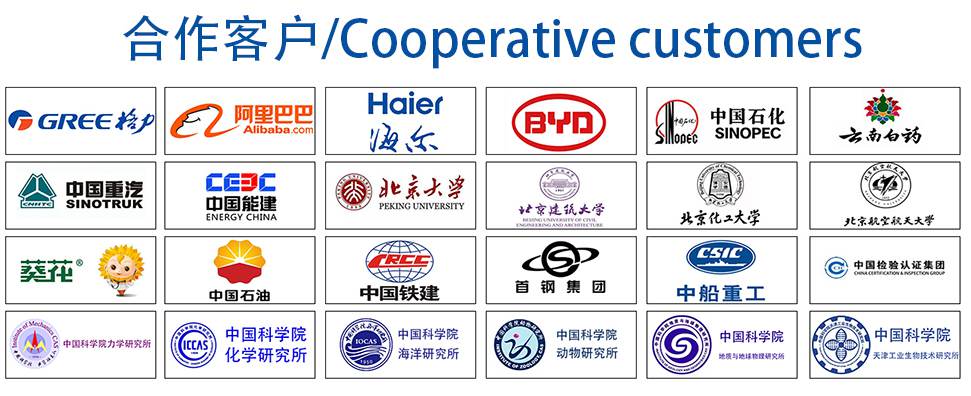