金属载体催化剂检测的关键项目与技术解析
金属载体催化剂作为工业催化领域的核心材料,广泛应用于石油化工、环境保护、新能源开发等领域。其性能直接影响反应效率、产物选择性和设备运行稳定性。为确保催化剂的质量和活性,需通过系统化检测手段对物理化学性质、结构特征及使用性能进行全面评估。检测项目的选择需结合催化剂类型(如贵金属/过渡金属载体)、应用场景(如加氢、氧化、脱硫等)及使用阶段(新鲜/再生催化剂)进行针对性设计。
核心检测项目及方法
1. 金属负载量测定
通过ICP-OES(电感耦合等离子体发射光谱)或XRF(X射线荧光光谱)精准分析活性组分(如Pt、Pd、Rh)的实际负载量,偏差需控制在±0.1%以内。同步结合EDS(能谱分析)实现载体表面的元素分布表征。
2. 机械强度测试
采用压碎强度仪测定单颗粒抗压强度(MPa级),评估催化剂在装填、反应工况下的抗破碎能力。流化床催化剂需额外进行磨损率测试(ASTM D5757标准)。
3. 比表面积与孔结构分析
基于BET法计算比表面积(m²/g),BJH模型解析孔径分布(微孔/介孔比例)。典型工业催化剂比表面积需达150-400m²/g,孔容0.3-1.2cm³/g,以满足传质需求。
4. 活性组分分散度检测
应用CO化学吸附法测定金属分散度(D%),结合TEM观察纳米粒子尺寸(2-10nm范围)。高分散度可提升原子利用率,降低贵金属用量。
5. 热稳定性验证
通过TPR(程序升温还原)分析还原特性,TPD(程序升温脱附)检测酸性位点强度。800℃高温焙烧实验可模拟长期使用后的结构演变。
功能性性能评价体系
1. 催化活性测试
建立微型固定床反应器系统,在模拟工况下测定转化率、选择性及TOF(转换频率)。如加氢催化剂需评估苯加氢环己烷产率(>99.5%)。
2. 抗中毒特性分析
引入硫、氯等毒化物质(浓度梯度法),通过XPS表征毒物吸附位点,评价催化剂的再生能力。车用催化剂需通过100小时含硫燃料耐受实验。
3. 寿命预测模型构建
结合加速老化实验(高温、高湿度、高毒物负荷)与Arrhenius方程推算实际使用寿命,优化再生周期设计。
质量控制与标准化
检测过程需严格参照ISO 9001质量管理体系及ASTM D8098催化剂检测标准。针对车用催化剂须满足GB 18352.6-2016排放标准,石化领域催化剂需通过API RP 571腐蚀性评估。第三方认证机构(如SGS)的定期复核可确保数据可靠性。
通过多维度的检测体系,可优化催化剂制备工艺,提升工业装置运行经济性。随着原位表征技术(如XAS、operando XRD)的普及,金属载体催化剂的检测正朝着高精度、动态化方向发展,为新型催化材料研发提供关键支撑。
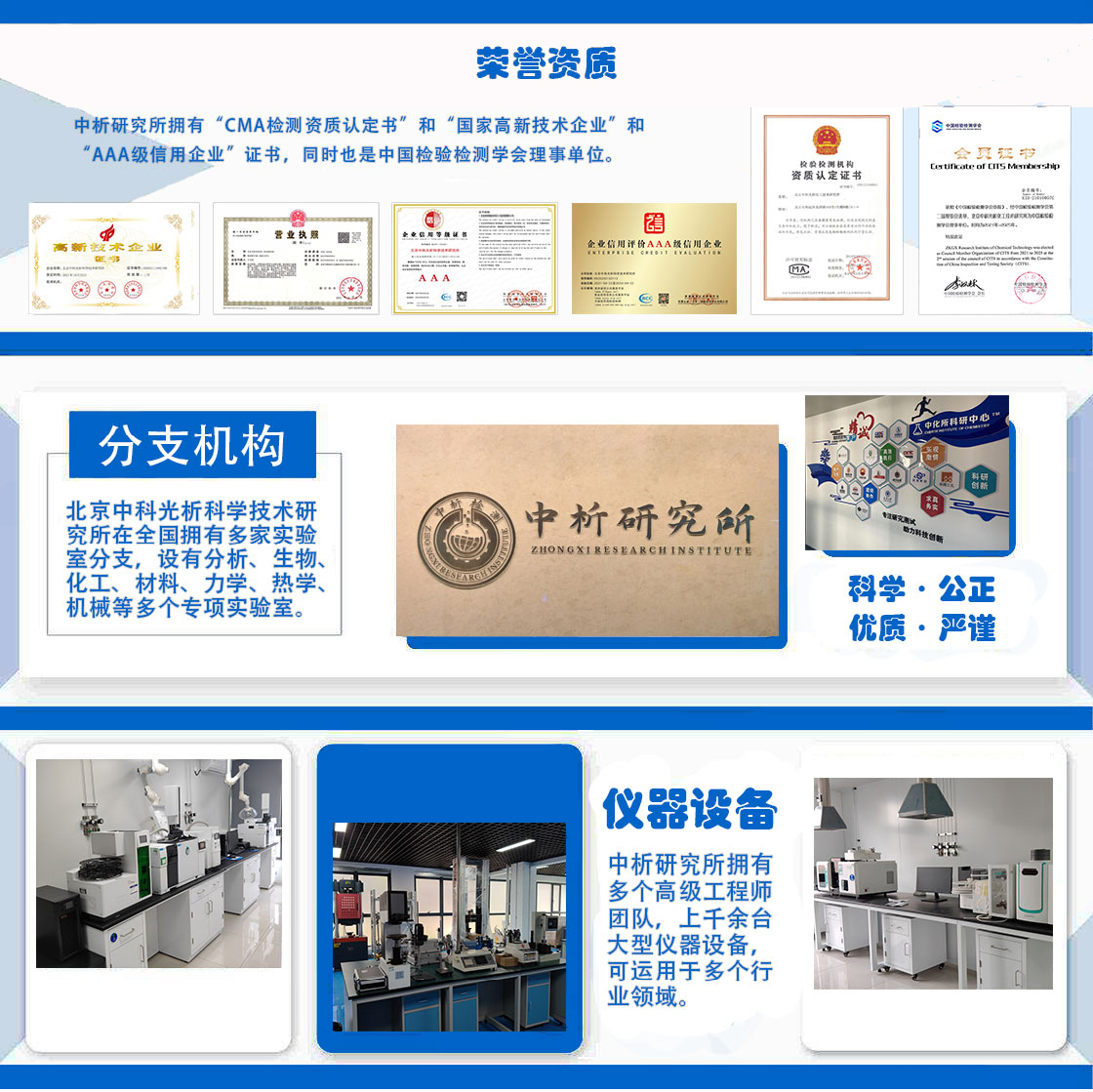
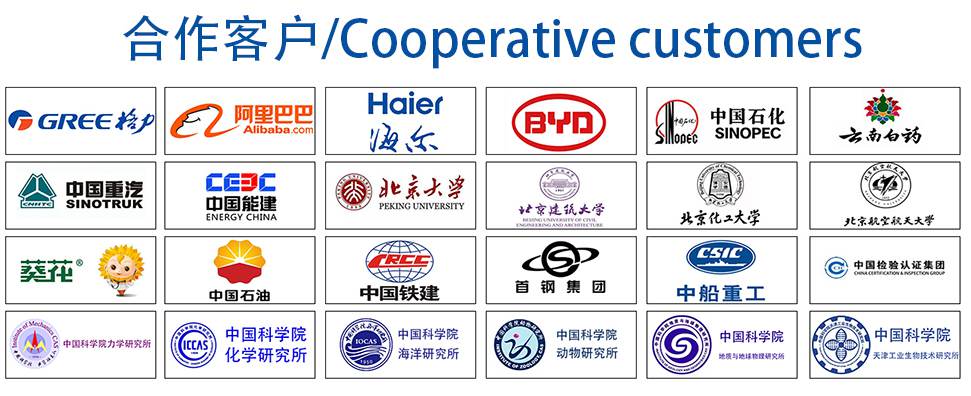