三牙轮钻头检测的重要性与核心内容
三牙轮钻头作为石油钻井、地质勘探等领域的关键工具,其性能直接影响钻探效率与安全性。在高强度作业中,钻头需承受高温、高压、高扭矩及复杂地层的剧烈冲击,长期使用易导致牙轮磨损、轴承失效、齿面断裂等问题。因此,定期开展三牙轮钻头的系统性检测是保障设备可靠性、延长使用寿命、降低作业事故风险的必要手段。检测过程需覆盖结构完整性、材料性能、动态运行状态等多个维度,并结合专业设备和行业标准进行全面评估。
三牙轮钻头核心检测项目
1. 牙轮结构完整性检测
通过渗透探伤(PT)、超声波探伤(UT)或磁粉探伤(MT)技术,检查牙轮本体、轴承座及螺纹连接部位是否存在裂纹或变形。重点分析牙轮齿圈与轴孔的配合间隙,确保无松动或异常磨损。同时使用三维扫描仪对比设计参数,评估几何尺寸偏差是否在允许范围内。
2. 牙轮齿面磨损与损伤检测
采用高精度显微镜或轮廓仪对牙齿表面进行定量分析,测量齿高、齿宽及齿尖角的磨损量,计算剩余寿命。针对硬质合金齿的脱落、崩裂现象,需通过金相分析判断材料疲劳程度。对于金刚石复合片(PDC)钻头,还需检测复合层的结合强度和热损伤情况。
3. 轴承系统性能检测
拆解后检查滚柱轴承、滑动轴承的磨损痕迹与润滑状态,使用塞规测量轴向/径向游隙,判断是否超出API标准。通过振动频谱分析或X射线检测轴承内部缺陷,模拟加载试验验证其承载能力与旋转灵活性。密封系统的气密性测试也需同步进行,防止泥浆侵入导致润滑失效。
4. 动平衡与连接部件检测
利用动平衡机测试钻头高速旋转时的振动幅值,确保重心偏移量符合ISO 1940标准。检查钻头体与牙轮轴的花键、销孔配合状态,评估螺纹连接的预紧力与抗扭强度。同时需验证喷嘴流道的通畅性及耐冲蚀性能,防止因堵塞导致水力效率下降。
5. 材料硬度与金相分析
通过洛氏硬度计或显微硬度仪检测牙轮基体、齿材及轴承部件的硬度分布,对比原始设计指标。金相显微镜下观察材料晶粒度、碳化物分布及热处理效果,排查过热、脱碳等异常组织,确保材料韧性、耐磨性满足极端工况需求。
检测结果应用与维护建议
基于检测数据生成详尽的评估报告,量化剩余使用寿命并提出修复或更换建议。对于轻度磨损的钻头,可通过堆焊、涂层强化等技术进行再生处理;严重损伤的部件则需强制报废。建立检测数据库有助于优化钻头选型与作业参数,最终实现降本增效的目标。
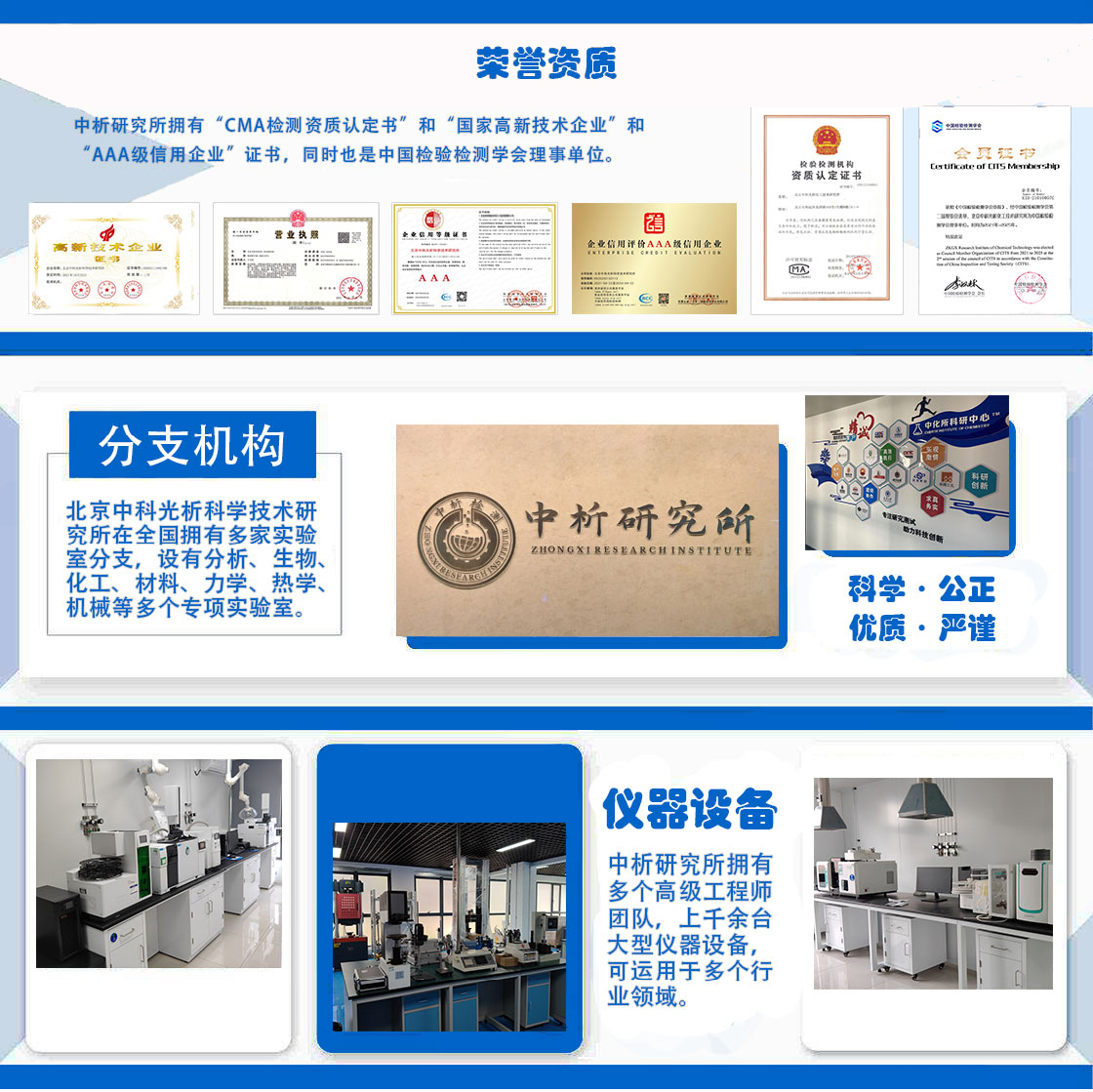
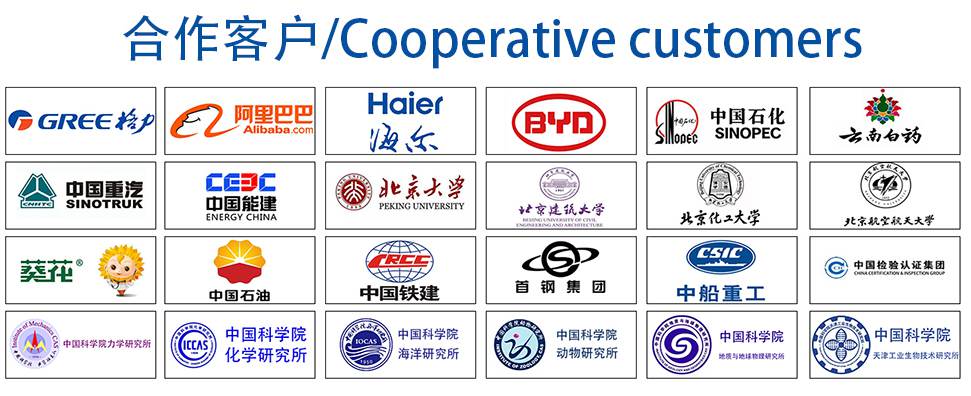