合金样品检测的关键项目与技术应用
在工业生产和材料研发中,合金作为重要的结构材料,广泛应用于航空航天、汽车制造、电子元件及能源装备等领域。合金样品的性能直接关系到产品的安全性、可靠性和使用寿命,因此对其成分、物理性能及微观结构的检测至关重要。通过科学的检测手段,不仅能验证合金是否符合设计标准,还能发现潜在缺陷,优化生产工艺。目前,合金样品检测的核心项目主要包括成分分析、力学性能测试、金相组织观察、耐腐蚀性评估以及无损检测等。以下将对这些检测项目展开详细阐述。
1. 成分分析(化学成分检测)
成分分析是合金检测的基础环节,主要目的是确定材料中元素的种类及含量。通过光谱分析法(如ICP-OES、XRF)、化学滴定法或电子探针显微分析(EPMA),可精准测定主元素(如铁、铝、镍)和微量元素的配比。例如,钛合金中氧、氮的含量若超标,会导致材料脆性增加;而铝合金中硅含量的偏差可能影响其铸造性能。成分检测数据不仅是判定合金牌号的依据,也为后续加工工艺提供调整方向。
2. 力学性能测试
力学性能测试通过模拟实际工况评估合金的强度、硬度、韧性等特性。常见方法包括: - 拉伸试验(测定抗拉强度、屈服强度、延伸率) - 冲击试验(评价材料在低温或冲击载荷下的韧性) - 硬度测试(布氏、洛氏或维氏硬度检测) 例如,高温合金需通过蠕变试验验证其在持续负载下的抗变形能力,而汽车用铝合金轮毂需满足特定疲劳强度指标。测试结果直接影响材料在极端环境下的应用可靠性。
3. 金相组织分析
金相显微镜与扫描电镜(SEM)技术可揭示合金的微观结构特征,包括晶粒尺寸、相分布、夹杂物及缺陷形态。通过观察热处理后的组织变化(如马氏体、奥氏体转化),可优化退火、淬火工艺参数。例如,镍基高温合金中γ'相的体积分数直接影响其高温强度;铝合金中析出相的形态则与耐腐蚀性密切相关。金相分析为改进材料性能提供微观层面的直接证据。
4. 耐腐蚀性评估
合金的耐腐蚀性能需通过盐雾试验、电化学极化曲线测试或长期环境暴露实验来验证。例如,不锈钢样品需在5% NaCl盐雾环境中进行96小时测试以评估抗点蚀能力;海洋工程用铜合金则需检测其在模拟海水中的电化学腐蚀速率。检测数据可指导防腐涂层选择或合金配方的优化,避免因腐蚀导致的失效风险。
5. 无损检测(NDT)
无损检测技术在不破坏样品的前提下识别内部缺陷,包括超声波检测(UT)、射线检测(RT)和涡流检测(ET)。例如,航空钛合金锻件需通过X射线检测气孔和夹杂,而焊接接头处常采用超声相控阵技术排查裂纹。NDT在保证材料完整性的同时,大幅降低生产成本,已成为高端装备制造中不可或缺的检测手段。
综合来看,合金样品检测需结合多维度数据,覆盖化学成分、宏观性能与微观结构的全面评价。选择具备CMA/ 资质的实验室,并依据GB、ASTM或ISO标准制定检测方案,可确保结果的专业性与权威性。随着智能检测设备与大数据分析技术的应用,合金检测正朝着高效化、精准化的方向持续发展。
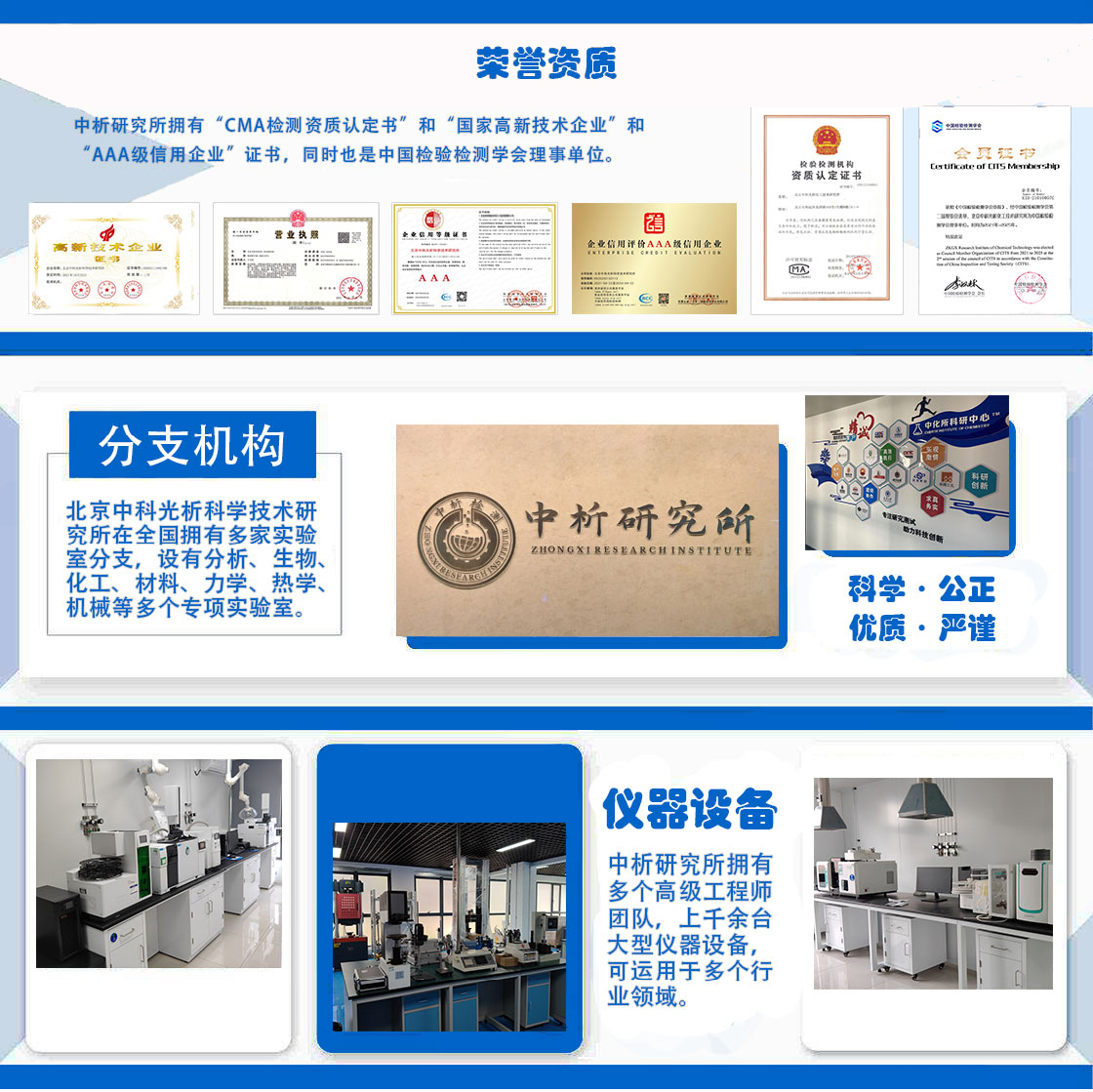
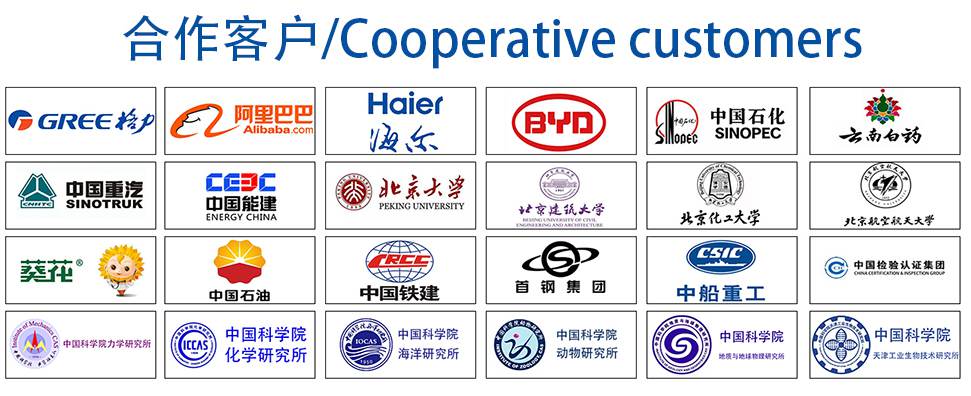