空气压缩机组及供气系统检测的重要性
空气压缩机组及供气系统作为工业生产的核心动力源,广泛应用于制造业、能源、化工、医疗等领域。其运行效率、安全性和稳定性直接关系到生产流程的连续性和设备寿命。由于系统长期处于高压、高温和高负荷工况,内部组件易出现磨损、泄漏、积碳等问题,可能导致能源浪费、设备故障甚至安全事故。因此,定期开展系统性检测是保障设备高效运行、降低运维成本、满足环保与安全规范的必要手段。
核心检测项目及技术要求
1. 机组运行参数监测
包括压缩机排气压力、温度、电流、振动值等关键参数的实时采集与分析,需对照设备铭牌额定值及行业标准(如GB/T 15487-2015)进行偏差评估。使用红外测温仪、振动分析仪等工具可精准识别轴承过热、转子不平衡等隐患。
2. 安全阀与压力容器检测
依据TSG 21-2016《固定式压力容器安全技术监察规程》,重点检查安全阀启闭压力、密封性能及校验周期,同时对储气罐进行壁厚测量(超声波测厚仪)和焊缝探伤检测,确保压力容器符合承压要求。
3. 冷却系统效能评估
通过检测冷却水流量、进出水温差(建议温差≤10℃)及散热器表面清洁度,评估换热效率。风冷系统需检测风扇转速、翅片堵塞情况,避免因散热不良导致的机组高温停机。
4. 气路系统泄漏检测
采用超声波检漏仪或皂泡法对管道、法兰、阀门等连接部位进行气密性检测。根据ISO 8573-1标准,系统泄漏量应控制在额定排气量的3%以内,超标泄漏不仅增加能耗,还会缩短压缩机加载周期。
5. 压缩空气品质分析
使用露点仪、油分检测仪等设备检测出口空气的含水量(压力露点≤-20℃)、含油量(Class 1级≤0.01mg/m³)及颗粒物浓度(Class 2级≤1μm),确保符合ISO 8573洁净度等级要求,避免对气动元件造成污染。
6. 控制系统功能验证
模拟测试压力开关、温度传感器、联锁保护装置的响应精度和及时性,重点校验压力容器的自动泄压功能与电机过载保护机制,确保控制逻辑符合GB 50029-2014设计规范。
检测周期与维护建议
常规检测应每季度实施1次,关键部件(如安全阀、压力表)需按法规要求强制年检。建议建立设备健康档案,结合运行数据分析预测性维护节点。对于老旧机组,检测频率应提高至每月1次,重点关注缸体磨损量(塞尺测量)与阀片密封性等衰退指标。通过科学的检测与维护,可使系统能效提升15%-30%,故障率降低40%以上。
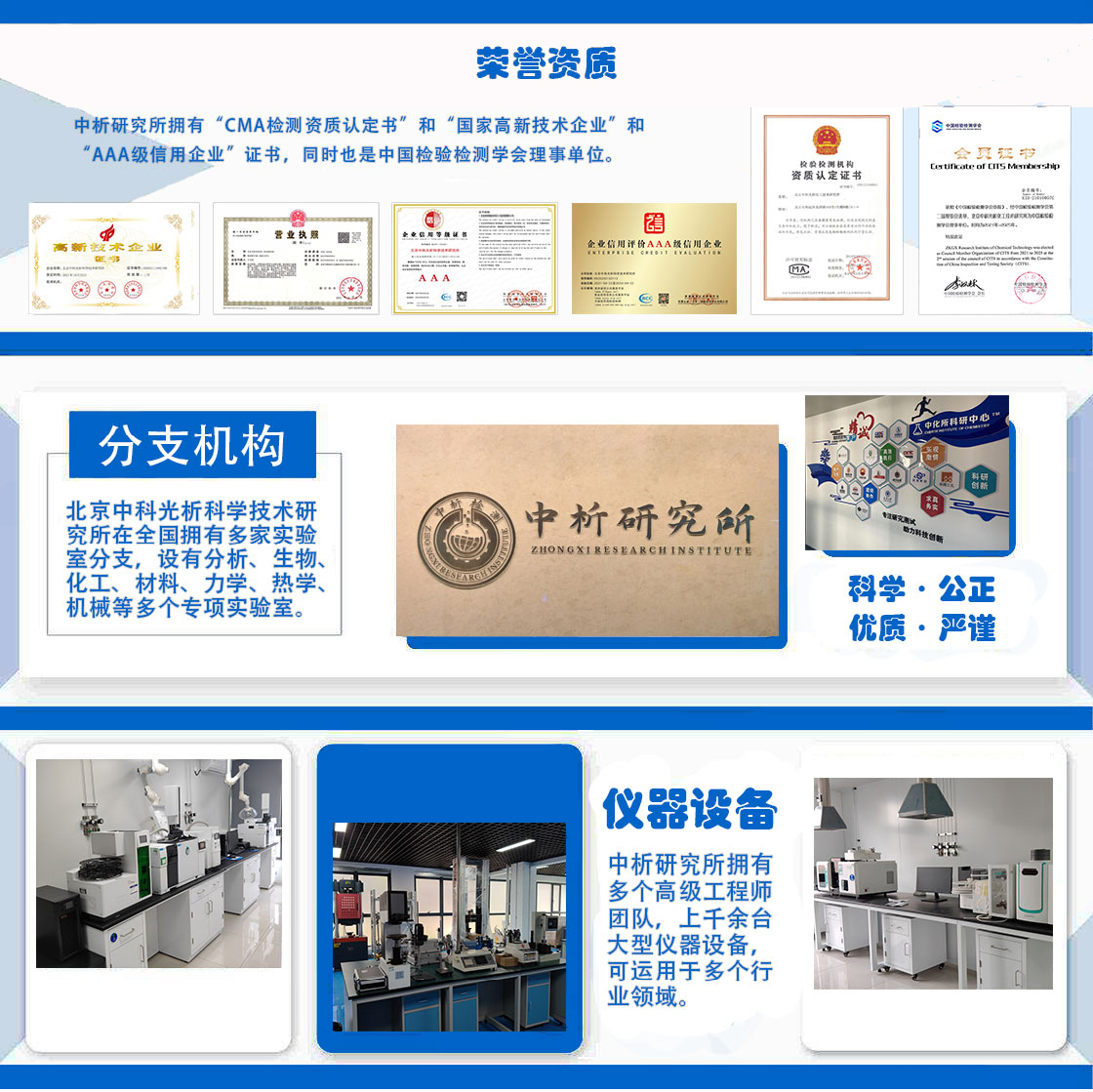
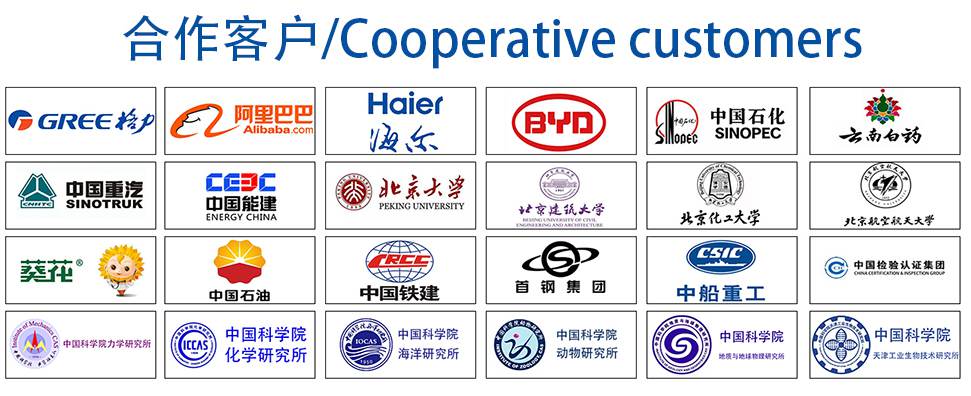