碳钢与低合金钢检测的重要性
碳钢和低合金钢是工业领域中应用最广泛的金属材料之一,尤其在机械制造、压力容器、管道工程、桥梁建筑及汽车制造等领域占据重要地位。碳钢以铁和碳为主要成分,通过调整碳含量(通常0.02%~2.1%)可实现不同强度和韧性的平衡。低合金钢则在碳钢基础上添加少量合金元素(如锰、铬、镍、钼等),以提高耐蚀性、耐磨性或高温性能。然而,材料的性能受成分、加工工艺及热处理状态的影响显著,因此需要通过科学检测确保其符合设计标准和使用要求。检测过程不仅关乎产品质量,更直接涉及设备安全性、使用寿命及经济成本控制。
主要检测项目及方法
1. 化学成分分析
化学成分是决定材料性能的核心因素。检测时需精确测定碳(C)、锰(Mn)、硅(Si)、硫(S)、磷(P)等主量元素,以及铬(Cr)、镍(Ni)、钼(Mo)等合金元素的含量。常用方法包括:
- 光谱分析法(如直读光谱仪OES):快速无损,适用于生产现场;
- 化学滴定法:精度高,用于仲裁检测;
- X射线荧光光谱(XRF):适用于表面成分分析。
2. 力学性能测试
力学性能直接反映材料承载能力,关键指标包括:
- 拉伸试验(GB/T 228.1):测定抗拉强度(Rm)、屈服强度(ReL)、断后伸长率(A)和断面收缩率(Z);
- 冲击试验(GB/T 229):通过夏比缺口试样在低温下的冲击吸收能量(KV2)评估材料韧性;
- 硬度测试:布氏(HBW)、洛氏(HRC)或维氏硬度(HV)用于评估材料表面抗变形能力。
3. 金相组织分析
通过显微镜观察材料的显微组织,判断热处理工艺的有效性:
- 晶粒度评级(GB/T 6394):影响材料的强度和韧性;
- 非金属夹杂物检测(GB/T 10561):评估硫化物、氧化物等杂质分布;
- 相组成分析:识别铁素体、珠光体、贝氏体或马氏体的比例及形态。
4. 无损检测(NDT)
在不破坏材料的前提下探测内部及表面缺陷:
- 超声波检测(UT):用于发现内部裂纹、夹层等缺陷;
- 射线检测(RT):通过X/γ射线成像检测焊缝质量;
- 磁粉检测(MT)与渗透检测(PT):针对表面及近表面裂纹检测。
5. 耐腐蚀性能测试
针对低合金钢的耐环境腐蚀能力进行评价:
- 盐雾试验(GB/T 10125):模拟海洋大气环境下的耐蚀性;
- 晶间腐蚀试验(GB/T 4334):评估不锈钢及合金钢的晶界腐蚀倾向;
- 应力腐蚀试验:检测材料在腐蚀介质与应力共同作用下的开裂敏感性。
6. 工艺性能试验
验证材料在加工过程中的适用性:
- 弯曲试验:检测材料弯曲成型时的抗开裂能力;
- 焊接性试验:包括冷裂纹敏感性测试(如斜Y型坡口试验);
- 扩口/压扁试验:评估管材的塑性变形能力。
检测标准与质量控制
检测过程需严格遵循国家标准(GB)、行业标准(如JB)或国际标准(ISO、ASTM、EN)。例如,压力容器用钢需符合NB/T 47008-2017,而结构钢检测则参照GB/T 1591。企业应建立从原材料入厂到成品出厂的全流程质量监控体系,结合第三方检测报告与内部实验室数据,确保材料性能的可靠性和一致性。
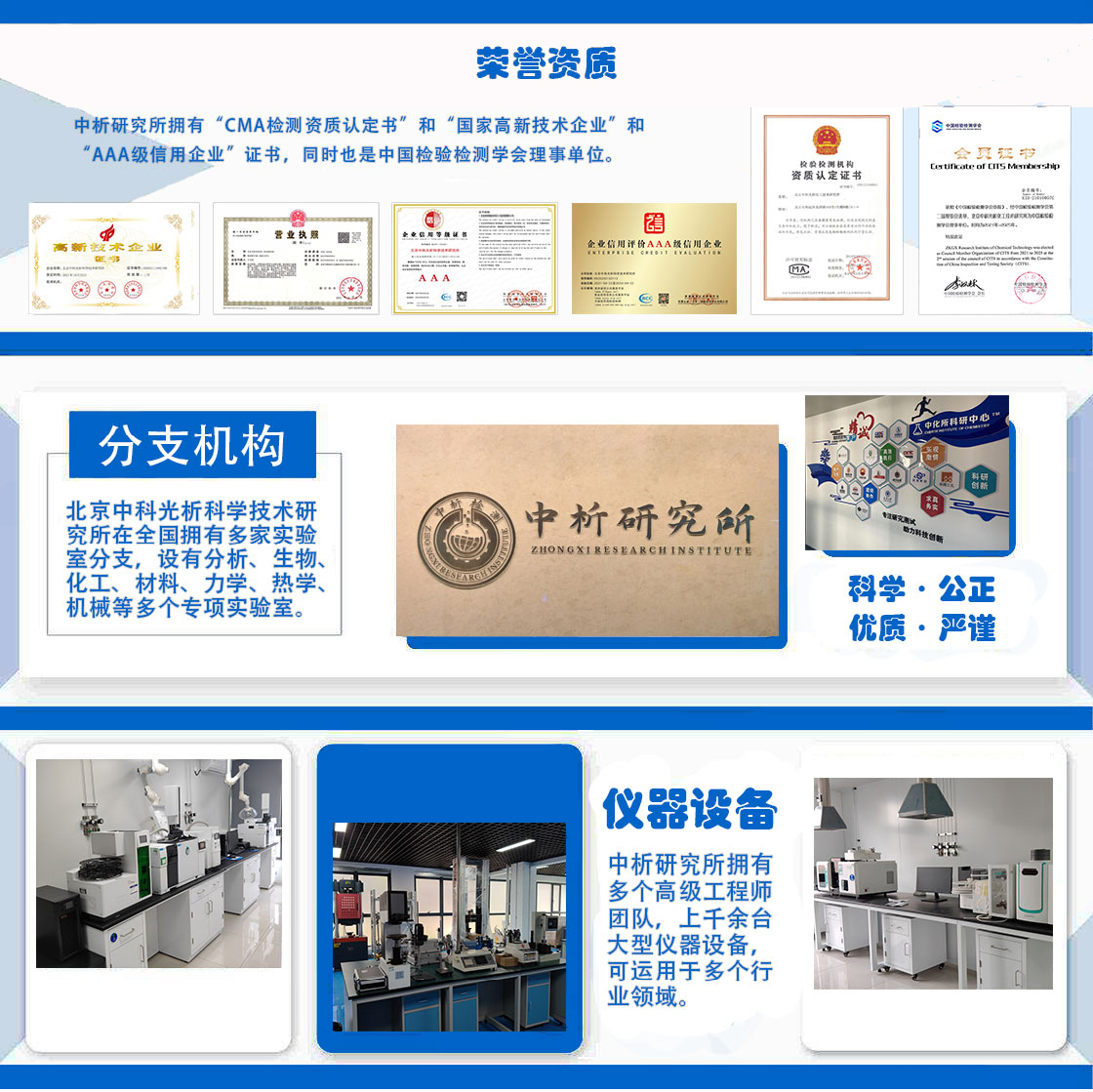
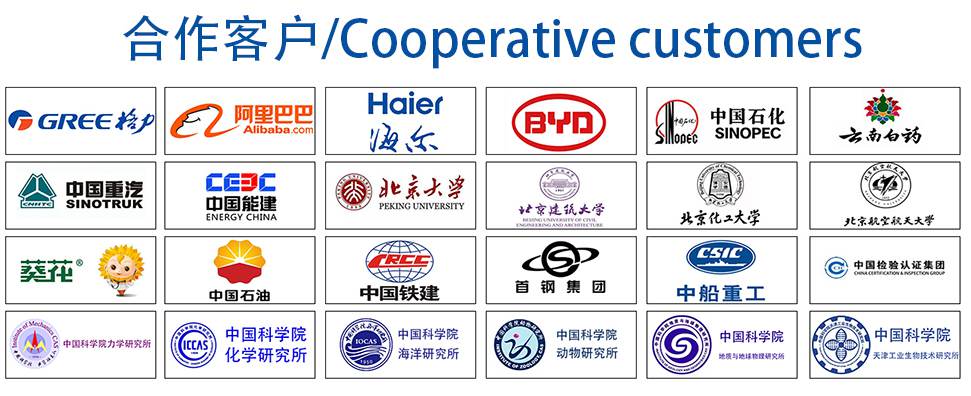