航空用钛及钛合金棒材和锻坯检测的重要性
钛及钛合金因其高强度、低密度、耐高温和优异的抗腐蚀性能,被广泛应用于航空发动机、机身结构件、起落架等关键部件。在航空领域,材料的安全性和可靠性是首要考量。由于钛合金制品在极端工况(如高温、高压、高速)下运行,任何微小的缺陷都可能引发灾难性后果。因此,对钛及钛合金棒材和锻坯进行严格的检测是确保飞行安全的核心环节。检测过程需贯穿原材料采购、加工成型到成品验收的全生命周期,涵盖化学成分、力学性能、微观组织、缺陷控制等多维度指标。
关键检测项目及技术方法
1. 化学成分分析
钛合金的性能高度依赖其元素配比,例如Ti-6Al-4V(TC4)需精准控制铝、钒的含量范围。通过直读光谱仪(OES)或X射线荧光光谱仪(XRF)进行元素定量分析,确保符合AMS 4928、ASTM B348等标准要求。尤其需检测杂质元素(如Fe、C、N、H)的含量,氢含量过高会导致氢脆问题。
2. 力学性能测试
包括拉伸强度、屈服强度、延伸率、冲击韧性及硬度测试。通过万能材料试验机、夏比冲击试验机等设备,模拟材料在静态和动态载荷下的表现。例如,航空锻坯需满足室温抗拉强度≥895 MPa(依据AMS 4928),同时在高温环境下(如300°C)仍需保持稳定性。
3. 显微组织分析
利用金相显微镜、扫描电镜(SEM)观察材料的晶粒尺寸、相分布及α/β相比例。通过腐蚀试样并依据ASTM E3标准制备金相样品,评估是否存在过热组织、偏析或异常析出相。细小的等轴晶结构通常预示更好的疲劳性能。
4. 无损检测(NDT)
采用超声波检测(UT)、渗透检测(PT)和射线检测(RT)识别内部裂纹、气孔或夹杂物。超声波的探头频率需根据材料厚度调整(如5-10 MHz),灵敏度需满足AMS 2630标准。对于复杂形状锻坯,工业CT可提供三维缺陷成像。
5. 尺寸与形位公差检测
使用三坐标测量机(CMM)或激光扫描仪验证棒材直径、锻坯轮廓度及表面粗糙度。例如,航空紧固件用钛棒需满足±0.05 mm的直径公差,而涡轮盘锻坯的同心度偏差需小于0.1 mm。
6. 表面质量检测
通过目视检查、涡流检测或磁粉检测(适用于钛合金表面镀层)排查表面裂纹、折叠或氧化层。酸洗(按AMS 2488标准)可暴露微裂纹,而电子背散射衍射(EBSD)可分析表层晶粒取向变化。
7. 特殊环境性能测试
针对航空使用场景,需增加高温蠕变试验(如ASTM E139)、应力腐蚀试验(ASTM G34)及疲劳寿命测试(按ASTM E466进行高周疲劳测试)。例如,发动机压气机叶片需在500°C下承受10^7次循环载荷无失效。
结语
航空用钛合金的检测体系是一个多学科交叉的复杂工程,需结合材料学、力学和数字化检测技术。随着增材制造、超塑性成形等新工艺的应用,检测标准也在持续迭代。只有通过全流程、多维度的质量控制,才能保障钛合金部件在航空领域安全服役,支撑现代航空工业的高性能需求。
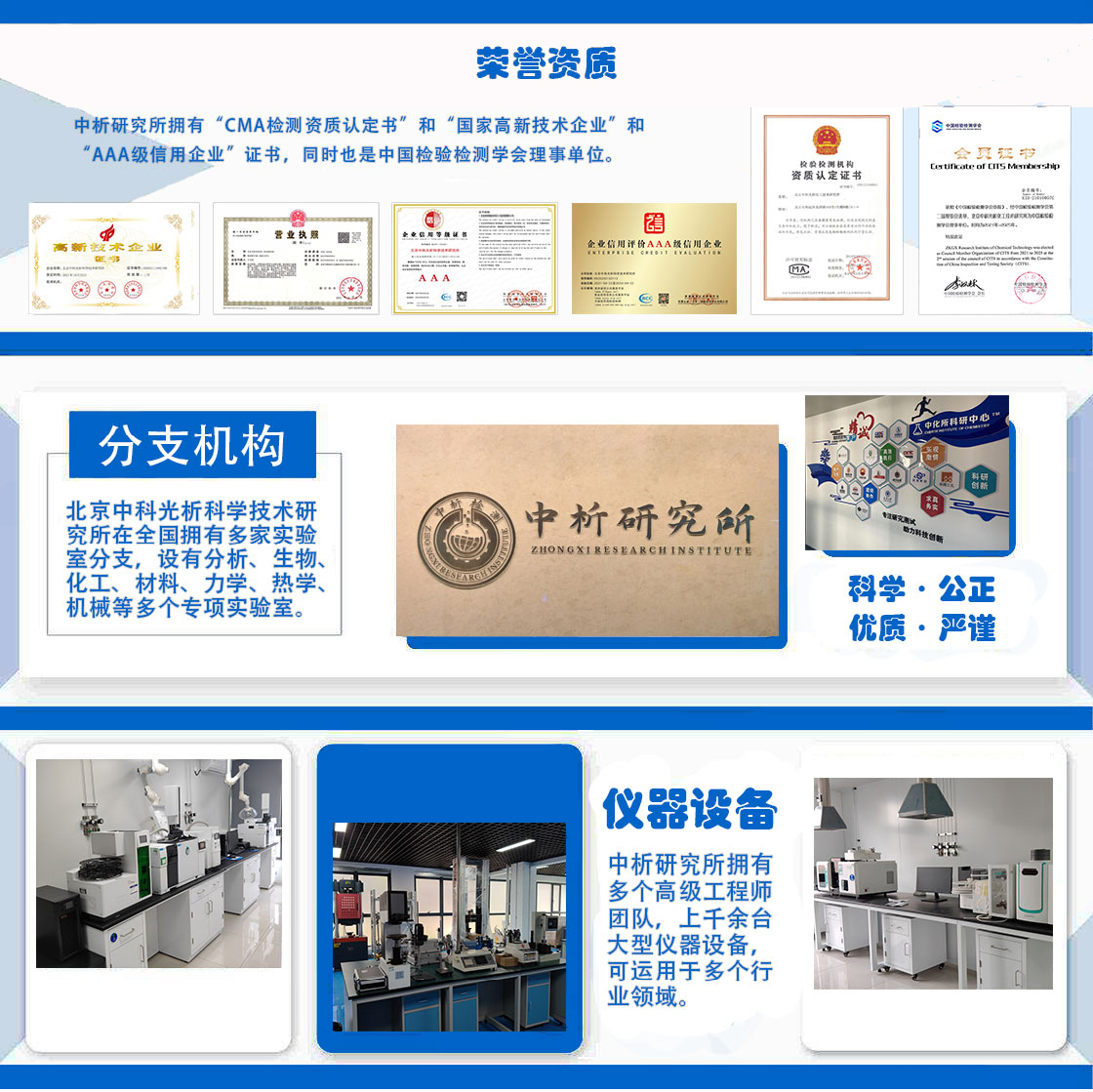
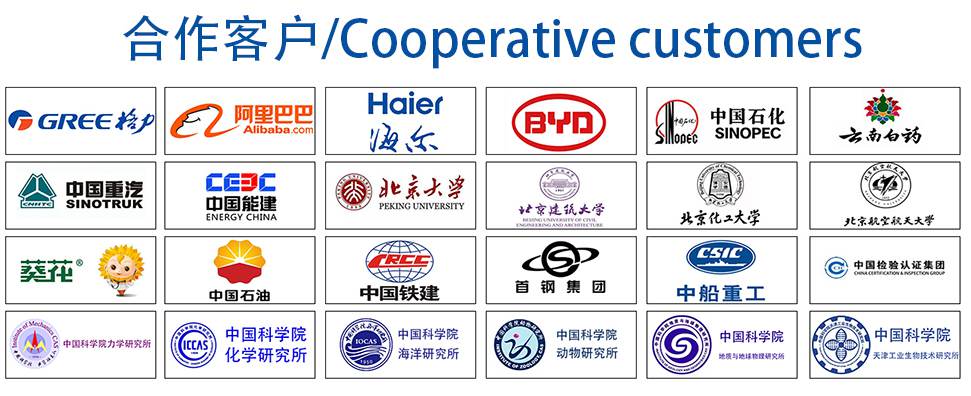