钛及钛合金棒材检测技术与质量控制体系
钛及钛合金棒材作为高端装备制造领域的核心基础材料,在航空航天、医疗器械、化工装备等行业发挥着不可替代的作用。其优异的比强度、耐腐蚀性和生物相容性等特性,决定了从原料到成品的全过程必须建立严格的质量控制体系。专业检测机构通过科学的检测项目和齐全的检测手段,可有效保障材料性能符合GB/T 2965-2020《钛及钛合金棒材》等国家标准要求,为下游应用提供可靠的质量保障。
核心检测项目体系
1. 化学成分分析:采用直读光谱仪(OES)和电感耦合等离子体发射光谱仪(ICP-OES)进行全元素检测,重点控制O、N、H等间隙元素含量,确保符合TC4、TA2等不同牌号成分标准。
2. 力学性能测试:包含室温拉伸试验(测定抗拉强度、屈服强度、断后伸长率)、高温持久强度试验及硬度测试(布氏/洛氏硬度),试样按GB/T 228.1标准要求加工制备。
3. 金相组织检测:通过光学显微镜和扫描电镜(SEM)观察α相、β相分布形态,评估晶粒度等级(按ASTM E112标准),检测显微孔隙、夹杂物等缺陷。
特殊检测项目
4. 无损检测技术:应用超声波探伤(UT)检测内部缺陷,渗透检测(PT)检查表面裂纹,涡流检测(ET)评估导电连续性,检测灵敏度需达到AMS 2630标准。
5. 尺寸与几何公差:采用三坐标测量仪进行直径偏差、直线度、圆度等形位公差检测,棒材端面切斜度控制≤2mm/m。
6. 腐蚀性能评估:依据ASTM G48标准进行点蚀试验,模拟5%NaCl溶液环境,测定临界点蚀温度(CPT),医用材料需额外进行细胞毒性测试。
质量控制关键点
检测过程需严格遵循ISO/IEC 17025体系要求,热处理工艺验证应包括β相变点测定和时效处理效果评估。对于航空级棒材,需增加疲劳性能测试和断裂韧性(KIC)试验。现代检测实验室已普遍配置带EBSD功能的场发射电镜,可实现晶体取向的数字化分析。
通过建立从熔炼批号追溯、中间品管控到成品全检的完整质量档案,配合X射线荧光光谱(XRF)现场快速筛查,可构建起多维度的质量防护网,确保每批钛合金棒材的性能稳定性和质量一致性。随着智能制造技术的发展,基于机器视觉的自动化检测系统和AI缺陷识别算法正在成为行业升级的新方向。
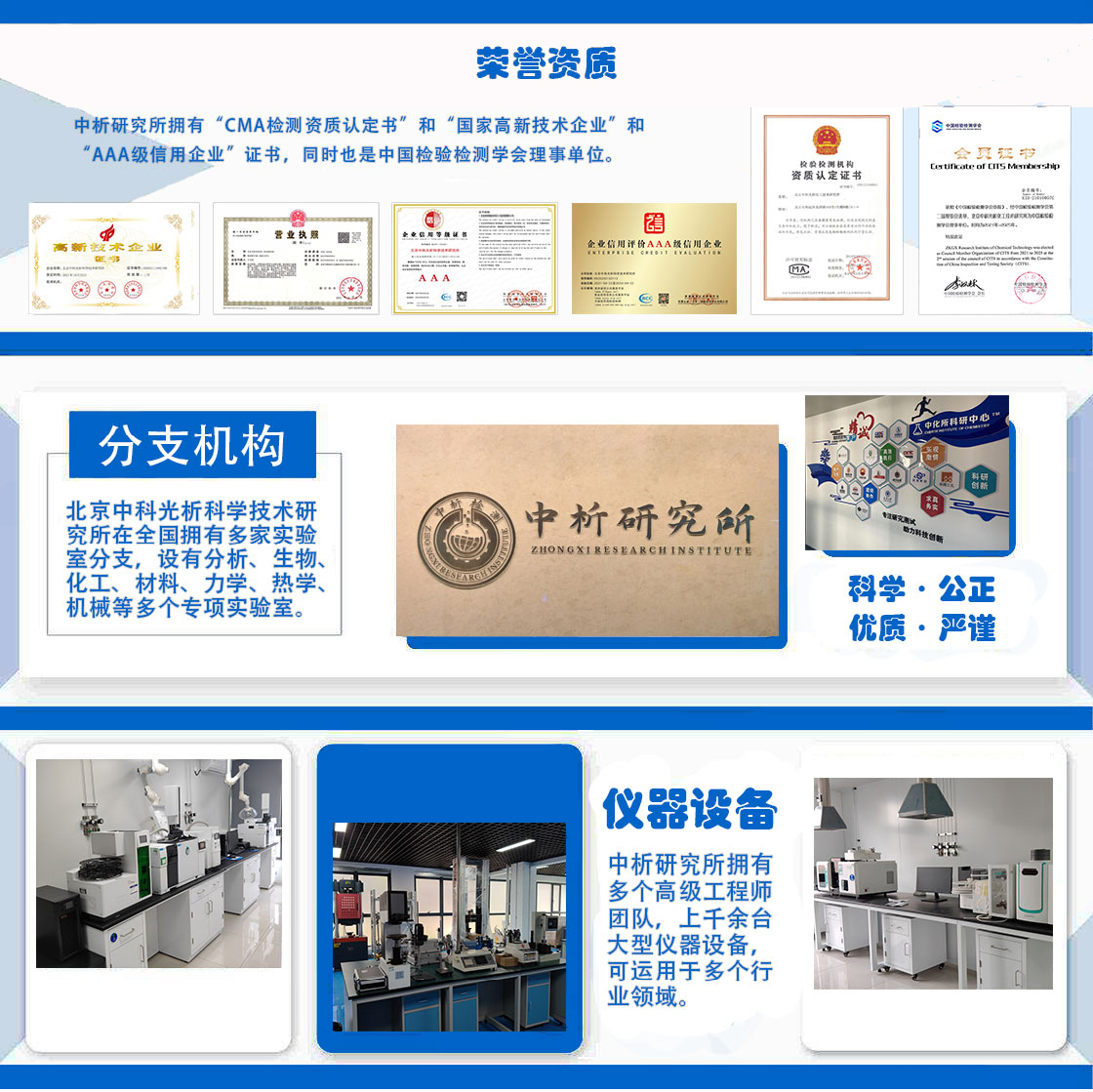
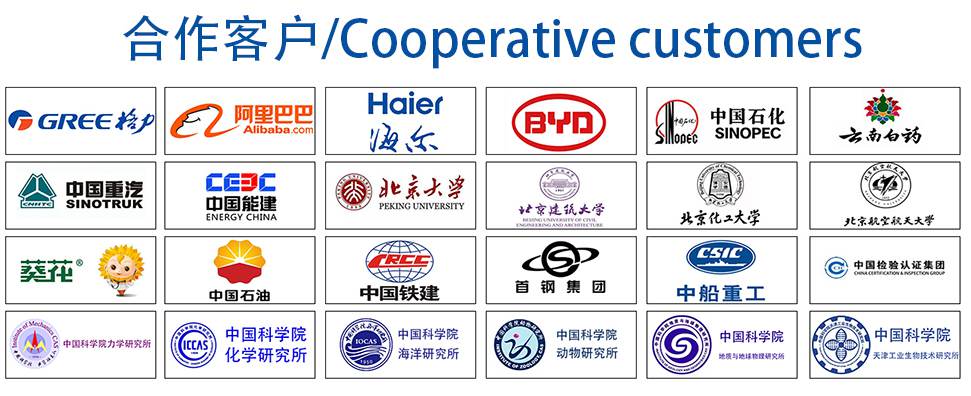