可溶桥塞检测的重要性与核心内容
可溶桥塞作为一种在油气井压裂作业中广泛应用的临时封隔工具,其性能直接关系到施工安全与作业效率。它通过溶解技术实现无干预回收,避免了传统桥塞需钻磨清除的复杂流程。随着页岩油气开发的深入,可溶桥塞的检测需求日益增长,检测项目涵盖材料特性、机械性能、溶解速率、环境适应性等关键指标,确保其在不同工况下的可靠性。完整的检测体系不仅能为产品研发提供数据支撑,更是保障井下作业安全的重要技术手段。
材料成分与溶解性能检测
通过X射线荧光光谱(XRF)和能谱分析(EDS)验证合金配比,确保材料符合可溶性设计标准。溶解实验模拟地层环境,在设定温度(通常90-150℃)、矿化度(3%-7% KCl溶液)下测试全溶解时间,要求48-120小时内完成可控分解。溶解残留物需进行粒径分布分析,确保不产生堵塞孔隙的碎屑。
机械强度测试体系
采用三轴应力试验机开展复合加载测试,包括:1)轴向抗压强度(≥70MPa) 2)径向抗剪切强度(≥50MPa)3)抗冲击性能(落锤试验10次无结构破损)。同步进行蠕变试验,验证长期承压(35MPa持续72小时)下的形变率需<0.5%。
密封性能验证方案
构建高温高压密封测试系统,在模拟井筒条件下进行:① 正向压力密封(工作压力42MPa)② 反向压差测试(压差25MPa)③ 循环压力波动实验(200次±5MPa脉动)。要求泄漏量<5mL/min,橡胶元件在120℃热老化后仍保持90%以上压缩回弹率。
环境适应性评估
涵盖温度交变测试(-20℃至150℃循环20次)、酸性介质浸泡(pH=3溶液48h)、H2S/CO2腐蚀试验(按NACE TM0177标准)。检测项目包括质量损失率(<1%)、表面腐蚀等级(不超过GB/T 16545 2级)、应力腐蚀开裂敏感性等指标。
现场应用模拟测试
在实验井筒中复现真实作业工况,包括:1)坐封压力响应曲线监测 2)多级压裂冲击模拟(累计等效20段压裂)3)复合振动环境下的结构完整性测试。通过声发射技术实时监测微观裂纹扩展情况,建立失效预警模型。
检测标准与质量管理
检测体系需符合API 11D1/ISO 14310 V0级标准,同步执行ASTM E8/E18材料试验规范。建立全生命周期质量追溯系统,每个桥塞附带独立检测报告,包含300+项过程数据,实现从原材料到成品的数据链闭环管理。
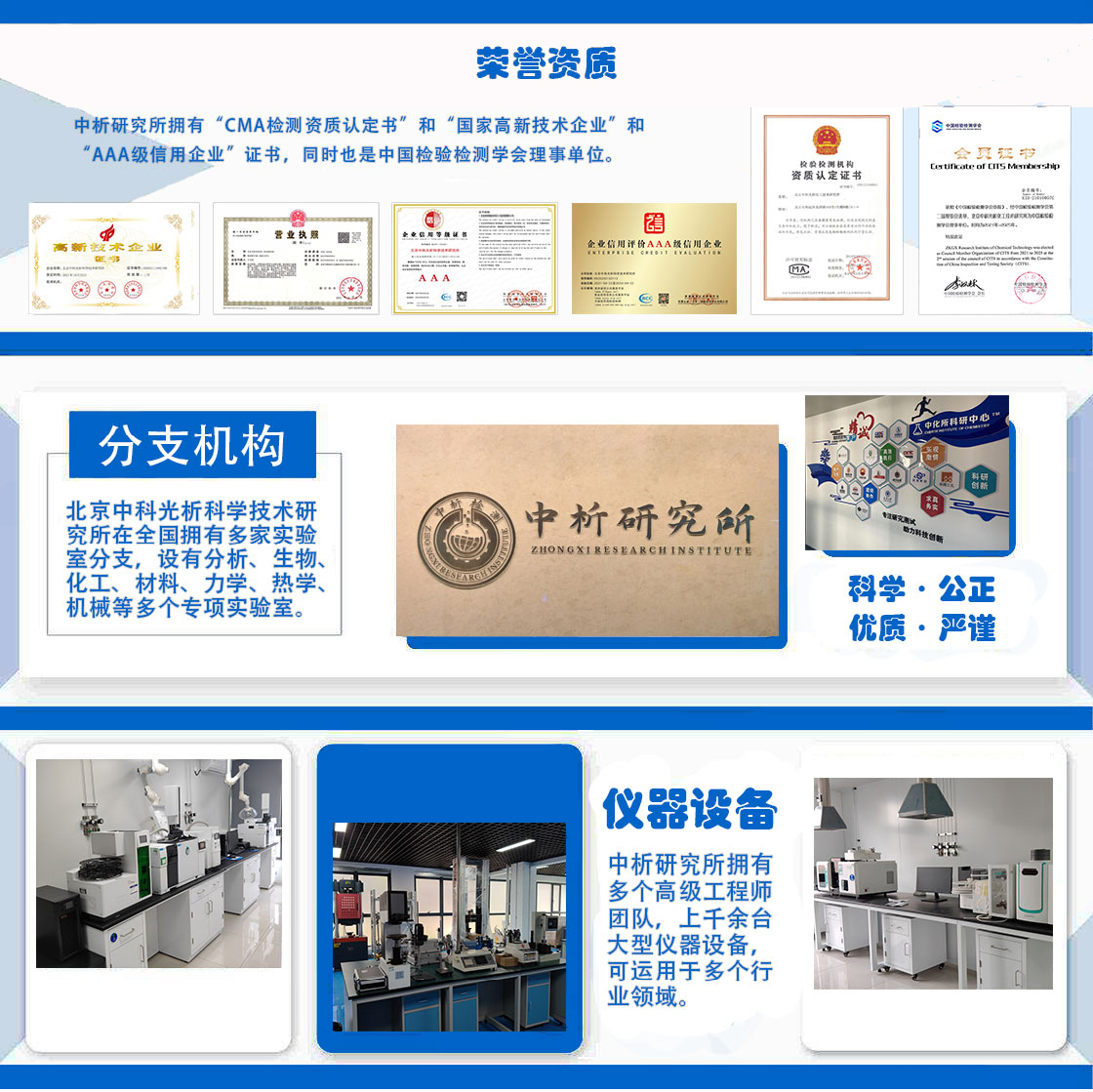
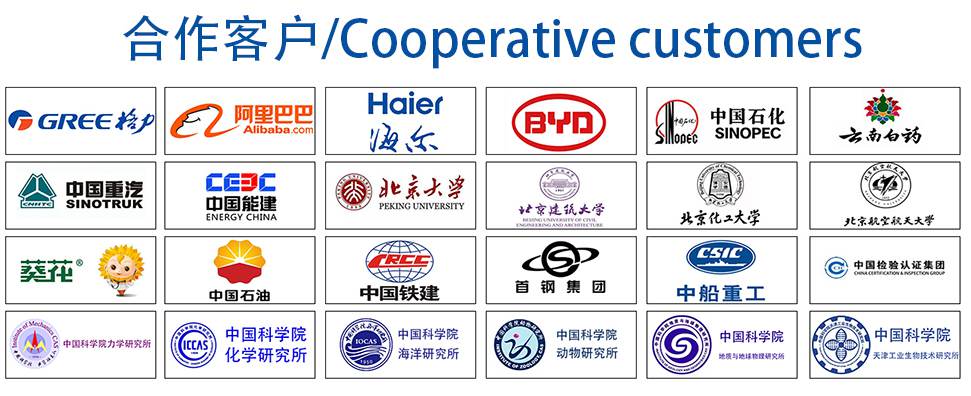