抽油杆吊卡检测项目及技术要点解析
在石油开采作业中,抽油杆吊卡作为连接抽油杆与提升设备的核心承重部件,其性能直接影响井下作业安全及生产效率。该装置长期承受交变载荷、腐蚀介质及机械磨损,需定期开展系统性检测。根据GB/T 20970-2020《石油天然气工业用吊卡》等标准要求,完整的抽油杆吊卡检测体系包含以下核心项目:
一、外观质量检测
通过目视检查与磁粉探伤结合的方式,重点检测吊卡体表面是否存在裂纹、变形、腐蚀坑等缺陷。要求工作表面粗糙度≤Ra6.3μm,非工作面≤Ra12.5μm,关键部位不允许存在深度超过0.5mm的机械损伤。
二、尺寸公差检测
使用三坐标测量仪验证关键尺寸:吊卡开口尺寸偏差≤±0.1mm,锁紧机构配合间隙≤0.05mm,本体厚度偏差控制在±5%以内。特别关注使用中出现尺寸变化的易磨损区域。
三、材料性能检测
对吊卡本体取样进行光谱分析,验证材料成分是否符合40CrMo或35CrMo材质要求。通过金相检验确认热处理状况,硬度值应达到HRC28-35范围,冲击功≥35J(-20℃条件下)。
四、承载能力试验
在液压试验台上进行静载试验,加载至额定载荷的1.5倍保持3分钟,要求无永久变形。动态疲劳测试需模拟实际工况,完成10^5次循环加载后检查结构完整性。
五、功能性检测
着重验证锁紧机构的可靠性:在振动台上模拟井口工况,检查锁舌自动复位功能;进行500次开合寿命测试,测量操作手柄力矩变化值不超过初始值的20%。
六、无损探伤检测
采用超声波检测内部缺陷,对焊缝区域进行100%射线检测。根据NB/T 47013标准评定缺陷等级,Ⅱ级区域不允许存在条状缺陷,点状缺陷当量直径≤2mm。
通过上述系统化检测,可有效评估抽油杆吊卡的剩余使用寿命,及时发现潜在失效风险。建议每季度开展常规检测,大修周期不超过2年,对于已服役超过5万小时的设备应增加检测频次。规范的检测流程不仅能预防井下事故,更能延长关键设备服役周期,为油田安全生产提供可靠保障。
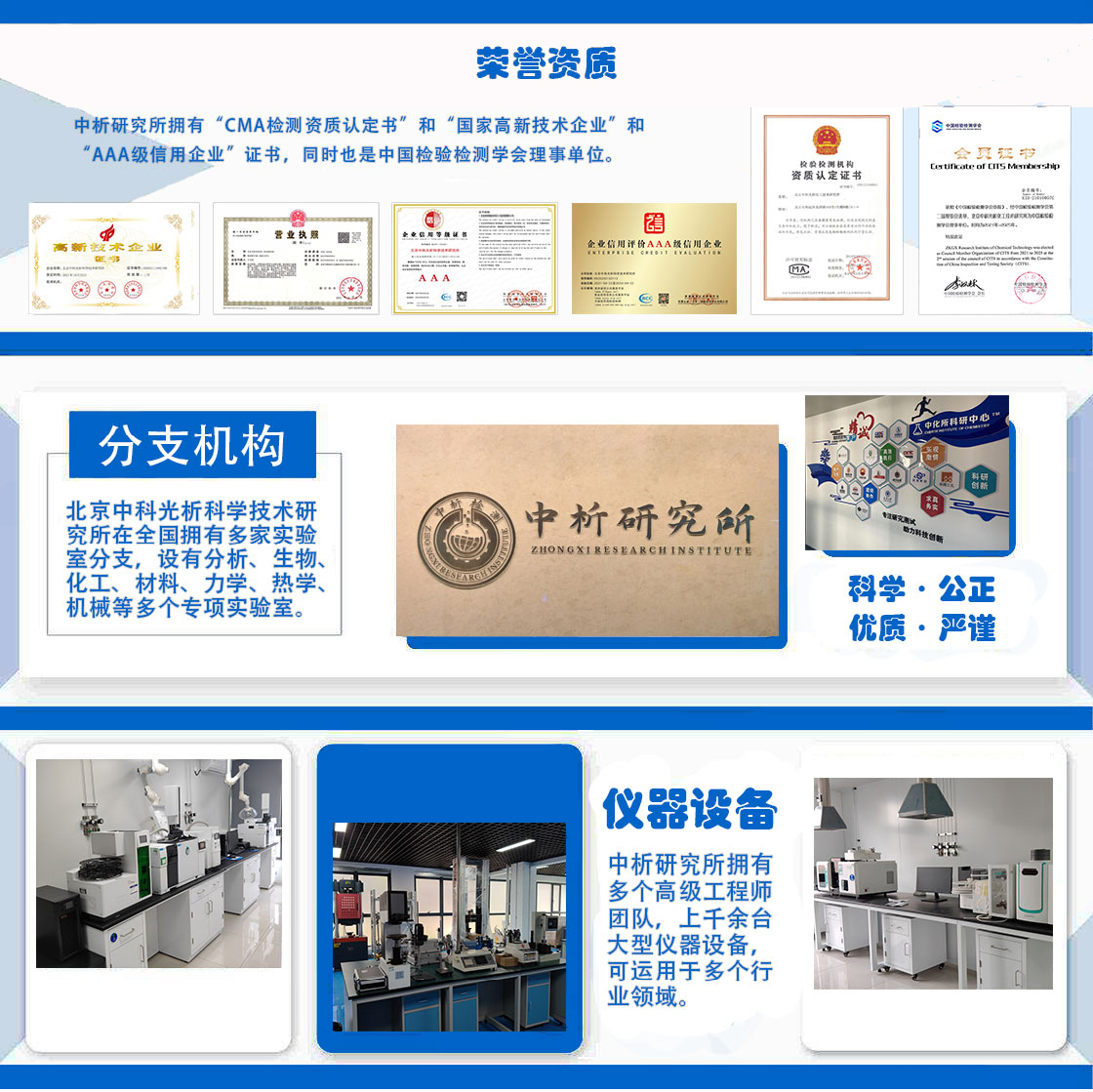
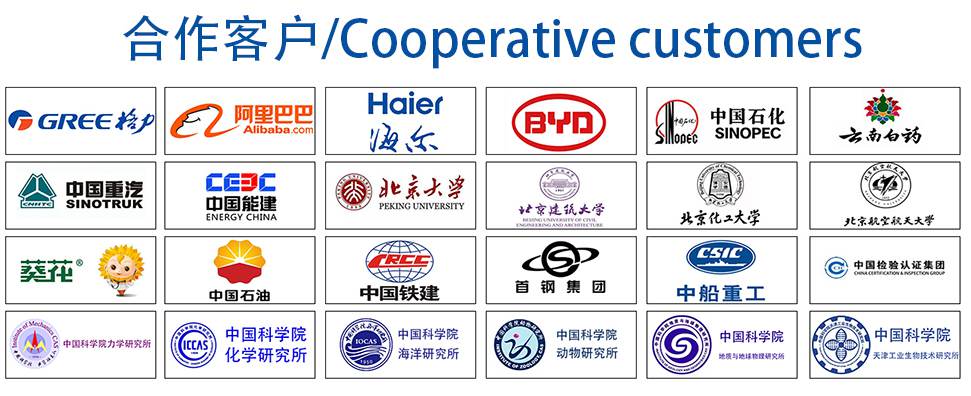