交流发电机用调节器检测项目详解
交流发电机调节器作为保障电力系统稳定运行的核心部件,承担着控制发电机输出电压、防止过充或欠压的关键任务。其性能直接影响发电机组的供电质量、蓄电池寿命及车载电气设备的安全性。为确保调节器在复杂工况下的可靠性,需通过系统性检测验证其功能参数。以下针对调节器检测的关键项目展开详细说明。
一、电压调节精度测试
通过模拟不同转速与负载条件,检测调节器能否将输出电压稳定在设定范围内(通常为28V±0.5V)。使用可编程电源和示波器记录电压波动曲线,验证稳压精度是否达到<1.5%的行业标准,确保在发动机转速突变时仍能维持稳定输出。
二、温度特性测试
在-40℃至+85℃温控箱中连续工作8小时,监测电压漂移量。优质调节器应具备温度补偿功能,保证高温环境下不超压、低温时快速建立电压。重点验证热敏元件灵敏度及散热结构有效性。
三、动态响应特性检测
采用突加载/卸载测试仪模拟大功率设备启停,检测电压恢复时间。标准要求负载突增时电压跌落≤15%,并在0.3秒内恢复至正常值。此项测试可暴露调节器响应延迟或功率管过载等隐患。
四、保护功能验证
包括过压保护(>32V自动断电)、短路保护(输出端短接不烧毁)、反接保护(电池极性接反时电路自锁)三项强制检测。使用故障注入系统模拟异常工况,验证保护电路响应速度及自恢复能力。
五、电磁兼容性测试
在电波暗室中执行辐射抗扰度(≥100V/m)和传导干扰测试,确保调节器在强电磁环境下不误动作,同时自身产生的电磁干扰符合GB18655标准。特别关注PWM调压电路的高频噪声抑制性能。
六、耐久性试验
在85℃高温环境下进行500小时老化测试,模拟10万次载荷循环。检测后需重新验证所有性能参数,评估触点磨损、电容容量衰减、半导体器件热疲劳等潜在失效模式。
通过上述检测流程可全面评估调节器的综合性能。建议每2年或车辆行驶5万公里后实施预防性检测,结合示波器波形分析和红外热成像技术,实现故障的早期预警,避免因调节器失效导致发电机系统崩溃。
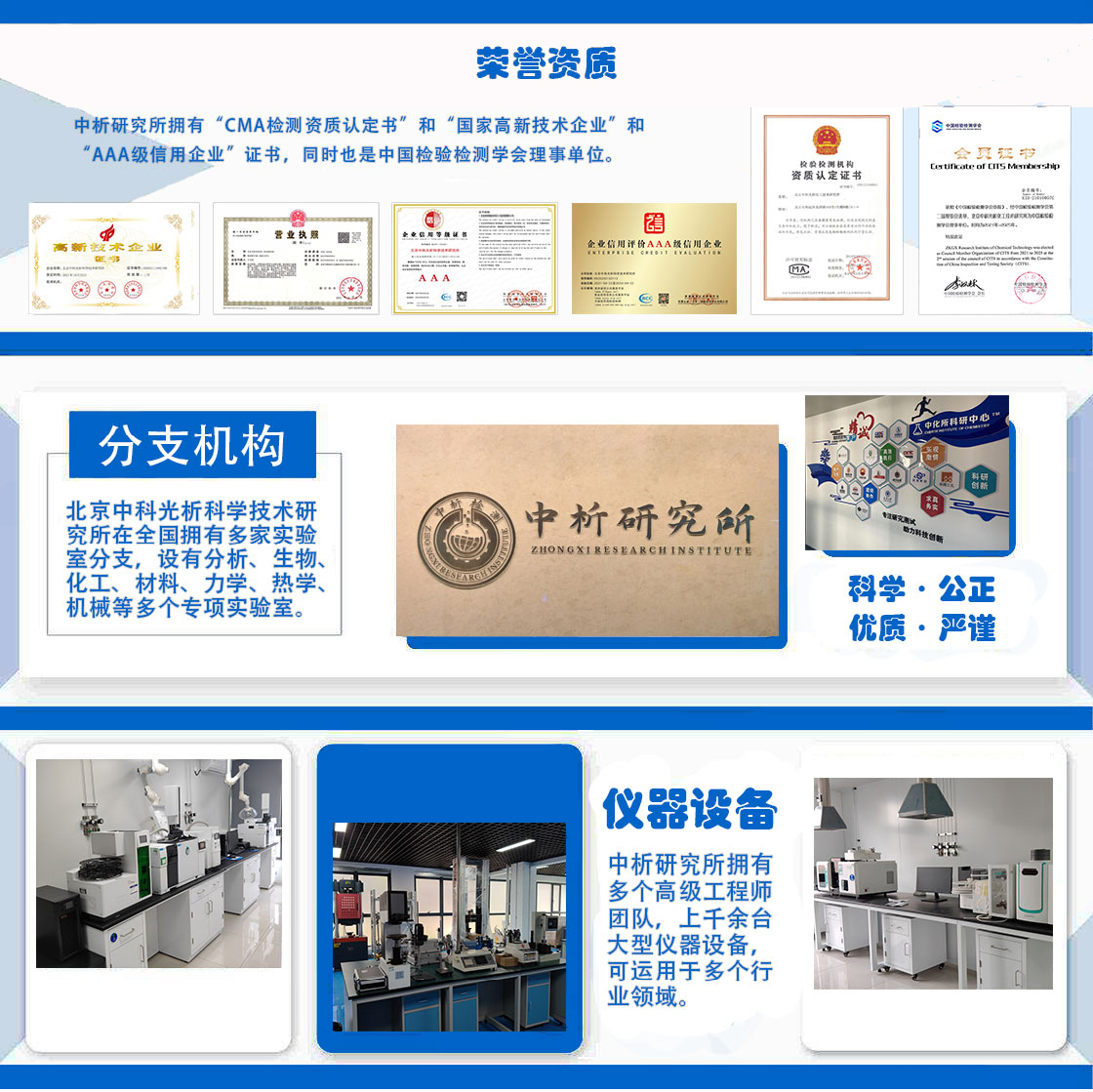
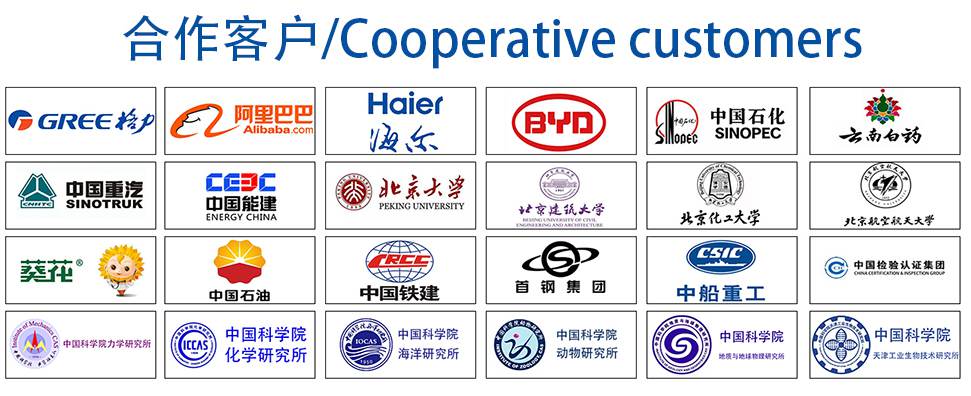