铸锻件检测的关键项目与应用价值
铸锻件作为机械制造、能源设备、轨道交通等领域的基础零部件,其质量直接影响设备性能与安全。铸锻件检测是通过科学手段对材料成分、内部结构、力学性能及表面缺陷进行全面分析的过程,旨在确保产品符合行业标准(如ASTM、ISO、GB等)和实际使用需求。随着工业技术升级,检测手段从传统目视检查发展为多维度、高精度的综合评估体系,涉及化学成分、无损探伤、金相组织等多个核心项目。以下将重点解析铸锻件检测的关键技术环节及其工程意义。
1. 材料成分分析与均匀性检测
铸锻件的化学成分直接影响其力学性能和耐腐蚀性。通过光谱分析仪(如OES)、X射线荧光光谱(XRF)或化学滴定法,精确测定碳、锰、硅、硫、磷等元素的含量,确保符合材料标准(如20CrMo、304不锈钢等)。同时需检测成分分布的均匀性,避免偏析问题导致局部性能下降。
2. 力学性能测试
力学性能是评价铸锻件承载能力的关键指标,主要包括: • 拉伸试验:测定抗拉强度、屈服强度及断后伸长率; • 冲击试验(如夏比冲击):评估低温环境下的韧性; • 硬度测试(布氏/洛氏/维氏):反映材料耐磨性与加工硬化程度。
3. 无损检测(NDT)技术应用
无损检测用于发现内部缺陷而不破坏工件,常用方法包括: • 超声波检测(UT):识别气孔、夹杂、裂纹等深层缺陷; • 射线检测(RT):通过X射线或γ射线成像观察内部结构; • 磁粉检测(MT)与渗透检测(PT):检测表面及近表面微小裂纹。
4. 金相组织与微观结构分析
通过金相显微镜或电子显微镜观察晶粒大小、相组成及非金属夹杂物分布。例如,锻件中的流线方向需与受力方向一致,铸件应避免出现疏松、缩孔等铸造缺陷。热处理方法(如正火、淬火)的合理性也可通过金相检验验证。
5. 尺寸精度与形位公差检测
使用三坐标测量仪(CMM)、激光扫描仪等设备,对铸锻件的几何尺寸、平面度、圆度、同轴度等进行精密测量,确保装配兼容性。尤其对于涡轮盘、曲轴等复杂部件,公差需控制在微米级。
6. 耐腐蚀性与高温性能测试
针对特殊工况的铸锻件,需进行盐雾试验、晶间腐蚀试验或高温蠕变试验,模拟实际环境下的材料稳定性。例如,核电阀门锻件需通过应力腐蚀开裂(SCC)评估。
铸锻件检测贯穿设计验证、生产监控到成品验收的全生命周期,是保障工业装备安全运行的核心环节。通过多技术融合的检测体系,企业可有效降低质量风险、提升产品竞争力,同时为工艺优化提供数据支持。
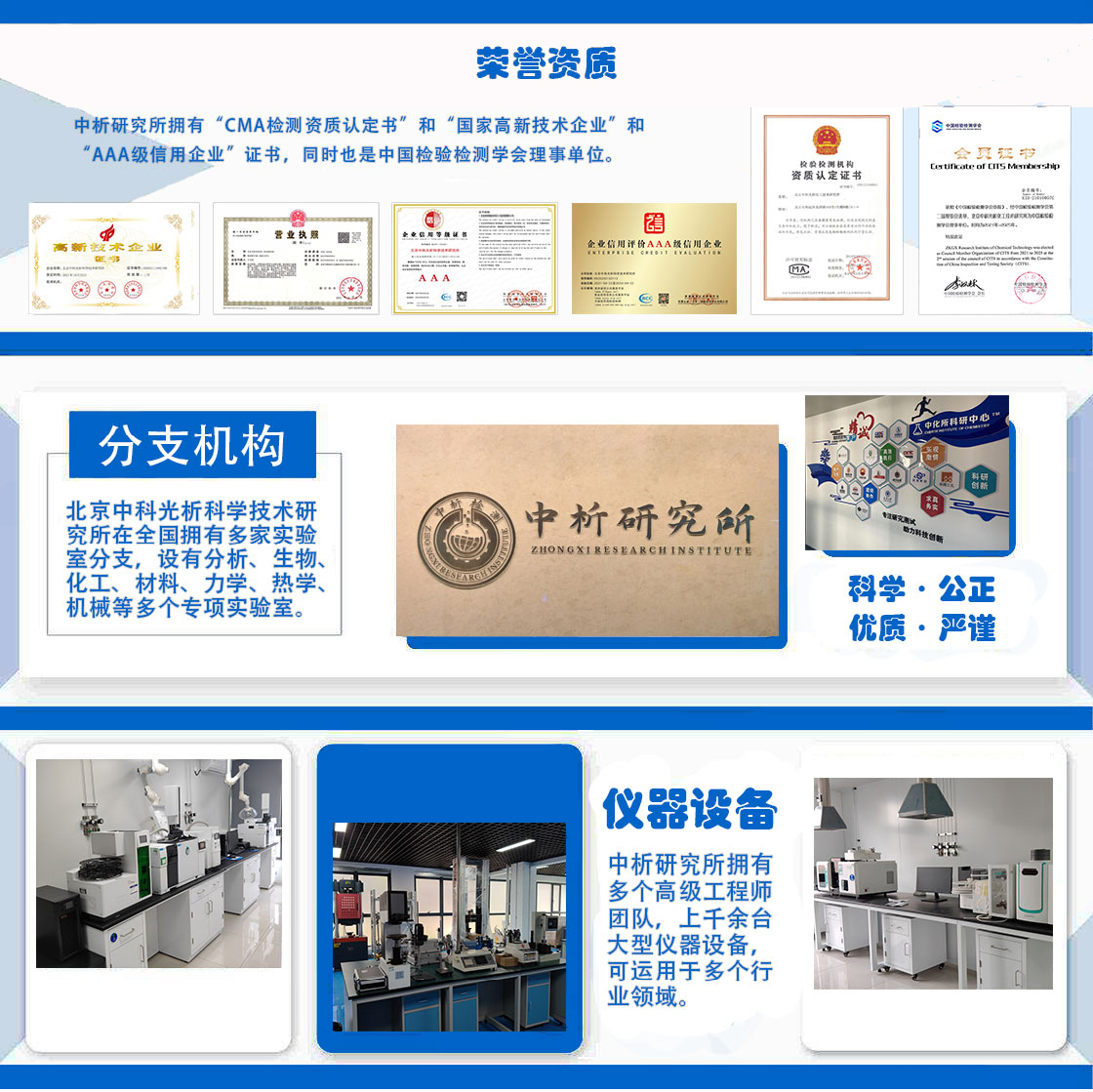
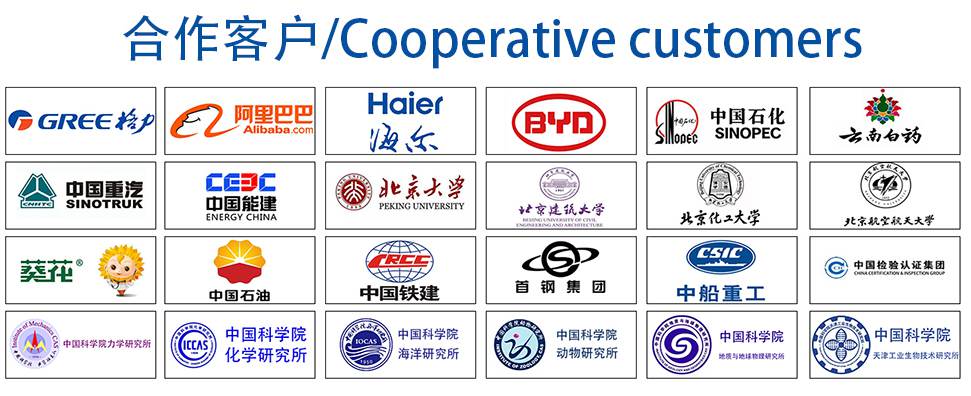