螺旋压力机检测的重要性及检测项目解析
螺旋压力机作为金属成型加工领域的核心设备,广泛应用于汽车配件、航空航天零部件、五金工具等行业的锻造、冲压及校直工艺。其通过螺旋副传动将电动机的旋转运动转化为滑块的直线运动,具有能量可控、冲击力大、成形精度高等特点。为确保设备运行稳定性、工艺精度及操作安全性,定期开展螺旋压力机检测已成为企业设备管理与质量控制的关键环节。
一、运行参数检测
1. 压力输出检测:通过应变式传感器和动态数据采集系统,测量实际输出压力与标称值的偏差,误差应控制在±5%以内;
2. 行程精度检测:使用激光位移传感器校准滑块行程重复定位精度,确保上下死点位置偏差≤0.1mm;
3. 打击能量测试:采用能量测试仪验证飞轮储存动能与实际释放能量的匹配度,避免能量不足或过载。
二、结构部件检测
1. 螺杆-螺母副检测:通过三维坐标测量仪检测螺纹磨损量,当螺距累积误差超过0.3mm/m需更换;
2. 导轨间隙检测:使用塞尺测量滑块导轨配合间隙,径向间隙应≤0.08mm,轴向间隙≤0.05mm;
3. 机身刚性测试:采用动态应变仪监测满载工况下的机身变形量,主框架应力值不得超过材料屈服强度的60%。
三、控制系统检测
1. 电气安全检测:包括绝缘电阻(≥1MΩ)、接地连续性(≤0.1Ω)等参数测量;
2. 控制精度验证:通过编程模拟多组工艺参数,检测实际动作与指令的响应时间差(应≤50ms);
3. 过载保护测试:人为设置超载工况,验证液压过载保护装置的反应速度和卸荷可靠性。
四、安全防护装置检测
1. 紧急制动系统测试:测量急停按钮触发后滑块的制动距离,400吨级设备应≤10mm;
2. 光电保护装置验证:使用专用测试棒检查安全光幕的响应时间和保护区域覆盖率;
3. 联锁装置功能检测:重点验证模具安装区防护门与设备运行的机械-电气双重联锁可靠性。
五、工艺质量检测
1. 成形件尺寸检测:随机抽取50件产品,使用三坐标测量机评估尺寸波动范围;
2. 表面质量分析:通过金相显微镜检查工件表面裂纹、折叠等缺陷发生率;
3. 模具适配性检测:测量模具安装面平面度(≤0.02mm/m)与定位销配合精度。
六、专项性能检测
1. 动态平衡测试:采用振动分析仪检测飞轮系统在额定转速下的振动烈度(应≤4.5mm/s);
2. 噪声水平测量:按照GB/T 25618标准,在操作位测量连续工作时的等效声压级(应≤85dB(A));
3. 温升试验:连续运行2小时后,检测轴承部位温度升高值(滚动轴承≤40℃,滑动轴承≤30℃)。
规范的螺旋压力机检测应遵循JB/T 9957《螺旋压力机精度》等行业标准,建议每6个月进行定期检测,大修后或生产工艺变更时需增加专项检测。通过科学的检测体系,可有效提升设备综合性能,降低非计划停机风险,同时为工艺优化提供数据支撑。
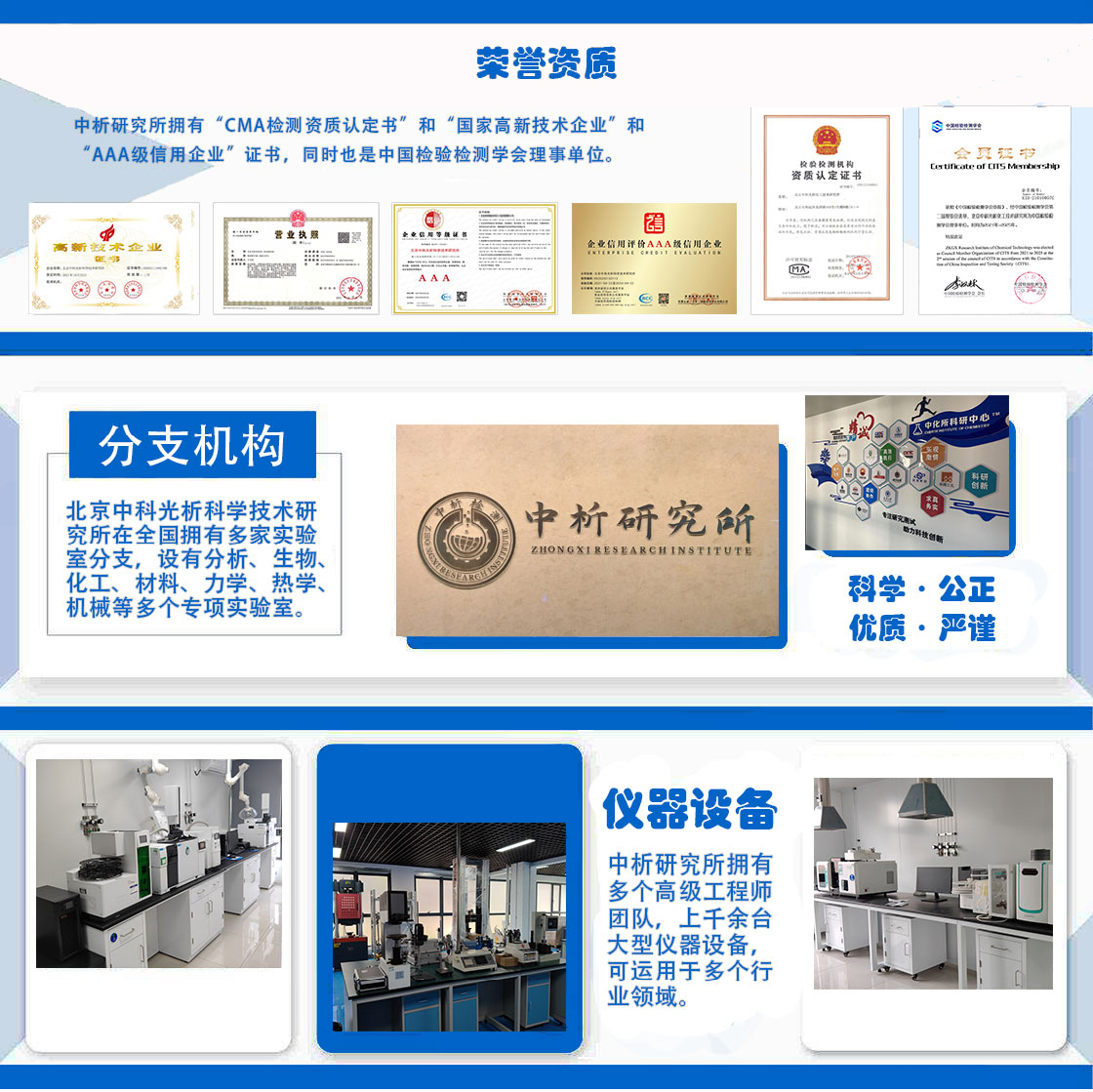
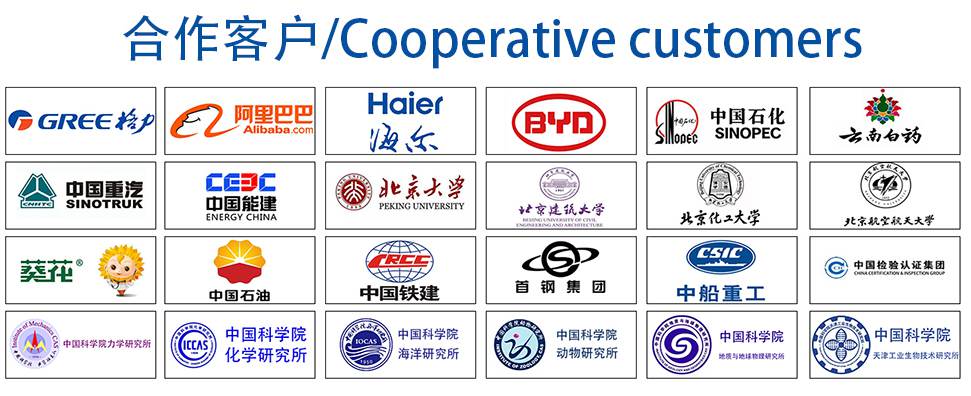