开式压力机检测的重要性与核心内容
开式压力机作为金属成型加工领域的重要设备,广泛应用于汽车制造、家电生产、航空航天等行业。其通过液压或机械传动系统对金属坯料施加压力,完成冲压、拉伸、弯曲等工艺。由于设备长期处于高负荷、高频率运行状态,安全性和稳定性直接关乎生产效率及操作人员安全。因此,定期开展开式压力机检测不仅是保障生产安全的基础要求,也是延长设备使用寿命、避免突发故障造成经济损失的关键举措。
开式压力机核心检测项目解析
1. 安全装置功能性检测
检测压力机的紧急制动系统、双手操作装置、光电保护装置是否灵敏可靠,确保制动响应时间符合GB 27607-2011《机械压力机安全技术要求》。重点验证急停按钮按下后滑块能否在5°曲轴转角内停止,并对安全门联锁装置进行反复触发测试。
2. 机械结构完整性检测
检查机身、导轨、滑块等重要承力部件是否存在裂纹或变形,使用超声波探伤仪对机身焊接部位进行无损检测。同时测量导轨平行度误差(≤0.02mm/m)、滑块与工作台面垂直度(≤0.05mm/300mm)等关键尺寸参数,确保机械精度达标。
3. 电气控制系统检测
使用绝缘电阻测试仪检测主电路绝缘电阻(≥1MΩ),验证过载保护装置动作值是否符合设定要求。通过PLC程序模拟测试各传感器(位置/压力/温度)的反馈准确性,排查线路老化或接触不良等隐患。
4. 液压/气动系统性能检测
对液压泵站进行压力-流量特性测试,检测溢流阀调定压力是否偏移。使用红外热像仪检查管路是否存在泄漏点,测量油液污染度(NAS 9级以内为合格)。气动系统需检测三联件过滤效能及气缸运动同步性。
5. 工作精度与动态性能测试
采用激光干涉仪检测滑块下死点重复定位精度(±0.02mm),进行满负荷试运行时监测振动加速度(≤4.5m/s²)。通过应变片测量关键部位的应力分布,分析设备刚性是否满足工艺要求。
6. 润滑与冷却系统检测
检查集中润滑系统的油路通畅性,检测润滑油膜厚度是否达标(≥2μm)。冷却系统需验证热交换效率,确保液压油温升不超过35℃/h,避免因过热导致密封件失效。
7. 噪声与工作环境安全评估
按照GB/T 17248.3标准进行噪声测量(空载≤85dB(A)),检测设备接地电阻(≤4Ω)。评估操作区域照明强度(≥300Lux)及紧急疏散通道设置是否符合职业健康安全规范。
检测周期与结果应用
建议每500工作小时进行常规检测,年度大修时需执行全面检测。检测数据应建立数字化档案,通过趋势分析预测部件剩余寿命。对于检测发现的导轨磨损超标、液压系统内泄等问题,需立即停机整改并重新进行验收测试。
通过系统化的检测管理,企业可降低设备故障率30%以上,同时避免因设备隐患导致的安全事故。值得注意的是,检测过程中必须遵守设备断电挂牌、能量锁定等安全规程,检测人员需持有特种设备检验资质方可开展作业。
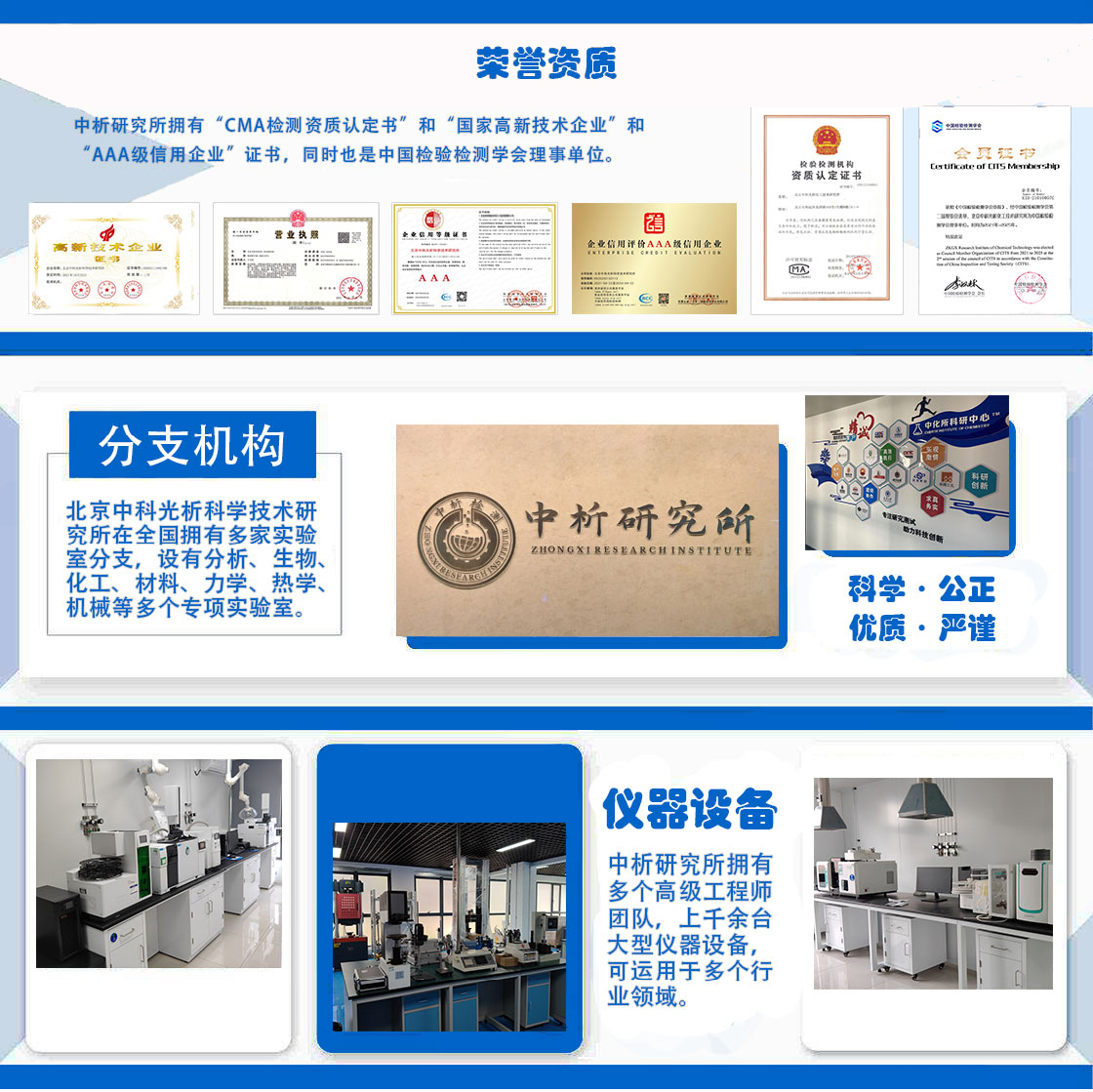
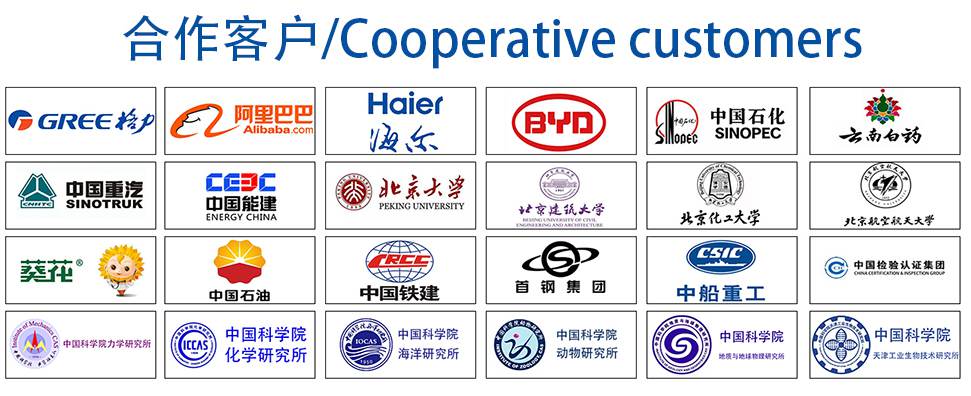