铝中间合金锭检测的关键项目与技术解析
铝中间合金锭作为铝合金生产的重要原料,其质量直接关系到下游产品的性能与稳定性。为确保其在航空航天、汽车制造、电子设备等领域的可靠应用,需通过多项专业检测验证其成分、物理特性及工艺适应性。检测过程需遵循GB/T 27677-2011《铝中间合金》等国家标准,结合行业规范与用户定制化需求,建立系统化的质量评价体系。
化学成分检测
采用电感耦合等离子体发射光谱仪(ICP-OES)和X射线荧光光谱仪(XRF)精准测定主元素(如铝、硅、镁)及杂质元素(铁、铜、锌等)含量。重点检测活性元素添加偏差,例如钛、硼、锆等细化剂元素的配比是否符合YS/T 447.1标准要求,确保合金化效果达标。
物理性能检测
通过压汞法测定合金锭密度(误差需≤0.5%),使用显微硬度计检测布氏硬度(HB值),并采用差示扫描量热仪(DSC)分析熔化温度区间。对特殊用途合金锭需额外测试热膨胀系数(20-300℃)和导电率(IACS%),确保其适用极端工况环境。
微观组织分析
应用金相显微镜(放大倍率1000×)和扫描电镜(SEM)观测晶粒尺寸(通常要求≤100μm)、第二相分布状态及夹杂物含量。通过能谱分析(EDS)确认杂质元素偏聚情况,结合ASTM E112标准评定晶粒度等级,确保组织均匀性满足深加工要求。
表面质量检验
目视检查结合工业内窥镜检测表面氧化皮厚度(应≤0.05mm)、裂纹深度(不允许贯穿性裂纹)、缩孔直径(≤2mm)及夹杂外露情况。使用超声波测厚仪核查锭体尺寸公差(长度±5mm,厚度±1.5mm),确保符合YS/T 491运输包装规范。
特殊功能验证
对于变质合金锭,需进行熔体流动性测试(螺旋试样长度≥600mm);细化剂类合金锭需开展晶粒细化效果试验(α-Al晶粒尺寸≤200μm);除气剂类产品需测定除氢效率(H含量≤0.12ml/100gAl)。
通过上述系统性检测,可全面把控铝中间合金锭的冶金质量,为后续熔铸工艺提供可靠参数依据。检测机构需定期参加CMA能力验证,确保设备计量精度满足JJF 1130要求,检测报告应包含元素偏差曲线图、金相组织照片等可视化数据,助力用户实现质量追溯与工艺优化。
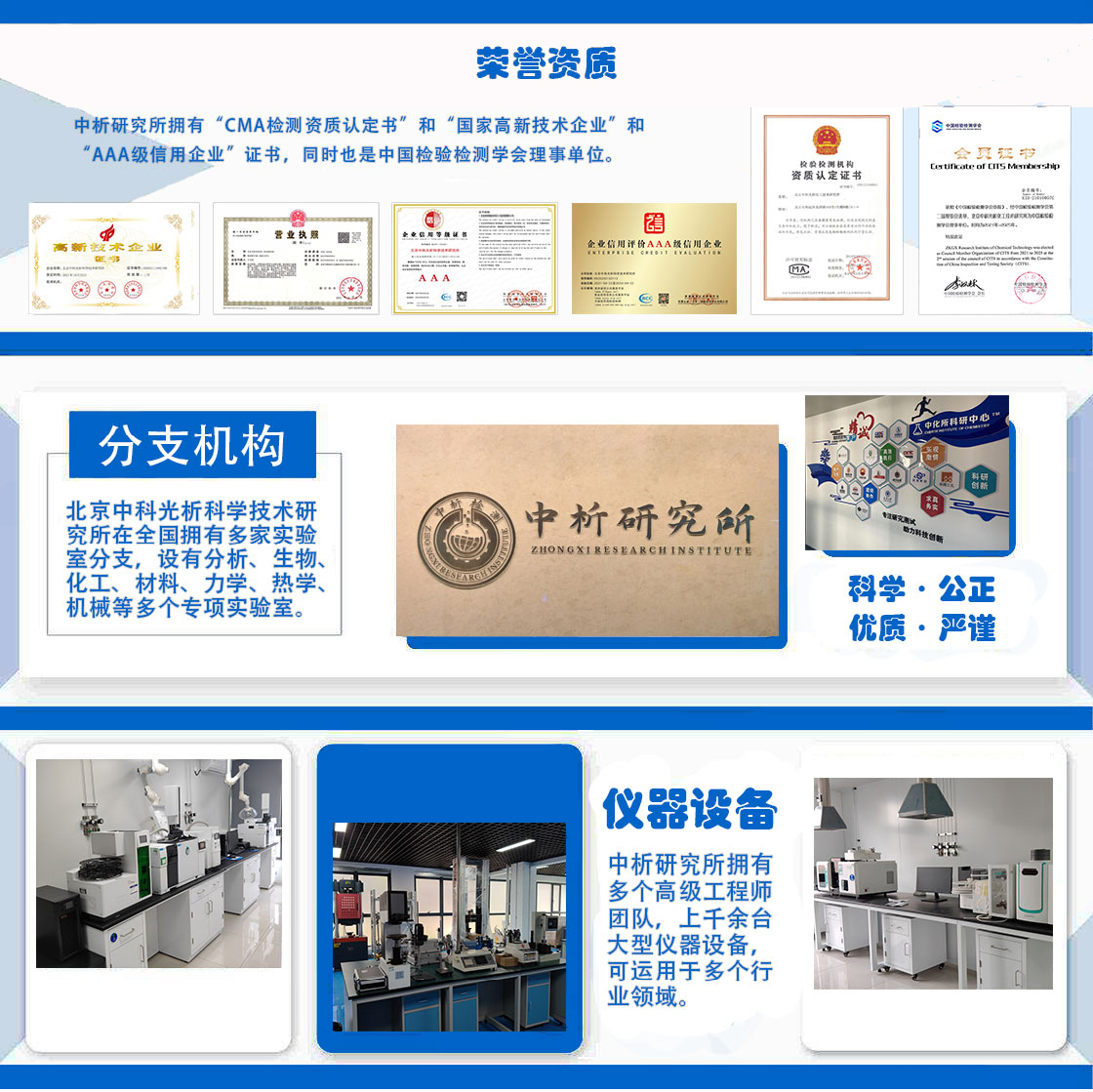
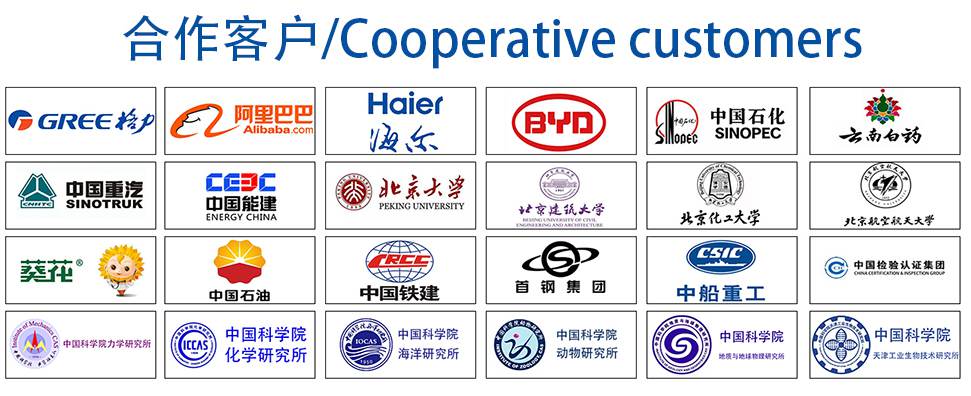