主轴箱固定型自动车床作为精密加工设备的核心机型,广泛应用于轴类、盘类零件的批量生产。其结构特点是主轴箱固定在床身上,通过刀具移动和工件旋转实现复杂加工,具有高刚性、高稳定性的优势。然而,长期运行或频繁换型可能导致精度劣化,因此建立系统化的检测体系是保障加工质量、预防设备故障的关键环节。
一、几何精度检测
1. 主轴系统检测:使用千分表测量主轴径向跳动(≤0.005mm)和轴向窜动(≤0.003mm),通过温度传感器监控运行温升(温升≤15℃)
2. 导轨精度验证:采用激光校准仪检测导轨水平度(误差≤0.02mm/m)与垂直度(误差≤0.015mm/m),确保各轴向运动的几何精度
二、运动精度检测
1. 定位精度测试:使用球杆仪进行圆度测试(ISO 230-4标准),X/Y/Z轴重复定位精度需≤±0.003mm
2. 反向间隙补偿:通过激光干涉仪测量反向间隙值(应≤0.008mm),并调整数控系统补偿参数
三、动力系统检测
1. 主轴性能测试:采用扭矩传感器测量额定转速(如3000rpm)下的扭矩波动(≤±2%),频谱分析仪检测轴承异响
2. 传动机构检测:检查同步带张紧力(符合制造商标准值±5%),齿轮箱油液金属颗粒含量(NAS 10级标准)
四、安全性能验证
1. 防护装置测试:模拟切屑飞溅测试防护罩密封性,安全门联锁响应时间≤0.3秒
2. 急停系统检测:进行多点急停触发试验,全系统停机时间≤0.5秒
五、综合加工能力测试
选用ISO 10791-7标准试件进行实际切削,检测表面粗糙度(Ra≤1.6μm)、直径尺寸一致性(公差±0.01mm),同时监测切削振动值(≤4.5mm/s)
六、环境适应性检测
在模拟工况下连续运行8小时,检测环境温升(≤5℃)、油雾浓度(≤0.5mg/m³),使用声级计测量工作噪音(≤75dB(A))
通过上述系统化检测,可确保主轴箱固定型自动车床保持微米级加工精度,平均故障间隔时间(MTBF)提升40%以上。建议每800小时或完成10批次生产后执行全面检测,并建立数字化检测档案实现预测性维护。
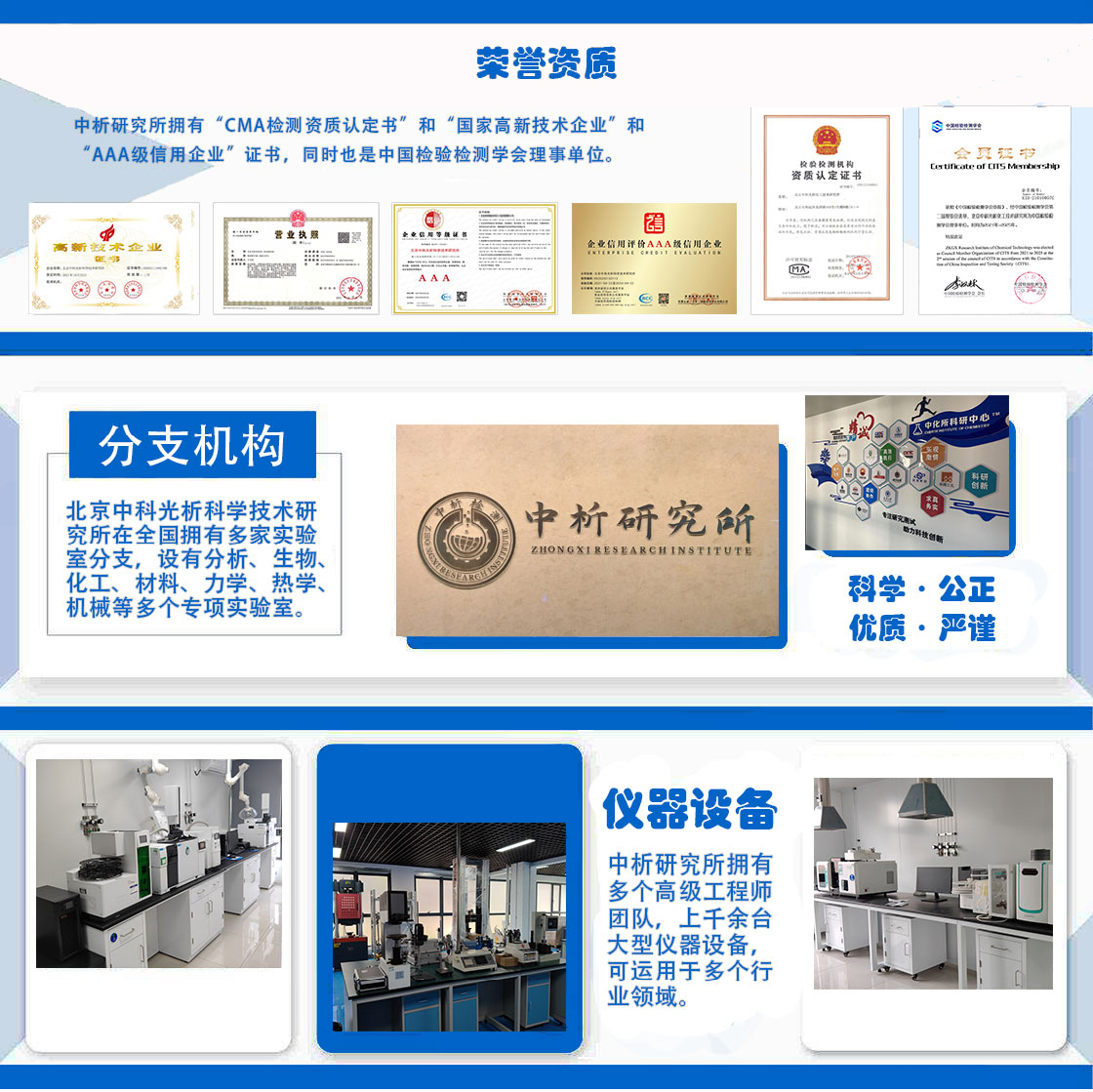
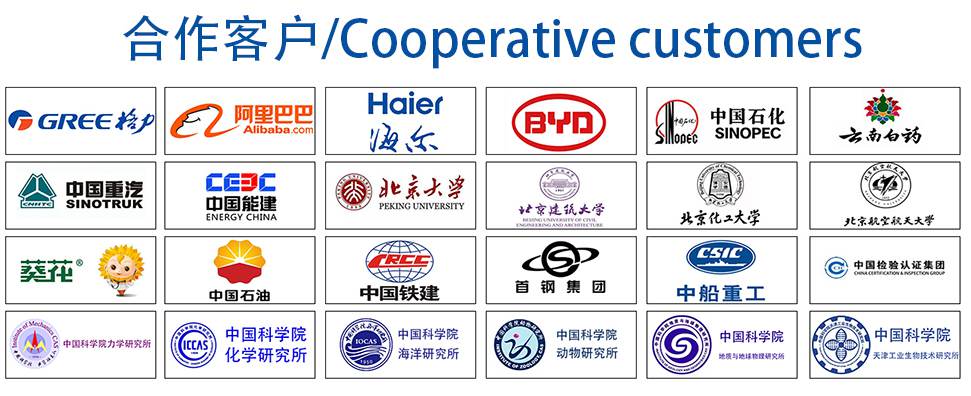