深沟球轴承检测的重要性及流程概述
深沟球轴承作为机械传动系统的核心部件,广泛应用于电机、汽车、机床等领域,其性能直接影响设备的运行效率和使用寿命。据统计,70%的轴承失效案例源于生产或使用阶段的检测疏漏。规范的检测流程能够有效识别轴承的几何精度、材料缺陷和装配质量,避免因轴承故障造成的设备停机甚至安全事故。现代检测技术已形成包含12类关键项目的体系,涵盖从原材料到成品的全生命周期管控。
核心检测项目解析
1. 外观与表面质量检测
采用10倍放大镜和电子显微镜对沟道、滚道、保持架进行目视检查。重点关注划痕(允许≤0.005mm)、锈蚀(面积<1%)及热处理变色现象。新型荧光渗透检测可发现微米级表面裂纹,符合ISO 15243标准要求。
2. 几何尺寸精度检测
使用精密测微仪和轮廓仪测量关键尺寸:
- 内径公差:±0.0025mm(P0级)
- 外径圆度误差:≤0.003mm
- 宽度变动量:±0.005mm
采用三点接触法验证沟道曲率半径偏差,要求控制在理论值的±2%范围内。
3. 旋转精度测试
在恒温(20±1℃)条件下,使用ABEC-7级检测仪测量:
- 径向跳动:P5级≤0.008mm
- 轴向跳动:P6级≤0.015mm
测试时需保持2000r/min转速持续30分钟,振动加速度值应小于4.5dB。
4. 材料性能检测
通过洛氏硬度计(HRC58-62)和能谱分析仪验证:
- 渗碳层深度:1.5-2.0mm
- 基体材料含碳量:0.95-1.10%
- 残余奥氏体含量:<15%
盐雾试验需达到720小时无红锈的防腐要求。
5. 动态性能试验
在专用寿命试验机上模拟工况:
- 额定载荷下持续运行2000小时
- 温升不超过35℃
- 噪声值≤45dB(A)
通过振动频谱分析识别保持架共振频率,确保避开常用转速区间。
检测标准与设备配置
依据GB/T 307.1-2017和ISO 492标准,建议配置:
- 泰勒霍普森圆度仪(分辨率0.01μm)
- 三坐标测量机(空间精度1.5+L/300μm)
- 轴承振动测试系统(频响范围50Hz-10kHz)
检测数据应通过SPC系统实时分析,CPK值需≥1.33方可通过质量认证。
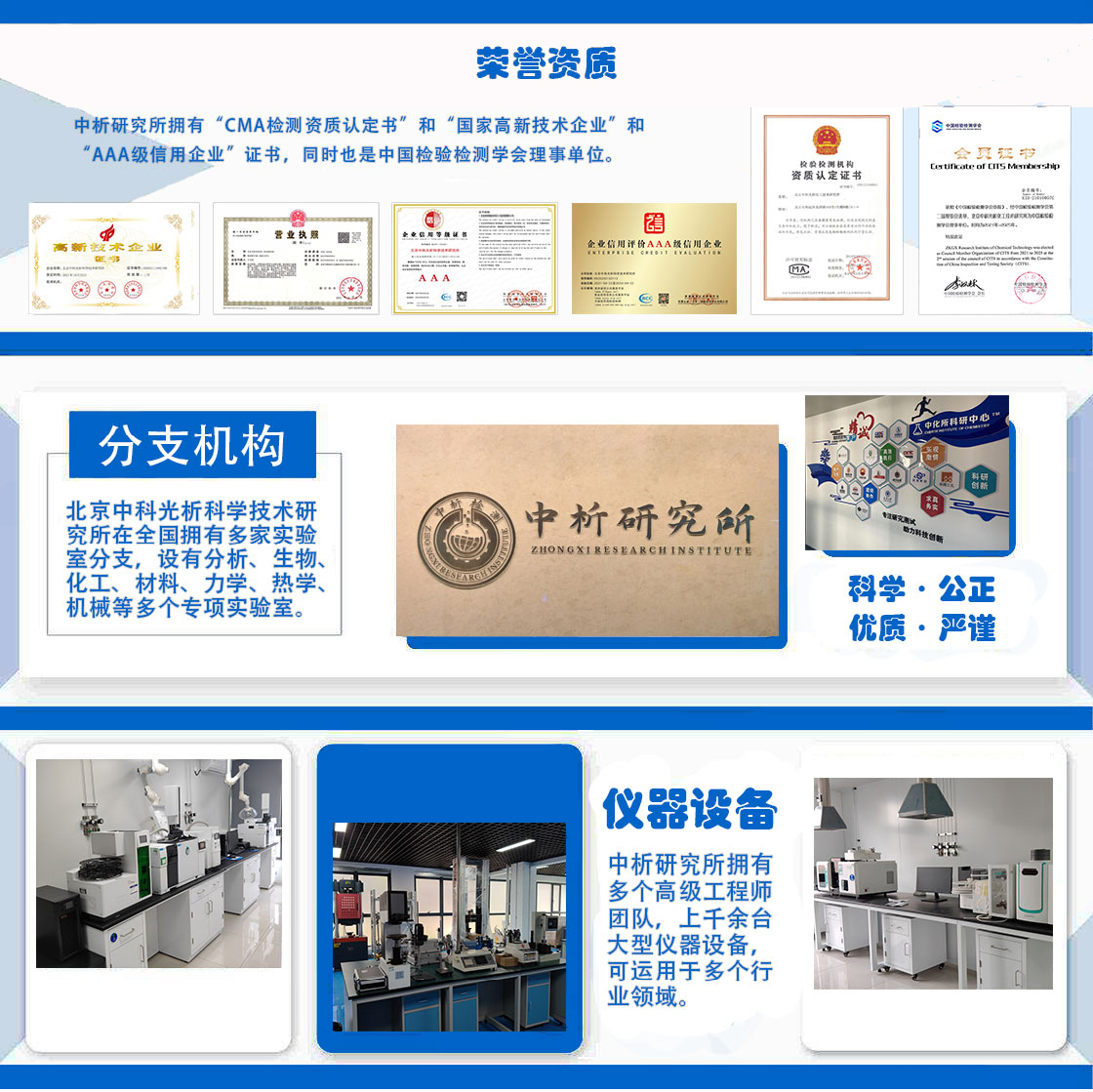
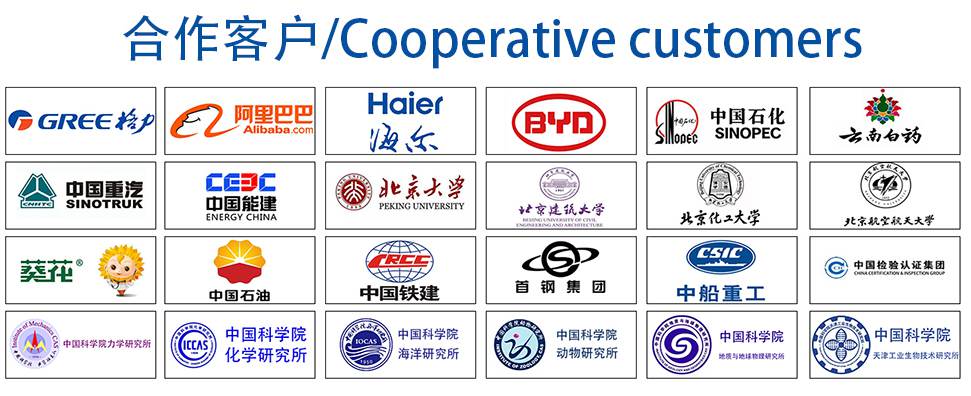