回转工作台检测的关键项目与技术要求
回转工作台作为数控机床、加工中心的核心功能部件,其精度与稳定性直接影响工件的加工质量和生产效率。为确保其性能符合设计要求,需通过系统化的检测流程对关键项目进行评估。检测内容涵盖几何精度、动态性能、重复定位精度等多个维度,同时需结合国际标准(如ISO 10791)或行业规范进行综合分析。
一、几何精度检测
几何精度是回转工作台的基础性能指标,主要包括以下检测项目:
1. 工作台平面度:使用精密水平仪或激光干涉仪测量台面在任意方向上的平面偏差,通常要求误差≤0.01mm/m;
2. 主轴轴线与台面垂直度:通过标准芯棒和千分表检测垂直方向偏差,确保多轴加工时的空间精度;
3. 中心孔同轴度:验证回转中心与定位基准的一致性,避免偏心导致的加工误差。
二、回转精度检测
动态旋转精度直接影响曲面加工质量,需重点关注:
1. 径向跳动:采用接触式测头在360°范围内测量最大偏移量;
2. 轴向窜动:检测工作台在旋转时沿轴线方向的位移量;
3. 分度精度:验证角度定位的准确性,高精度工作台要求≤±5角秒。
三、刚性检测
通过加载试验评估系统抗变形能力:
1. 在最大承载范围内施加静载荷,测量台面下沉量;
2. 模拟切削力进行动态加载,分析振动幅值和频率响应特性。
四、重复定位精度检测
使用激光干涉仪进行多循环测试:
1. 设定标准角度位置进行10次以上重复定位;
2. 记录每次实际角度与理论值的偏差,计算3σ标准偏差值。
五、动态性能检测
评估高速运转时的综合表现:
1. 最大转速下的温升测试,轴承部位温升应≤35℃;
2. 加速度特性曲线分析,验证加减速过程的平稳性;
3. 振动与噪音检测,A计权声压级应≤75dB。
六、辅助系统功能检测
1. 液压/气压夹紧装置的响应时间与保持力测试;
2. 润滑系统供油量与油膜均匀性检查;
3. 光栅/编码器反馈信号的稳定性验证。
通过以上系统化检测,可全面评估回转工作台的性能状态。建议每500工作小时或重要加工任务前进行周期性检测,结合设备维护记录建立精度衰减模型,为预防性维护提供数据支持。检测数据异常时,应及时进行轴承预紧力调整、导轨修复或伺服参数优化,确保加工系统处于最佳工作状态。
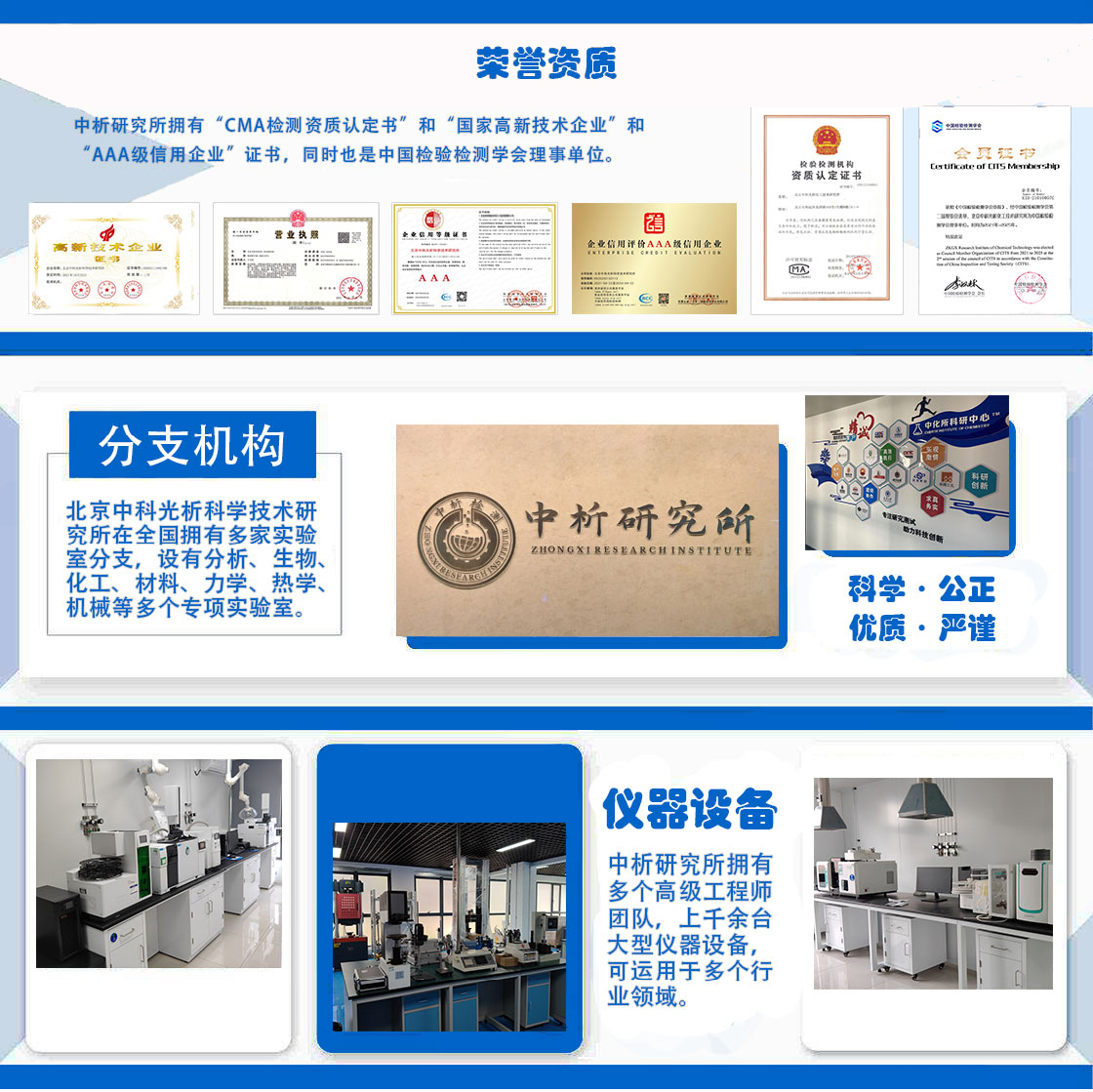
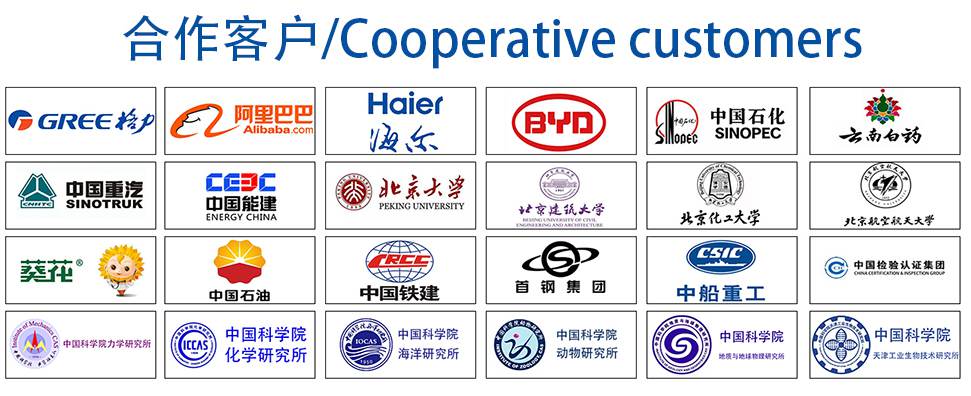