组合机床液压滑台检测的重要性与核心项目
组合机床液压滑台作为机床的核心运动部件,其性能直接影响加工精度、生产效率及设备稳定性。液压滑台通过液压驱动实现工件或刀具的直线运动,长期运行中易因油液污染、密封件磨损、系统压力异常等问题导致动作迟缓、定位偏差或振动加剧。定期开展液压滑台检测是保障设备高效运行、延长使用寿命的关键措施。检测项目需覆盖液压系统、机械结构、控制元件及综合性能,以全面评估滑台的健康状态,避免因部件失效引发停机事故。
一、液压系统功能性检测
1. 液压压力测试:使用压力表检测系统工作压力是否达到设定值,观察压力波动是否在允许范围内。异常压力可能导致滑台爬行或冲击现象。
2. 泄漏检测:检查油缸、油管接头及阀块的密封性,通过目视或荧光检漏剂排查外泄漏点,同时监测油温变化判断是否存在内泄漏。
3. 油液性能分析:采集液压油样本,检测粘度、污染度(颗粒计数)及含水量,劣化油液会加速元件磨损并影响系统响应速度。
二、机械结构精度与磨损评估
1. 导轨磨损测量:使用千分表或激光干涉仪检测导轨直线度、平行度及表面磨损量,超差会导致滑台运动轨迹偏移。
2. 滑块间隙检测:通过塞尺测量滑块与导轨接触面间隙,过大的间隙会引发振动和精度损失。
3. 连接件刚性检查:检查滑台与床身、驱动机构的连接螺栓预紧力,确保机械传动的稳定性。
三、控制系统与传感器校验
1. 位置传感器标定:使用光栅尺或磁栅尺校验滑台实际位移与反馈信号的匹配度,消除定位误差。
2. 电磁阀响应测试:通过示波器监测电磁阀切换时间,滞后超过10%需更换阀体。
3. PLC程序逻辑验证:模拟不同工况下的控制指令,确保滑台启停、调速及互锁功能正常。
四、综合性能验收标准
完成单项检测后需进行空载与负载试验:
- 空载运行:滑台全程移动速度波动≤±5%,无异常噪音或抖动。
- 负载测试:在额定载荷下重复定位精度应≤0.02mm,连续运行2小时油温升幅不超过35℃。
通过系统性检测可精准定位故障源,为液压滑台的维修或改造提供数据支撑,有效降低非计划停机风险。
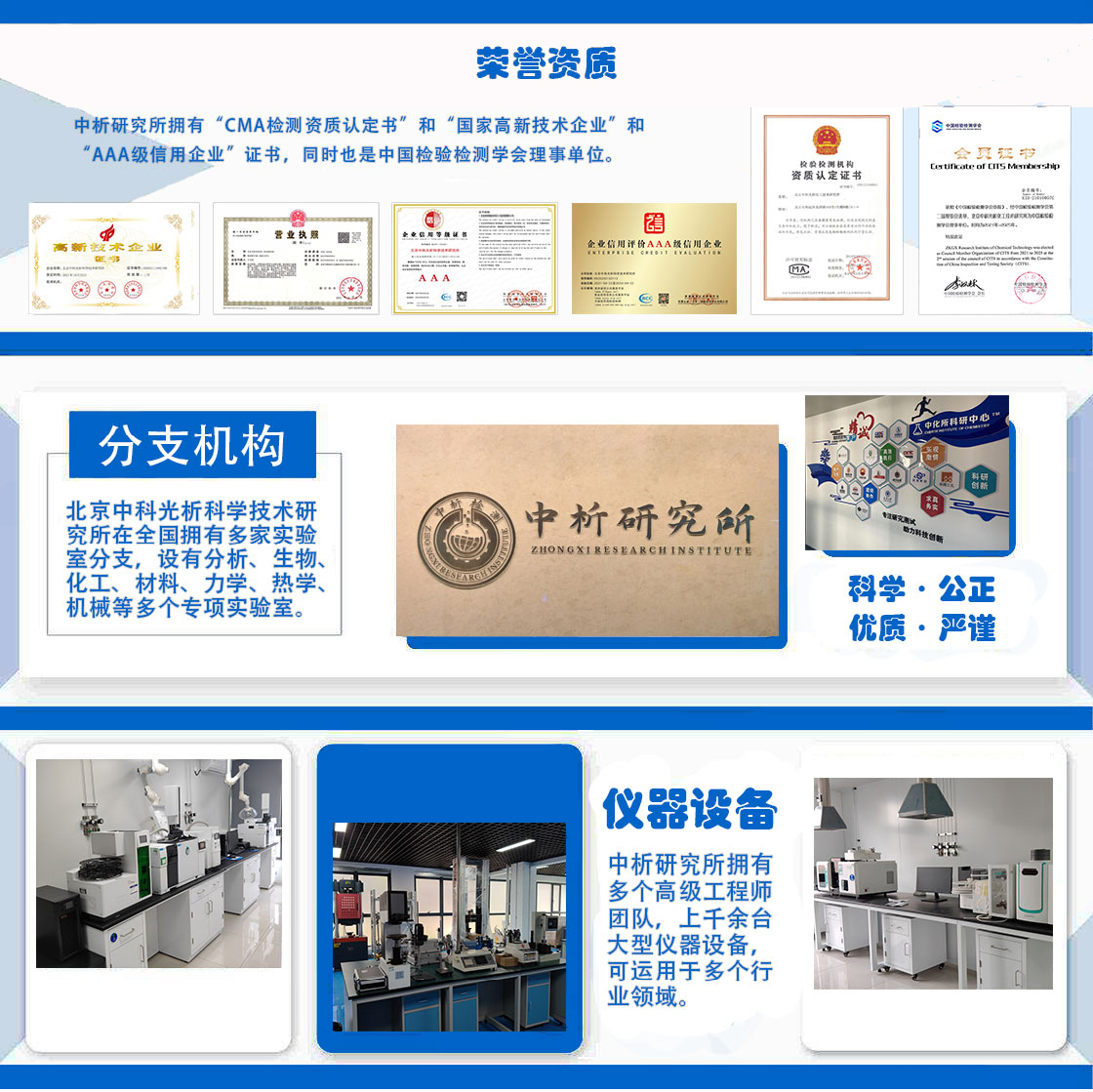
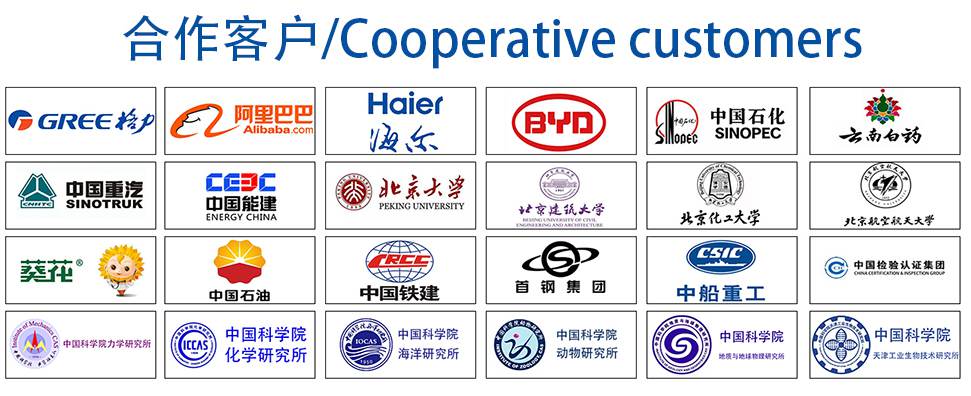