型材弯曲机检测项目及技术要点解析
型材弯曲机作为金属加工行业的重要设备,其性能直接关系到型材成型质量和生产效率。定期开展专业检测可有效预防设备故障、延长使用寿命,同时确保加工精度符合GB/T 232-2010《金属材料弯曲试验方法》等国家标准要求。检测工作需涵盖机械性能、电气系统、安全装置等8大核心模块,通过多维度评估实现设备状态的精准把控。
一、主要检测项目清单
1. 机械传动系统检测:检查齿轮箱油位及油质(按ISO 4406标准评估污染等级),测量传动轴径向跳动量(公差≤0.02mm/m),评估皮带/链条张紧度(挠度控制在10-15mm范围)。
2. 液压系统效能测试:检测油缸活塞行程精度(误差需<0.1mm),系统压力稳定性(波动值不超过设定值的±2%),油温控制功能(工作温度应维持在40-60℃区间)。
3. 电气控制系统验证:使用示波器检测PLC输出信号稳定性,测试各限位开关响应时间(≤0.3秒),测量电机绝缘电阻(≥5MΩ),验证急停装置触发时效(全系统断电时间<1秒)。
4. 成型精度校准:采用激光跟踪仪测量弯曲角度误差(±0.5°以内),使用CMM三坐标检测回弹量(铝合金材料应<1.2°,碳钢<0.8°),验证模具装配同轴度(偏差≤0.05mm)。
二、特殊工况专项检测
针对高强度作业场景需增加:连续运行8小时温升测试(电机温升≤65K),过载保护装置试验(110%额定负载下应可靠动作),以及不同材质(如钛合金/不锈钢)的成型力衰减测试。
三、检测周期与记录规范
建议执行三级检测制度:每日进行设备点检(包含润滑状态、异常声响等基础项),每月实施精度校准,每年开展系统性检测。所有数据应按照ISO 9001质量管理体系要求建档,关键参数需绘制趋势分析图实现预防性维护。
通过科学系统的检测方案,可使型材弯曲机保持最佳工作状态,将设备故障率降低60%以上,同时提升产品合格率3-5个百分点。特别要注意的是,当设备进行过重大维修或长期停用后,必须执行全项目检测方可重新投入生产使用。
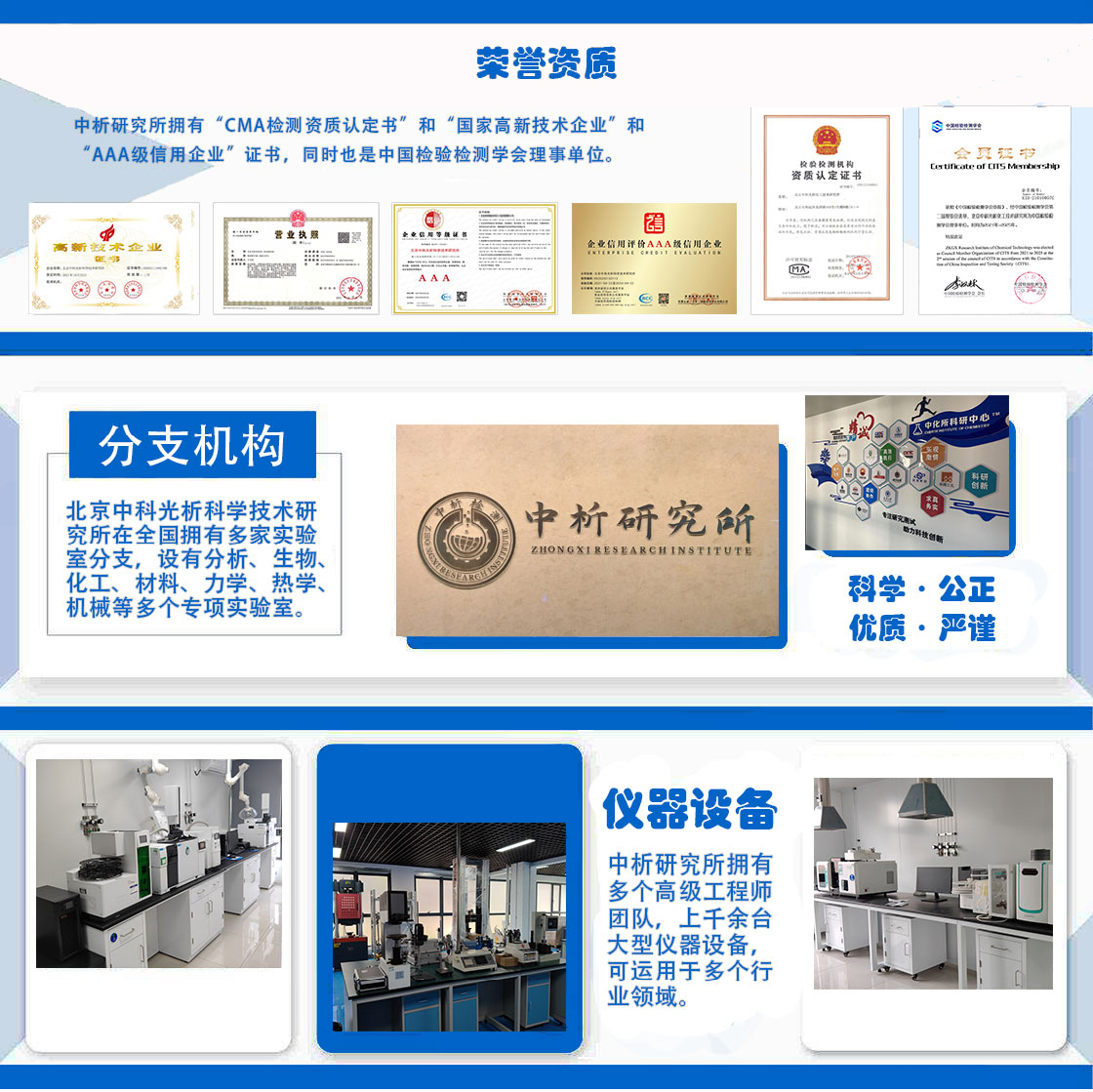
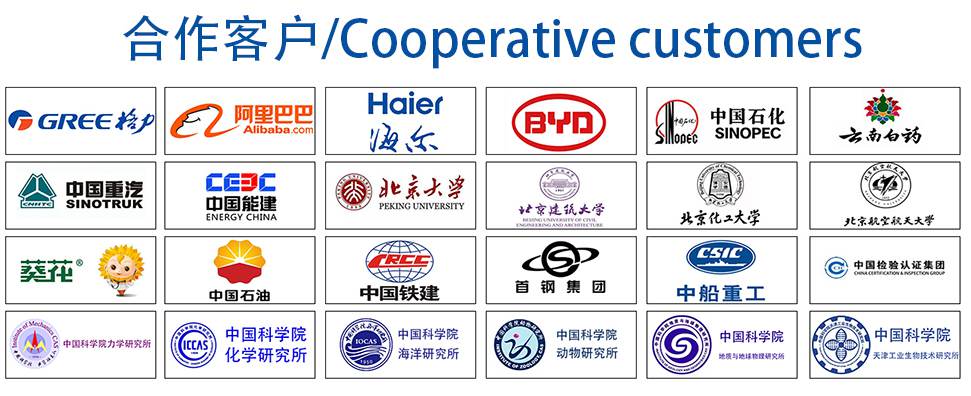