组合机床回转工作台作为现代机械加工中的核心部件,广泛应用于汽车、航空航天、模具制造等领域。其功能是实现工件在加工过程中的多角度定位与分度,确保复杂零件的高精度、高效率加工。随着加工精度的要求日益提高,回转工作台的性能稳定性直接影响整机的加工质量。因此,定期对回转工作台进行系统性检测,不仅是设备维护的必备环节,更是保障生产效率和产品质量的关键措施。
一、几何精度检测
几何精度是回转工作台的基础性能指标,主要包括台面的平面度、垂直度及与主轴的同心度。检测时需使用高精度水平仪、千分表和激光干涉仪等工具。例如,平面度检测需沿台面多个方向布置测点,通过数据对比分析偏差是否在允许范围内(通常≤0.01mm/m)。若发现超差,需对台面进行研磨或调整支撑机构。
二、回转定位精度检测
定位精度直接影响加工位置的一致性。检测方法为:利用角度编码器或光学分度头,在不同角度(如0°、90°、180°、270°)进行多次重复定位,记录实际值与理论值的误差。根据ISO 230-2标准,精密级回转台的定位误差应≤±5角秒。超差可能由蜗轮蜗杆磨损或伺服系统故障引起。
三、刚性及负载能力测试
在额定负载下,回转台的变形量需通过应变仪或位移传感器测量。测试时需模拟实际加工条件,逐步加载至最大工作载荷(通常为台面自重的1.5倍),观测台面下沉量和偏转角。刚性不足会导致切削振动,影响表面粗糙度,需检查轴承预紧力或加强支撑结构。
四、润滑与温升监测
回转台长时间运转时,需监测润滑系统油压、油量及温度变化。使用红外热像仪检测轴承、齿轮部位的温升,连续运行2小时后温升应≤35℃。异常温升可能反映润滑不足或摩擦副磨损,需及时更换润滑油或调整密封间隙。
五、重复定位精度验证
通过激光干涉仪进行动态重复性测试,连续执行10次相同角度的定位动作,计算标准差。高端机床要求重复定位精度≤±2角秒。若数据离散较大,需排查伺服电机反馈系统或消除反向间隙。
六、传动系统检测
重点检查蜗轮蜗杆副的啮合间隙与磨损情况。使用塞尺测量蜗杆轴向游隙(标准值0.02-0.04mm),同时听诊齿轮箱异响。严重磨损需更换配件并重新调整背隙补偿参数。
七、安全防护功能测试
验证超载保护、紧急制动及防护罩联锁功能。通过模拟过载状态(110%额定负载)触发保护机制,记录响应时间(应≤0.5秒)。防护罩开启时系统应自动切断动力,避免机械伤害。
检测注意事项:需在恒温环境(20±1℃)下进行,检测前空载运行30分钟以消除热变形影响;所有仪器需定期校准并符合GB/T 17421.2-2016标准;检测数据应形成趋势分析报告,为预防性维护提供依据。
结论:通过系统化的检测项目,可全面掌握组合机床回转工作台的性能状态,延长设备寿命并避免因精度失效导致的产品报废。建议结合智能传感器技术实现实时监控,将事后维修升级为预测性维护,进一步提升生产效益。
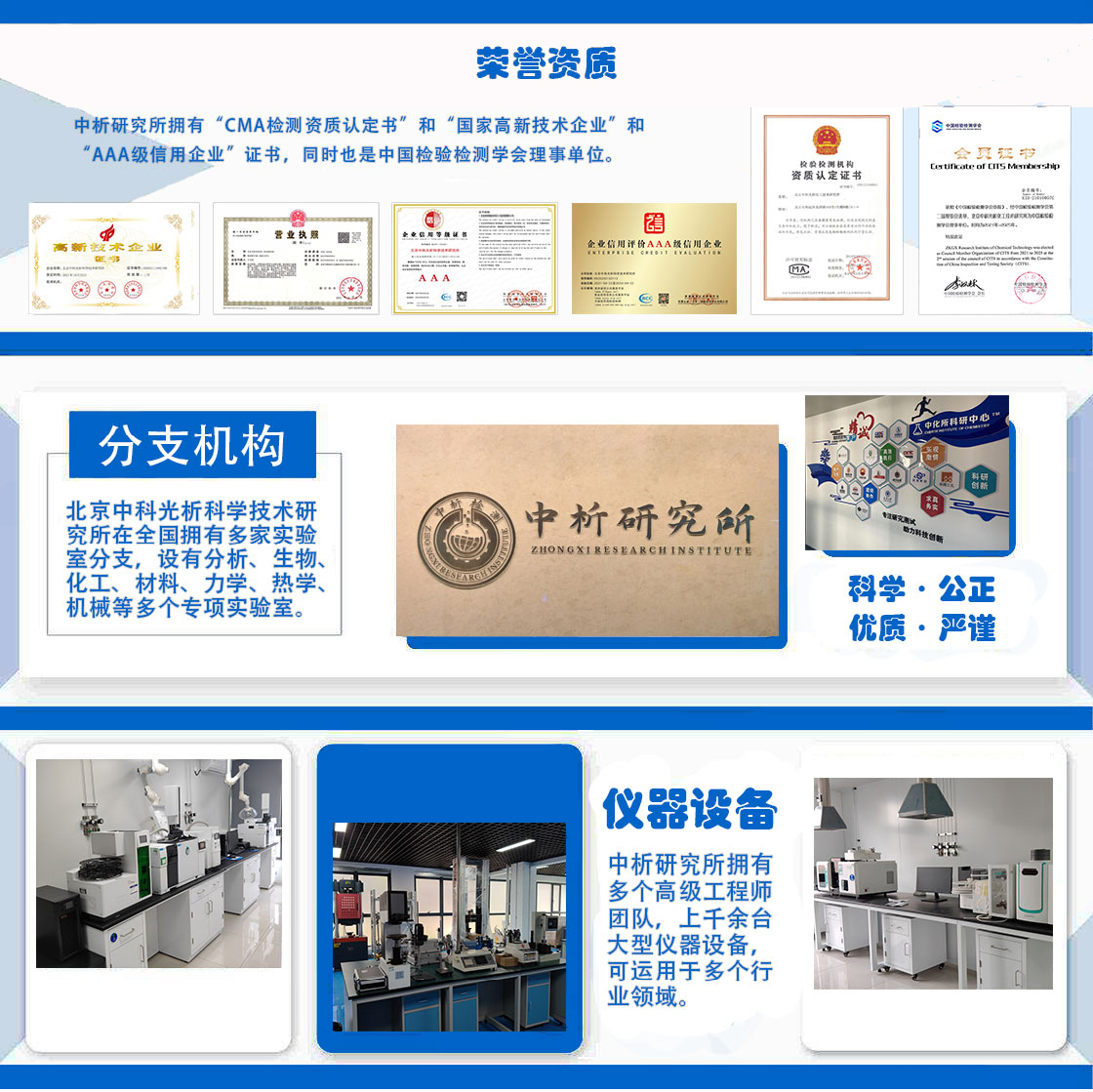
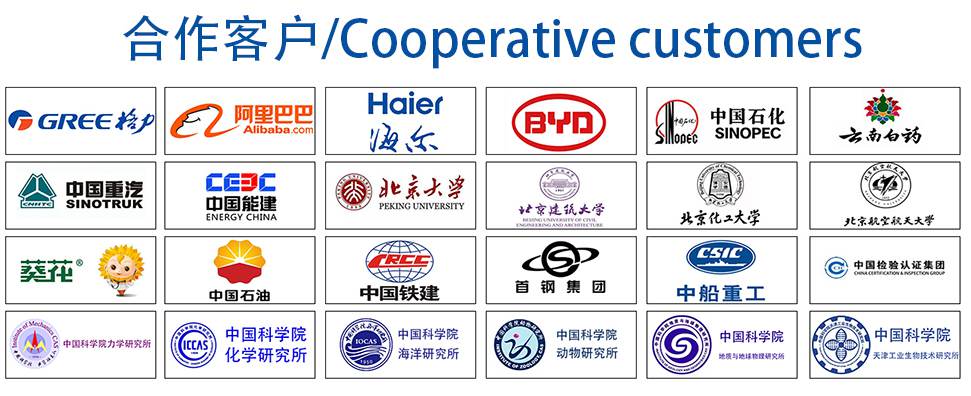