滚动轴承零件参数检测的重要性
滚动轴承作为机械设备的核心传动部件,其性能直接影响设备运行的稳定性、承载能力和使用寿命。为确保轴承满足设计要求,需对关键参数进行系统性检测。现代工业中,滚动轴承零件的检测项目覆盖尺寸精度、形位公差、材料性能及表面质量等四大维度,依据ISO、GB/T等标准建立严格的检测流程。通过科学的参数检测,不仅能验证制造工艺的可靠性,还能预防因零件缺陷导致的设备失效风险,对提升机械装备整体质量具有决定性作用。
核心检测项目分类
滚动轴承零件检测体系可细分为以下关键类别:
1. 尺寸精度检测
• 内圈/外圈内径、外径及宽度测量
• 滚动体直径偏差与椭圆度检测
• 保持架兜孔尺寸及中心距检验
采用高精度三坐标测量仪、气动量仪等设备,确保公差符合DIN 620-2标准要求,其中精密级轴承尺寸偏差需控制在微米级。
2. 形位公差检测
• 内外圈径向/轴向跳动量检测
• 滚道圆度、圆柱度测量
• 端面平行度与垂直度校验
通过圆度仪、激光干涉仪等设备分析零件几何形态,如P4级轴承径向跳动需≤3μm,超差会导致异常振动和噪音。
3. 材料性能检测
• 表面硬度(HRC)与硬化层深度测试
• 金相组织分析(碳化物分布、晶粒度)
• 冲击韧性及抗压强度试验
采用洛氏硬度计、显微硬度计及金相显微镜等设备,确保GCr15等轴承钢符合ASTM A295标准,保障材料承载能力和耐磨性。
4. 表面质量检测
• 粗糙度Ra值测量(接触式轮廓仪)
• 表面缺陷探伤(磁粉检测/涡流检测)
• 防锈处理层厚度及附着力测试
精密轴承表面粗糙度通常要求Ra≤0.05μm,同时通过荧光渗透检测发现微裂纹等隐蔽缺陷。
5. 动态性能检测(型式试验)
• 额定寿命试验(加速疲劳测试)
• 振动加速度级(Z组/V组分级测试)
• 温升及润滑性能评估
依据ISO 281标准进行寿命试验,采用振动频谱分析仪监测异常频率,评估轴承在模拟工况下的实际表现。
检测技术发展趋势
随着智能制造发展,在线检测系统与AI图像识别技术逐渐应用于轴承检测领域。机器视觉系统可实现0.1μm级表面缺陷自动识别,而基于大数据分析的预测性检测正改变传统抽检模式。未来检测技术将更注重全流程数据追溯与智能决策,推动轴承制造向零缺陷目标迈进。
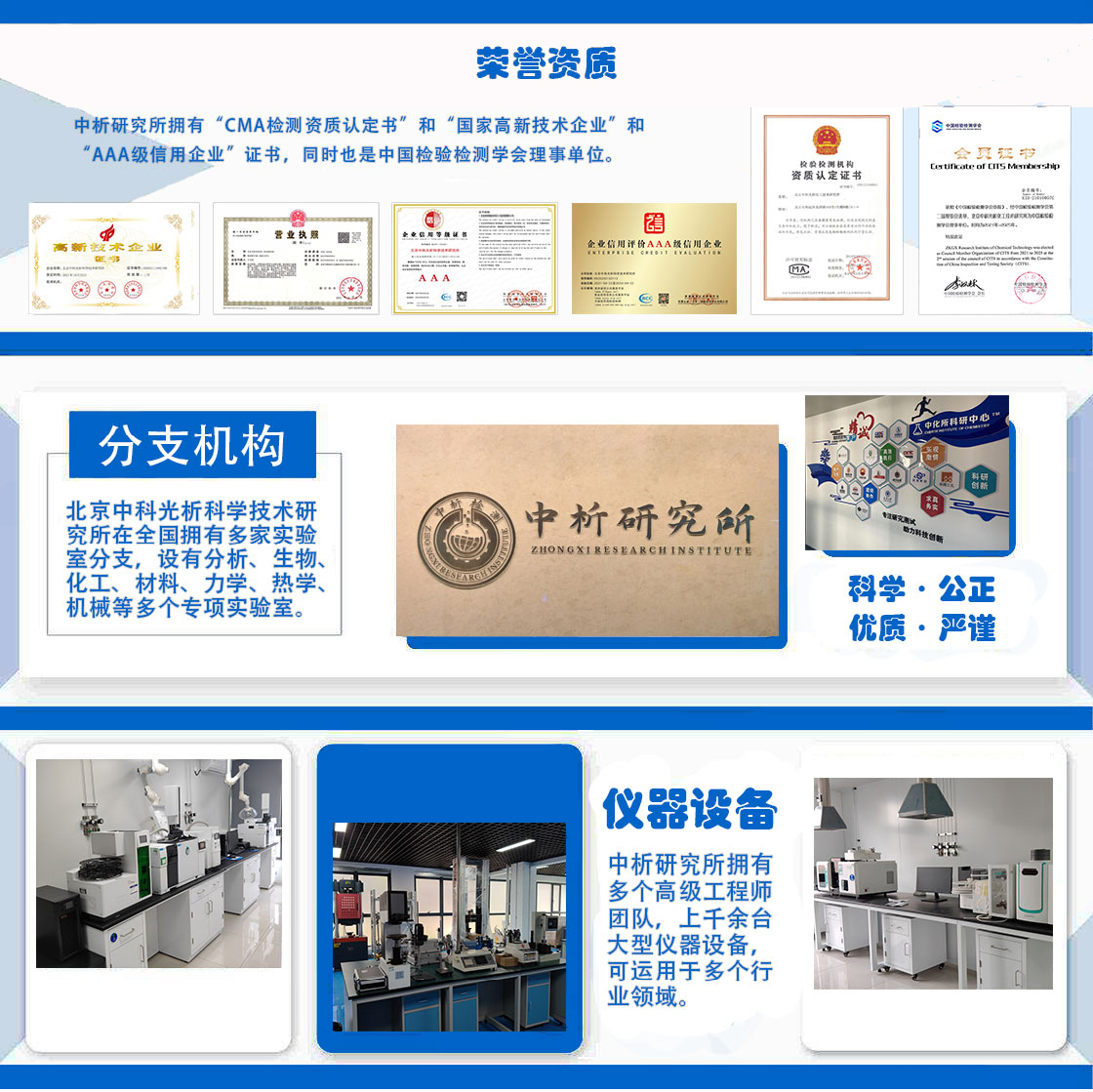
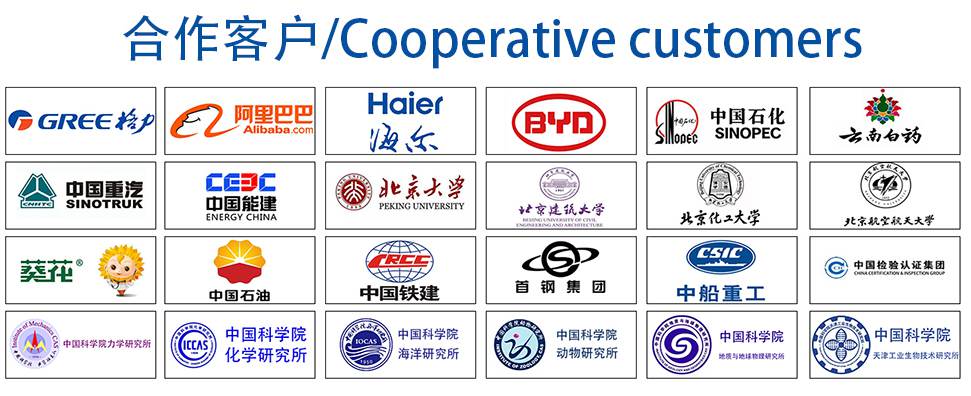