滚动轴承碳氮共渗低碳钢检测的重要性
在机械制造领域,滚动轴承作为核心传动部件,其材料性能直接影响设备的使用寿命和可靠性。碳氮共渗低碳钢凭借其优异的表面硬度、耐磨性和芯部韧性,成为高端轴承制造的理想材料。然而,碳氮共渗工艺的复杂性要求对材料的物理、化学及力学性能进行系统性检测,以确保材料满足工况需求。检测项目需覆盖从原材料成分到处理工艺效果的全流程,通过科学手段验证材料的均质性、渗层深度、残余应力分布等关键指标,从而避免因材料缺陷导致的轴承失效风险。
核心检测项目及方法
1. 化学成分分析
通过光谱分析仪(如ICP-OES)对低碳钢的C、Mn、Cr、Mo等元素含量进行定量检测,确保基体材料符合GB/T 3077标准。重点关注Si、Al等可能影响渗层形成的元素浓度,偏差超过±0.05%需启动工艺调整程序。
2. 金相组织检测
使用金相显微镜和扫描电镜(SEM)观察渗层与芯部的微观结构: - 表层需呈现连续致密的碳氮化合物层(厚度5-20μm) - 过渡区应为细针状马氏体组织 - 芯部保留铁素体+珠光体结构 异常粗大晶粒或非马氏体组织的出现可能预示淬火冷却速率不足。
3. 表面硬度与渗层深度测定
采用维氏硬度计(HV0.3)从表面至芯部逐点测试,绘制硬度梯度曲线: - 表面硬度需达到700-850HV - 有效硬化层深度(根据ISO 2639标准)应控制在0.3-0.8mm 使用显微硬度法或热酸侵蚀法验证渗层深度的均匀性,同一截面区域偏差不得超过±10%。
4. 残余应力检测
通过X射线衍射法(XRD)测量表面残余压应力值,合格范围应介于-400至-600MPa。过高的压应力可能引发微裂纹,而压应力不足则会影响接触疲劳强度。同步检测应力梯度分布,确保应力过渡平缓。
5. 耐腐蚀性测试
执行中性盐雾试验(ASTM B117),48小时后观察表面锈蚀面积比例。合格标准为锈蚀区域≤2%,且无点蚀现象。对于特殊工况要求的轴承,可增加电化学阻抗谱(EIS)测试以量化耐蚀性能。
6. 动态性能验证
在模拟工况的轴承试验台上进行: - 额定载荷下的疲劳寿命测试(循环次数≥1×10⁷次) - 极限转速下的温升监测(ΔT≤45℃) - 振动加速度值分析(符合ISO 15242-2标准) 通过动态数据验证碳氮共渗处理对轴承综合性能的提升效果。
质量控制的关键环节
建立从原材料入库到成品出厂的四级检测体系: 1)原料光谱复验 2)热处理过程在线监测(炉温均匀性、碳势控制) 3)半成品无损检测(超声波探伤+磁粉检测) 4)成品全尺寸测量(圆度误差≤1.5μm) 通过SPC统计过程控制技术,对关键参数进行趋势分析,实现质量问题的早期预警。
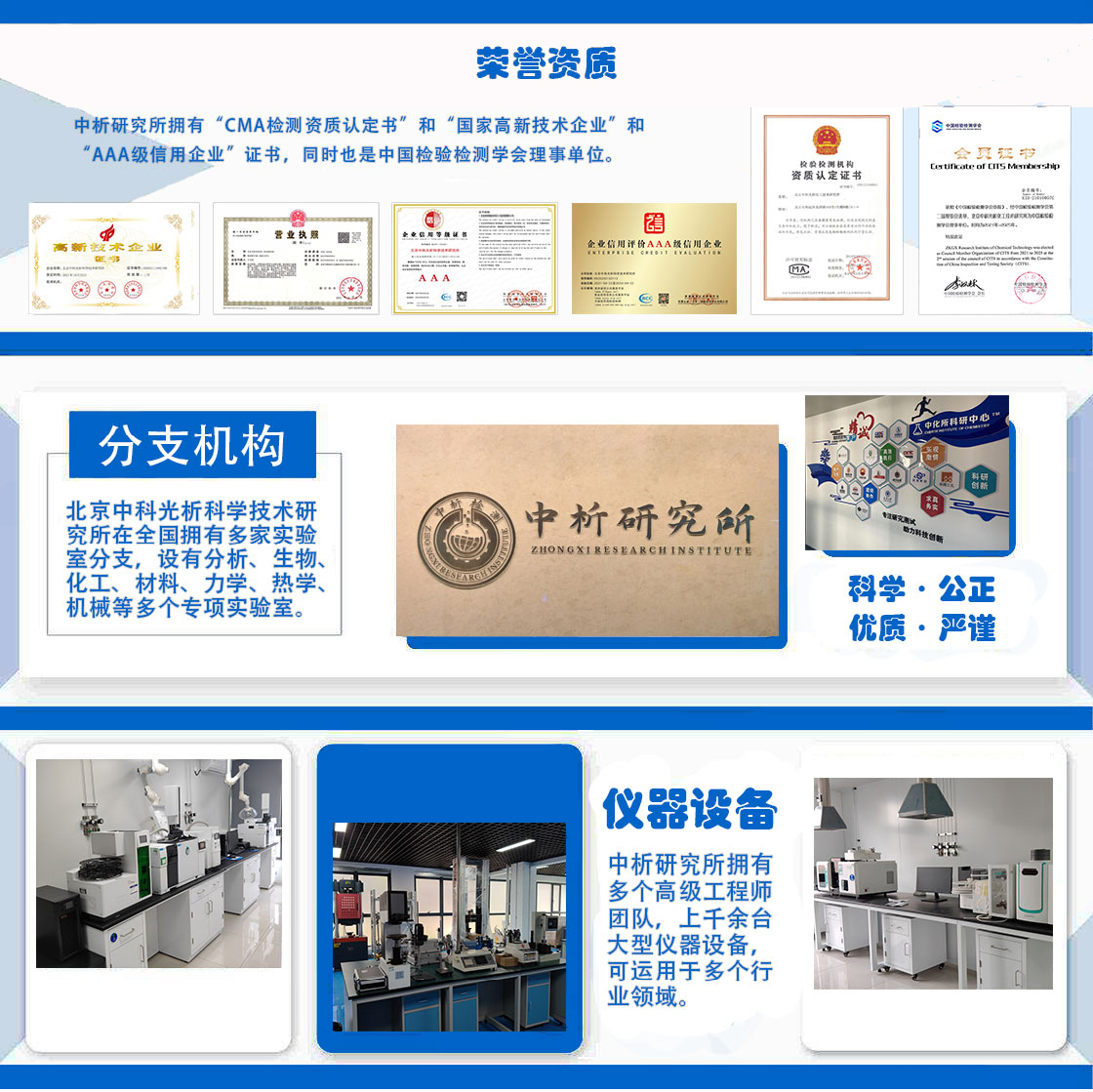
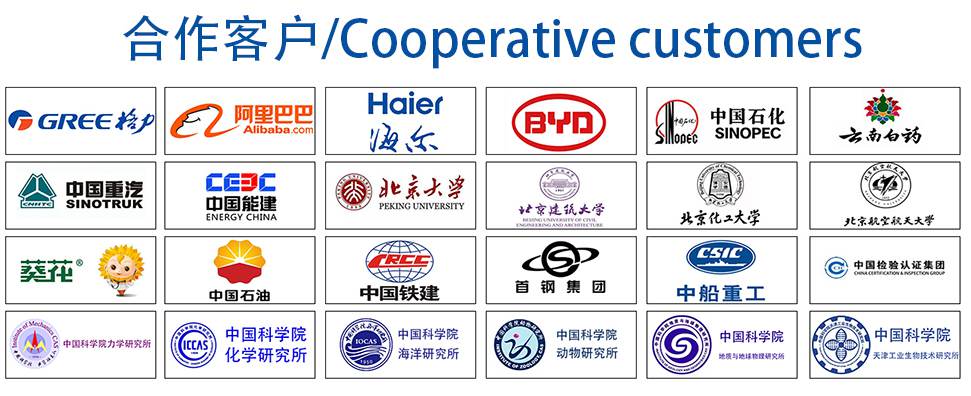