卧式精镗床镗头检测的关键项目与技术要点
卧式精镗床作为高精度孔加工的核心设备,其镗头的性能直接决定了工件的加工质量与生产效率。镗头在长期运行中可能因磨损、振动或热变形等因素导致精度下降,进而引发加工孔径偏差、表面粗糙度超标等问题。因此,系统性、周期性的镗头检测是保障设备性能与工艺稳定性的必要措施。检测过程需覆盖机械结构、运动精度、电气控制及环境适应性的多维度参数,并结合标准规范制定科学的评估方案。
主轴系统径向跳动检测
使用千分表或激光干涉仪测量镗头主轴在高速旋转下的径向跳动量,要求符合ISO 230-3标准(通常≤0.005mm)。检测时需分别在轴向不同位置及多转速工况下记录数据,分析轴承磨损与装配误差对精度的影响。
轴向窜动与定位精度测试
通过光栅尺或球杆仪对镗头的轴向移动重复性进行检测,重点关注反向间隙补偿效果。典型要求为全行程定位误差≤±0.008mm,重复定位精度≤0.005mm。对于数控机型还需验证伺服系统的跟随误差参数。
镗杆同轴度与静动态刚性评估
采用三点接触法或激光准直仪检测镗杆与主轴的中心线偏差,偏差值应控制在0.01mm/m以内。同时通过加载模拟切削力测试系统刚性,观察振动幅频特性曲线是否符合加工工况需求。
温度敏感性与热变形监测
在连续运行4小时后,使用红外热像仪记录主轴箱温升情况,对比冷态与热态下的加工尺寸差异。精密级设备要求温升引起的热变形量≤0.015mm,必要时需优化冷却系统或增加温控补偿功能。
刀具夹持系统性能验证
使用拉压力计检测液压或机械夹紧机构的夹持力稳定性,确保在最高转速下刀具无松动风险。同时检查刀柄锥面接触面积(应≥85%)及换刀重复定位精度(≤0.002mm)。
润滑与密封系统状态诊断
通过油液颗粒度分析仪检测主轴轴承润滑油的污染等级(NAS 1638标准),同步检查导轨密封件的磨损状况。异常油膜厚度或污染物含量超标可能引发早期磨损失效。
振动与噪声频谱分析
采用加速度传感器与声级计采集镗头运行时的振动速度有效值(要求≤2.8mm/s)及噪声水平(≤75dB(A))。通过FFT频谱分析识别不平衡、不对中或齿轮啮合异常等故障特征频率。
几何精度综合校验
依据GB/T 13573标准,使用精密水平仪、方尺及检棒检测主轴箱移动直线度(≤0.02mm/1000mm)、工作台平面度(≤0.015mm)及主轴与工作台的垂直度(≤0.01mm/300mm)。
加工试件综合性能测试
最终通过切削铸铁或钢质标准试件验证实际加工能力,检测项目包括孔径尺寸公差(IT6级)、圆度(≤0.008mm)、圆柱度(≤0.012mm)及表面粗糙度(Ra≤1.6μm)。
通过上述系统性检测,可全面评估卧式精镗床镗头的技术状态,及时进行主轴轴承更换、导轨副刮研或数控参数补偿等针对性维护。建议每800小时或季度周期实施预防性检测,并结合加工质量数据动态调整检测频次。
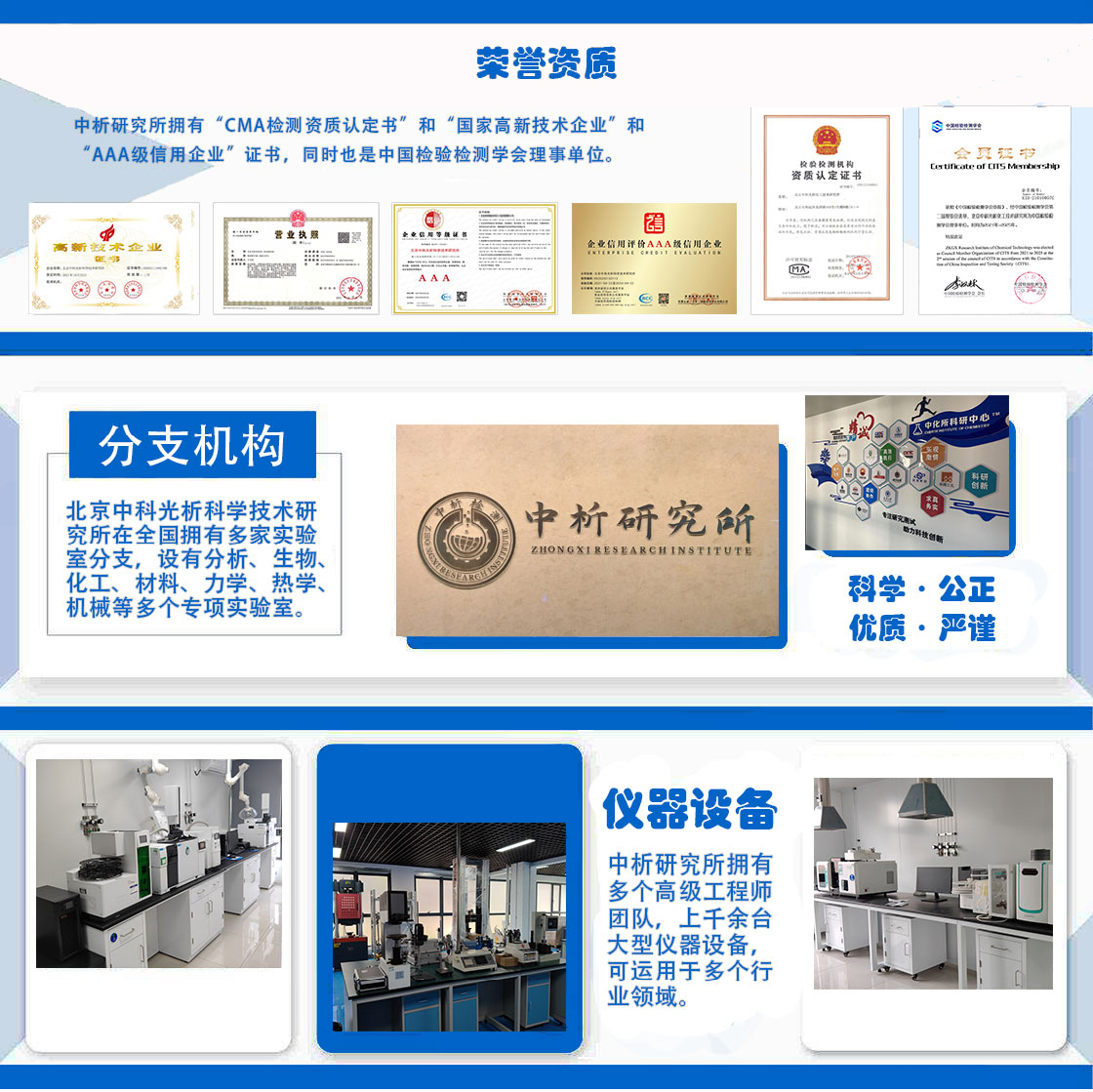
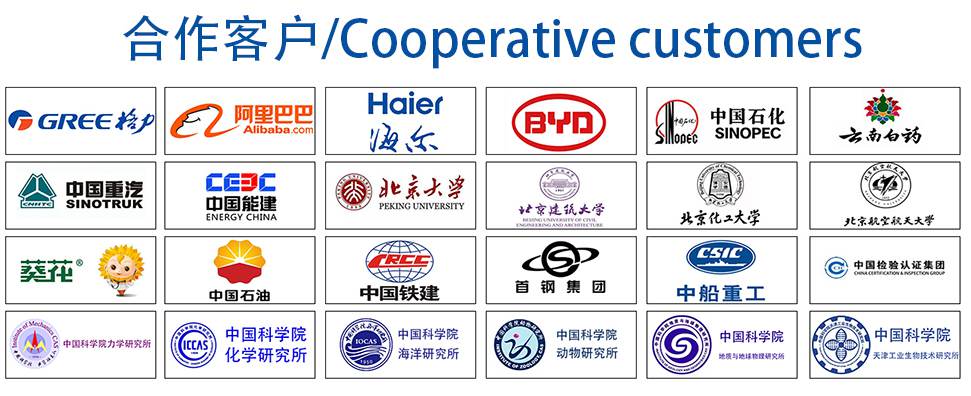