电子单元重复性检测的关键意义
在电子设备生产与质量控制体系中,电子单元的重复性检测是验证产品可靠性的核心环节。作为衡量电子元器件、模组或系统在相同操作条件下输出结果一致性的重要指标,重复性直接关系到设备长期运行的稳定性和安全性。随着工业4.0智能化升级,检测项目已从基础参数测量发展为涵盖电气特性、环境适应、信号完整性等多维度的系统化评估体系。
关键检测项目解析
1. 信号响应一致性测试
通过施加标准输入信号,连续记录电子单元输出波形参数(包括幅度、频率、脉宽等),计算10次重复测量的标准差。要求数字信号抖动误差≤0.5%,模拟信号波动幅度需控制在标称值的±2%以内。
2. 工作参数稳定性验证
在额定供电条件下,持续监测关键运行参数24小时:电压波动需稳定在±1%Vcc范围内,电流漂移不得超过初始值的3%。对于功率器件,需额外考核热态重复性,监测温度循环中的参数变化曲线。
3. 环境适应性重复测试
依据IEC 60068标准,进行温度(-40℃~85℃)、湿度(95%RH)、振动(5Hz-500Hz)三轴循环测试。每个环境条件下至少进行3组重复测试,功能参数偏差须满足初始校准值的±5%。
4. 老化加速重复性实验
采用高温老化箱(125℃)进行100小时加速老化,每隔8小时执行全参数检测。要求关键性能指标(如转换效率、响应速度)的退化斜率不超过0.1%/h,且末次测量值需在首次值的±3%区间内。
5. 数据传输重复性校验
对于带通信功能的电子单元,需通过协议分析仪捕获1000次数据传输过程。统计CRC校验错误率、数据包丢失率等指标,要求误码率≤1×10⁻⁶,响应时间标准差不超过0.5ms。
智能化检测技术发展
当前主流检测系统集成自动化测试平台(ATE),配合机器学习算法实现异常模式识别。某知名汽车电子厂商的案例显示,采用AI辅助重复性检测后,故障预警准确率提升47%,测试周期缩短60%。随着数字孪生技术的应用,虚拟仿真与实物检测的交叉验证将成为新的技术突破点。
结语
电子单元重复性检测已形成涵盖56项具体参数的行业标准体系,企业需要根据产品特性建立动态检测模型。通过强化过程控制、完善数据追溯机制,可有效提升电子设备的质量一致性,为工业自动化系统的可靠运行提供坚实保障。
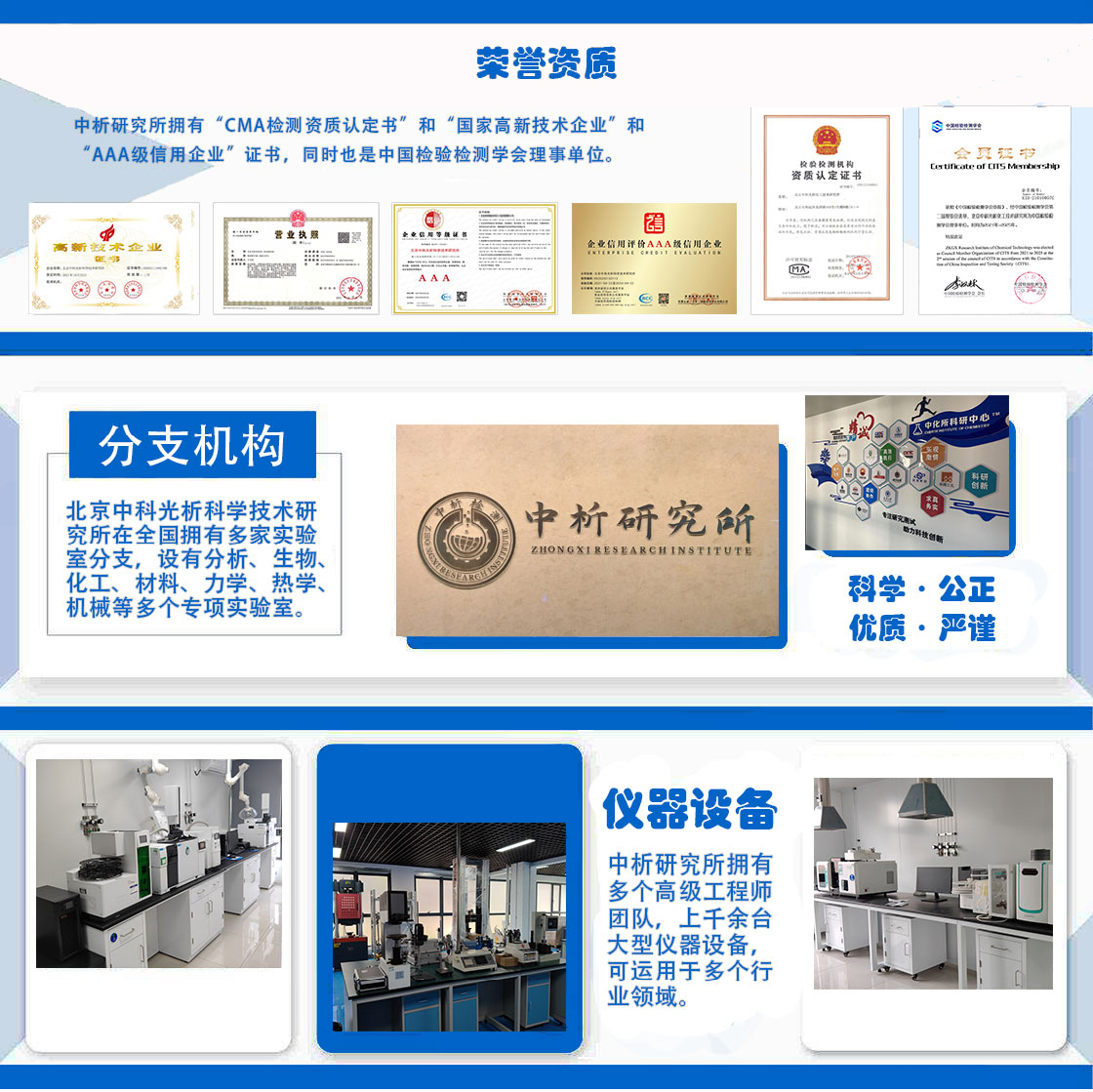
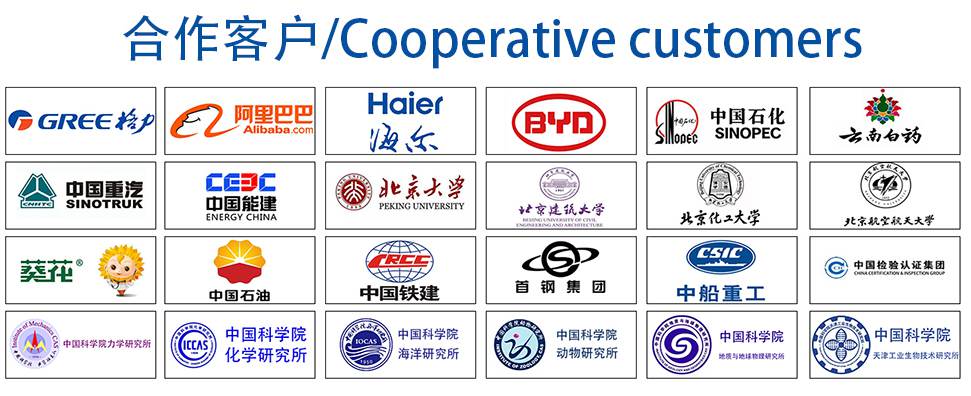