工作误差检测在工业领域的重要性
工作误差检测是工业生产、设备运维和质量管理中的核心环节,直接影响产品精度、生产效率和设备使用寿命。在制造业、自动化生产线、精密加工及仪器仪表等领域,设备或系统的实际输出与理论设计值之间的偏差(即工作误差)可能导致产品不合格、资源浪费甚至安全事故。通过科学的检测项目和方法,能够精准识别误差来源,优化工艺参数,保障设备运行稳定性。现代工业对误差检测的需求已从传统的人工抽检转向全流程智能化监测,结合传感器技术、数据分析及算法模型,实现误差的实时预警与闭环控制,从而提高良品率并降低维护成本。
工作误差检测的核心项目
1. 几何精度检测
包括导轨直线度、平面度、回转轴同轴度等基础精度指标,使用激光干涉仪、三坐标测量机(CMM)或电子水平仪等设备进行量化分析。例如,数控机床主轴径向跳动误差需通过千分表动态测量,确保加工中心运行轨迹符合设计要求。
2. 运动特性检测
针对设备的动态性能进行评价,如伺服系统响应速度、定位精度和重复性误差。通过动态测试仪或编码器记录运动轨迹数据,分析加减速阶段的振动、滞后现象,优化控制算法以减小跟随误差。
3. 重复定位精度检测
通过多次重复同一动作(如机械臂末端重复定位),结合激光跟踪仪或光栅尺测量实际坐标偏移量。该指标直接反映设备在连续作业中的稳定性,是自动化产线效能评估的关键参数。
4. 载荷误差检测
模拟设备在不同负载条件下的性能变化,检测传动部件(如齿轮箱、丝杠)的变形量与扭矩传递效率。使用力传感器和应变片采集数据,建立载荷-误差曲线,为结构优化提供依据。
5. 环境适应性检测
评估温度、湿度、振动等外部因素对设备精度的影响。例如,通过温控箱模拟极端工况,监测热膨胀导致的机械形变;或利用振动台测试设备抗干扰能力,确保在复杂环境下的误差可控。
6. 软件算法误差检测
针对数控系统、PLC控制逻辑等软件层面进行代码验证与仿真测试,识别插补运算误差、坐标转换偏差等潜在问题。借助MATLAB/Simulink等工具建立数字孪生模型,对比实际输出与理论值的差异。
检测技术与发展趋势
当前误差检测已深度融合物联网(IoT)与人工智能技术,通过边缘计算设备实时采集数据,结合深度学习模型预测设备劣化趋势。例如,利用振动频谱分析识别轴承磨损初期特征,或通过图像识别检测产品表面微观瑕疵。未来,随着5G通信和高精度传感器的普及,误差检测将向更高频次、更低延迟的方向发展,形成覆盖设计、生产、运维全周期的智能监测网络。
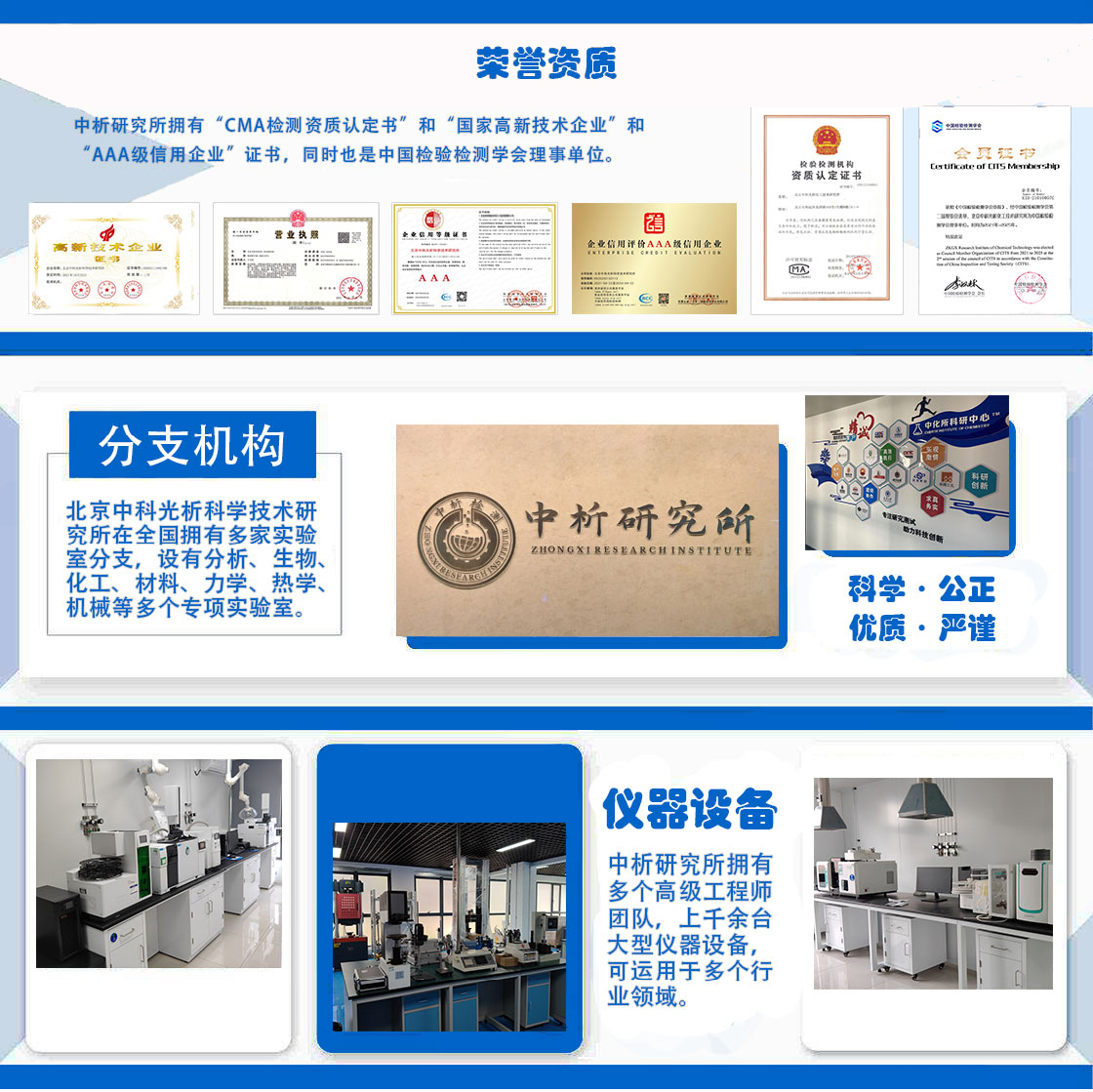
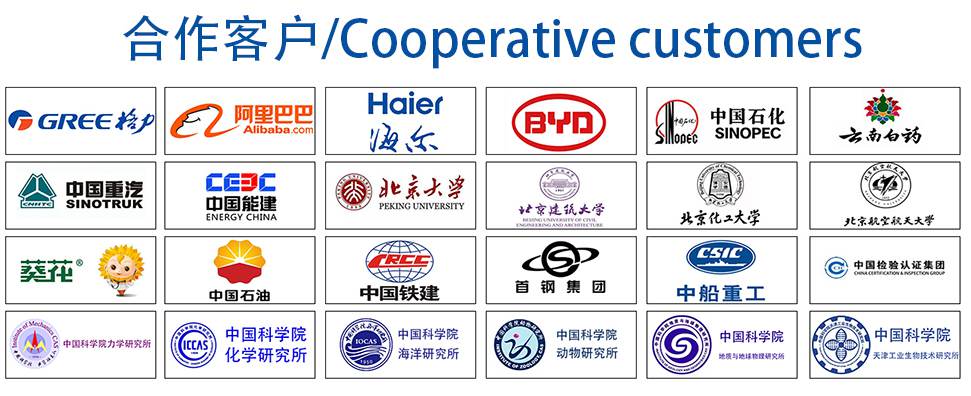