节流和压井管汇检测的重要性与技术要点
节流管汇和压井管汇是油气井控系统中的核心设备,承担着调节井口压力、控制溢流和井喷风险的关键作用。在钻井、完井或修井作业中,其性能直接影响作业安全与效率。由于长期承受高压、腐蚀性介质及复杂工况的冲击,管汇系统容易出现阀门卡阻、密封失效、结构疲劳等问题。因此,定期开展专业检测是保障设备可靠性、预防事故的必要手段。检测项目需覆盖结构完整性、密封性能、材料耐蚀性及功能性验证等多个维度,并严格遵循API 16C、SY/T 5323等行业标准,确保检测结果的科学性与权威性。
核心检测项目及方法
1. 结构完整性检测
通过目视检查、超声波测厚和磁粉探伤技术,重点检测管体焊缝、法兰连接处及阀门本体是否存在裂纹、变形或壁厚减薄现象。使用三维激光扫描技术验证管汇几何尺寸与设计图纸的匹配度,确保安装精度符合±2mm误差要求。
2. 密封性能测试
采用分段式压力测试法,对节流阀、手动闸阀及全系统进行额定压力1.5倍的水压/气压试验,保压时间不少于30分钟。同时使用氦气质谱仪检测微泄漏,泄漏率需低于10-6 mbar·L/s的行业安全阈值。
3. 材料性能分析
通过光谱分析仪验证管材成分(如35CrMo、F22合金钢)是否符合API 6A标准,并利用金相显微镜评估材料微观组织是否因硫化氢腐蚀或高温蠕变出现晶间裂纹。硬度测试范围需覆盖HB180-220的规范区间。
4. 动态功能验证
模拟实际工况进行节流阀开度调节响应测试,记录0-100%开闭循环中压力波动曲线,要求响应时间≤8秒且线性误差<5%。压井管汇需在紧急关断测试中实现0.5秒内全闭锁,同时验证远程控制系统的信号传输稳定性。
检测周期与维护策略
常规检测周期为每12个月一次,高强度作业井需缩短至6个月。检测数据需建立数字化档案,结合历史记录进行趋势分析,对磨损率超标的部件实施预防性更换。检测后应出具包含风险等级评估(如ASME B31.3分类)的正式报告,并针对密封面损伤、螺栓预紧力不足等典型问题提出研磨修复或扭矩校核等整改方案。
结语
通过系统化的节流和压井管汇检测,可显著降低井控失效风险,延长设备服役寿命。随着智能传感技术和数字孪生模型的应用,未来检测将向实时监测与预测性维护方向发展,为油气田安全运营提供更高效的技术支撑。
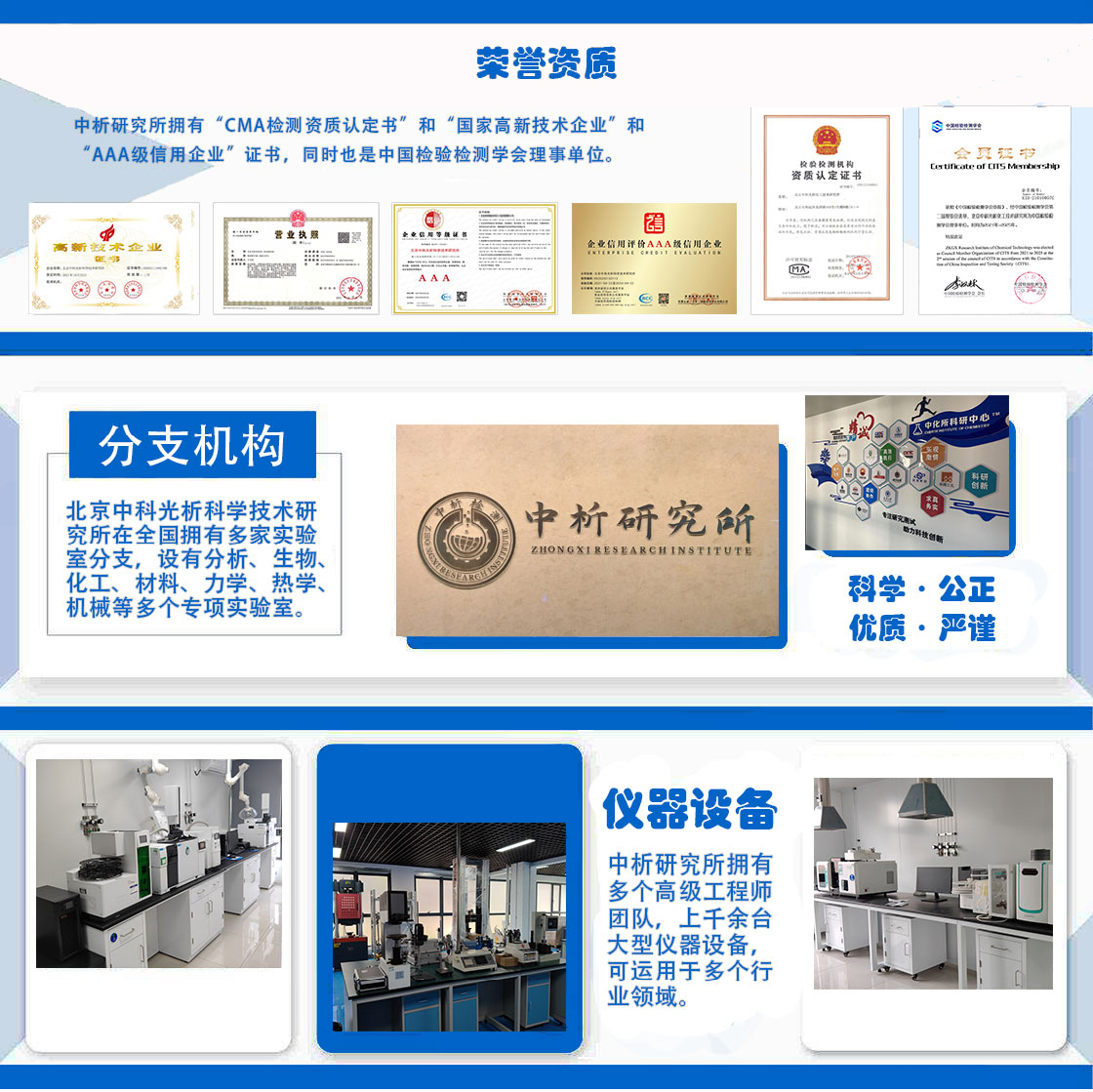
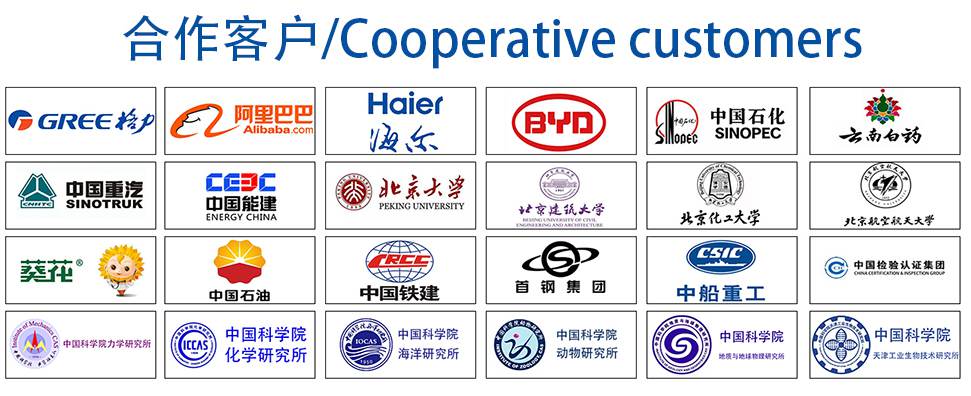