钻具螺纹检测的关键意义
在石油天然气、地质勘探和矿山开采等领域,钻具作为核心作业工具,其螺纹连接部位的可靠性直接关系到整个钻探系统的安全性与作业效率。钻具螺纹长期承受高频振动、轴向拉力及复杂地层压力,一旦出现磨损、变形或疲劳裂纹,可能引发断扣、泄漏甚至井下事故。因此,钻具螺纹检测是设备维护、质量管理及事故预防的关键环节。通过系统化的检测项目,可精准评估螺纹的几何精度、材料性能及服役寿命,为钻具的维修、报废或再制造提供科学依据。
钻具螺纹检测的核心项目
1. 螺纹外观与表面缺陷检测
采用目视检查结合工业内窥镜、高倍放大镜等设备,对螺纹牙型、倒角、根部圆角等部位进行表面质量评估。重点排查磕碰伤、腐蚀坑、机械磨损及裂纹等缺陷,尤其是应力集中区域的微裂纹需通过荧光渗透或磁粉探伤进一步确认。
2. 几何尺寸精度测量
使用螺纹通止规、三坐标测量仪或激光扫描仪,检测螺距、牙高、锥度、中径等参数是否符合API Spec 7-1、ISO 10424等标准。锥螺纹需验证其锥度一致性,确保公母螺纹的配合密封性。
3. 密封面接触率测试
通过染色剂接触法或专用压力敏感胶片,检测螺纹啮合后的密封面接触面积。要求主密封面的接触率不低于85%,次密封面不低于70%,以确保在高压工况下的密封性能。
4. 材料硬度与金相分析
采用里氏硬度计或显微硬度仪,检测螺纹表面及基体硬度是否满足HRC 22-28的行业要求。对频繁失效的螺纹进行金相组织观察,确认是否存在淬火裂纹、脱碳层或异常晶粒长大等冶金缺陷。
5. 无损探伤与疲劳评估
应用超声波探伤(UT)检测螺纹根部及过渡区的内部缺陷;涡流检测(ECT)用于表面裂纹筛查。对服役周期超过5万米的钻具,需通过疲劳寿命预测模型评估剩余使用次数。
6. 上卸扣扭矩与密封压力试验
在模拟工况下,使用液压扭矩扳手记录公母螺纹的旋合扭矩曲线,验证其是否在制造商规定的阈值范围内。同时进行水压或气压试验,检测螺纹连接在额定压力(如70MPa)下的密封可靠性。
检测流程与周期管理
钻具螺纹检测需遵循“入库检验-服役周期检测-退役前评估”的全生命周期管理模式。新钻具需100%全检,在役钻具每完成3-5口井作业或累计钻进5000米后必须进行复检。检测数据应录入数字化管理系统,实现趋势分析与预警。对于返修螺纹,需采用修扣机修复后重新进行精度校验,确保其性能恢复至设计标准的90%以上。
结语
钻具螺纹检测不仅是保障钻探作业安全的技术屏障,更是延长设备使用寿命、降低运维成本的重要手段。随着智能检测设备与AI图像识别技术的应用,螺纹检测正朝着高精度、自动化方向发展,为行业提供更高效可靠的解决方案。
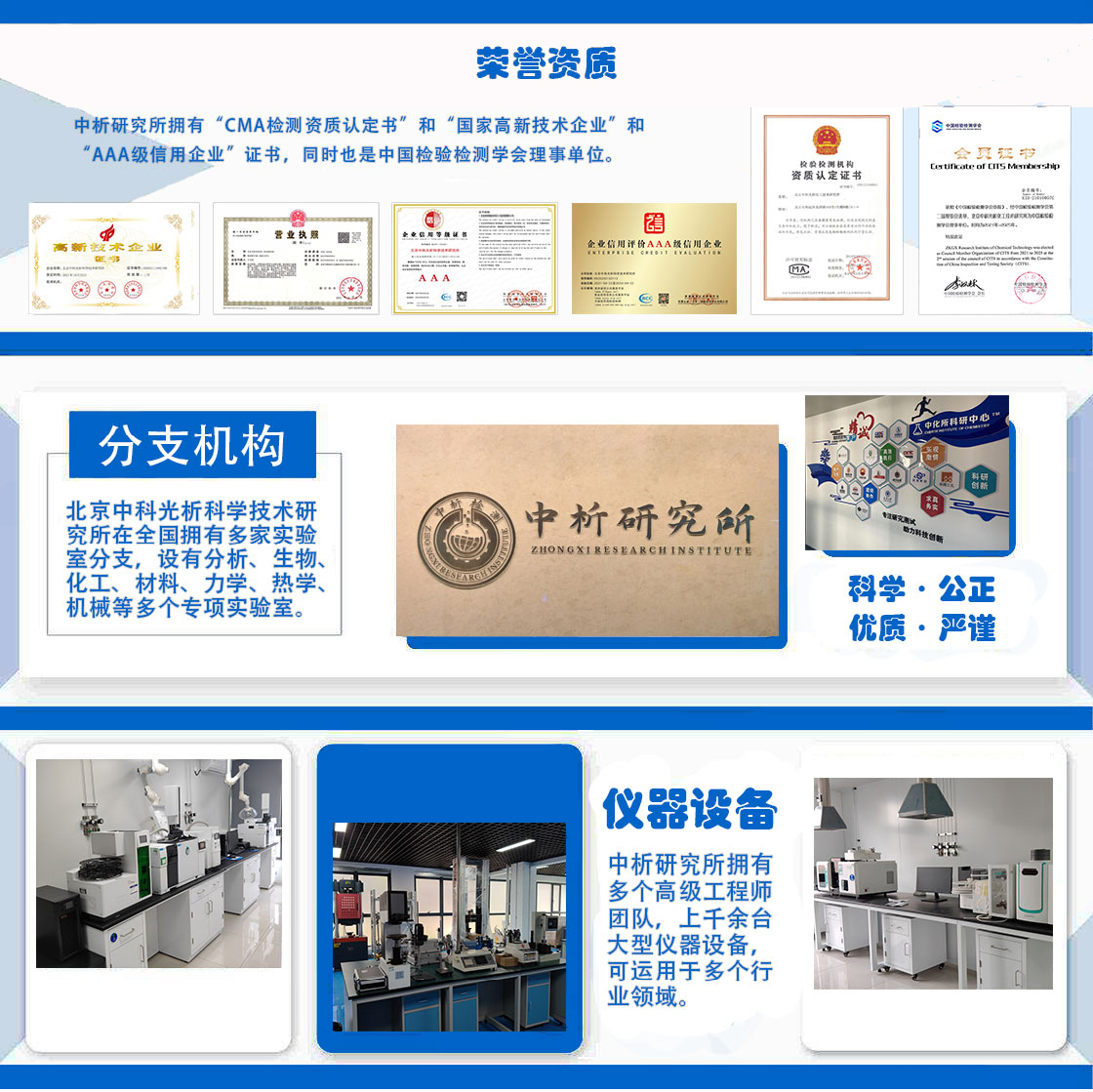
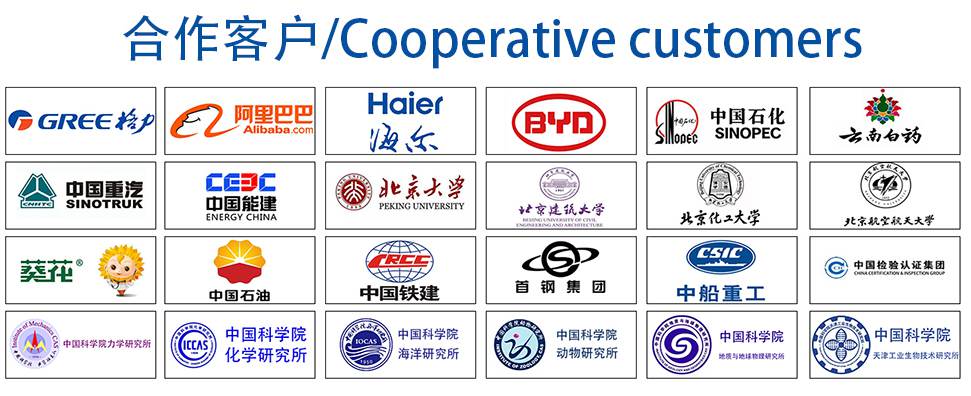