钻杆与钻铤检测的重要性及项目解析
在石油天然气勘探、地质钻探等工程领域,钻杆和钻铤作为钻井作业的核心工具,其性能直接关系到施工效率、安全性和成本控制。由于长期承受高压、高扭力、磨损及腐蚀等复杂工况,钻杆和钻铤易出现疲劳裂纹、壁厚减薄、螺纹损伤等问题。因此,定期开展科学规范的检测是预防设备失效、保障作业安全的关键环节。
钻杆与钻铤的核心检测项目
1. 尺寸精度检测:
包括外径、内径、壁厚、长度及直线度测量,确保符合API SPEC 7-1标准要求。过度磨损或变形可能导致钻井轨迹偏移或工具断裂风险。
2. 材料性能检测:
通过拉伸试验、冲击试验、硬度测试等方式验证材料力学性能,重点检测屈服强度、延伸率和低温韧性,防止因材料劣化引发脆性断裂。
3. 表面质量检测:
采用磁粉检测(MT)或渗透检测(PT)检查表面裂纹、腐蚀坑等缺陷;利用超声波测厚仪(UT)监测壁厚均匀性,定位内部蚀损区域。
4. 连接螺纹检测:
使用光学投影仪或三坐标测量机对螺纹牙型、螺距、锥度进行精密分析,配合通止规验证密封面完整性,防止因螺纹失效导致脱扣事故。
齐全检测技术的应用
当前行业普遍采用超声波相控阵(PAUT)实现三维缺陷成像,结合涡流检测(ECT)快速筛查表面微裂纹。对于关键部件,工业CT扫描可无损获取内部结构高清三维模型,精准评估损伤程度。此外,数字化检测系统可自动生成检测报告,实现数据追溯与寿命预测。
行业标准与检测周期要求
钻杆/钻铤检测需严格遵循API、ISO及SY/T系列标准:
- API SPEC 7-1 钻杆规范
- ISO 11961 石油天然气工业用钻杆
- SY/T 5146 钻铤技术条件
常规检测周期为单根钻杆每钻进5000小时或累计作业3口井后进行全面检测,高风险区域需缩短至2000小时。
典型检测案例分析
案例1:某油田在起钻时发现钻杆断裂,经超声波检测发现距接头1.2米处存在轴向疲劳裂纹,裂纹深度达壁厚60%,及时更换避免井下落鱼事故。
案例2:通过磁粉检测发现钻铤螺纹根部存在应力腐蚀裂纹,经分析为钻井液氯离子含量超标导致,优化泥浆配方后设备寿命提升40%。
结语
钻杆与钻铤的检测体系需覆盖从原材料到服役周期的全过程管理,结合智能化检测装备与大数据分析技术,可显著降低非计划性停机风险。企业应建立标准化检测流程,通过预防性维护延长工具寿命,为高效安全钻井作业提供坚实保障。
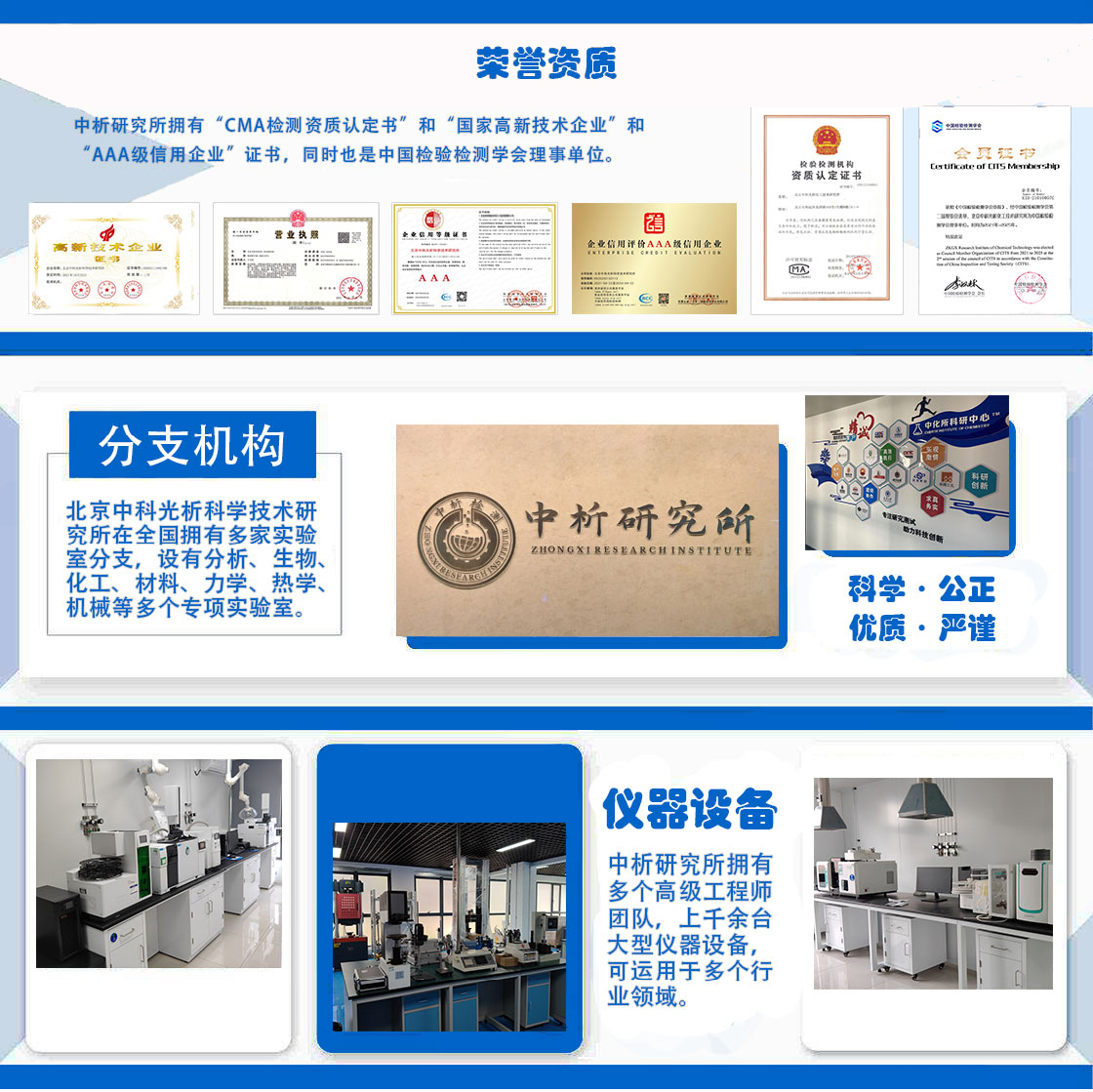
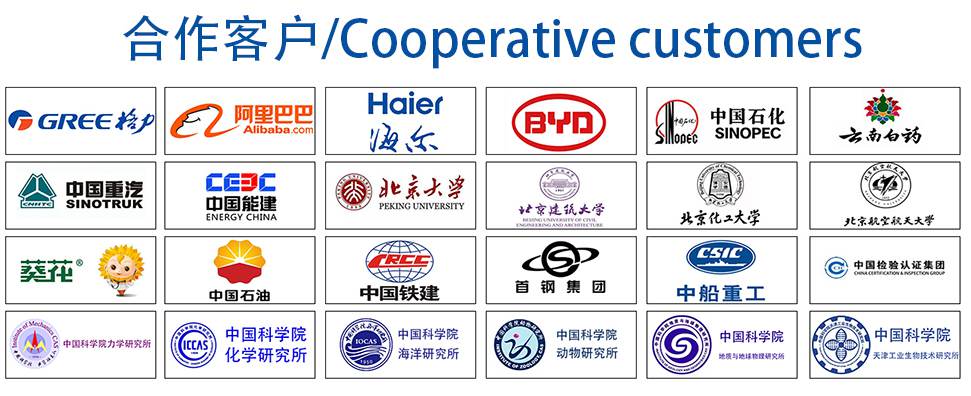