强制间歇式沥青混合料搅拌设备检测的重要性
强制间歇式沥青混合料搅拌设备作为道路建设领域的核心装备,其性能直接影响沥青混凝土的拌和质量、施工效率及工程成本。该设备由冷料供给系统、烘干筒、燃烧器、热料提升机、振动筛、计量系统、搅拌缸和除尘系统等组成,各环节的协同运作对最终混合料的级配、温度均匀性和稳定性具有决定性作用。定期开展专业检测能够确保设备符合《GB/T 17808-2010 道路施工与养护设备 沥青混合料搅拌设备》等国家标准,有效预防因设备故障导致的材料浪费、工期延误及质量缺陷,同时为节能减排和智能化生产提供数据支撑。
关键检测项目与技术要求
1. 冷料供给系统检测
通过皮带称重传感器验证各规格骨料的计量精度,误差需控制在±2%以内。同步检查变频调速装置响应速度,确保不同粒径骨料的配比稳定性,避免级配离析。
2. 烘干加热系统检测
使用红外测温仪监测烘干筒进出口温度梯度,评估燃烧器热效率。重点校验火焰监测装置灵敏度,要求筒体表面温度差≤15℃,燃料消耗量应符合设备标定值±5%范围。
3. 搅拌系统性能检测
采用扭矩传感器测试搅拌轴功率波动,验证叶片磨损程度。检测卸料门密封性时,需进行30次连续开闭试验,确保漏料量<0.5kg/次。搅拌时间设定误差应不大于±0.5秒。
4. 计量系统标定检测
使用标准砝码对沥青称量罐进行静态标定,动态计量误差须≤±1%。粉料计量系统需进行螺旋输送机给料均匀性测试,10次连续计量变异系数应<3%。
5. 环保性能检测
采用粉尘浓度测定仪检测除尘器排放口颗粒物浓度,布袋除尘器排放应≤20mg/m³,湿式除尘器≤50mg/m³。噪声检测点距设备外壳1m处,昼间限值85dB(A)。
6. 电气控制系统检测
模拟故障测试PLC程序的连锁保护功能,验证温度超限、电机过载等报警响应时间≤2秒。检查HMI界面参数设置权限管理,关键工艺参数修改需具备三级密码保护。
检测周期与方法
新设备安装后应进行72小时空载运行和48小时负载测试,生产季每月开展1次常规检测,累计运行2000小时需实施全面性能评估。检测过程应采用振动分析仪、热成像仪等智能诊断设备,结合生产数据建立设备健康档案,实现预测性维护。
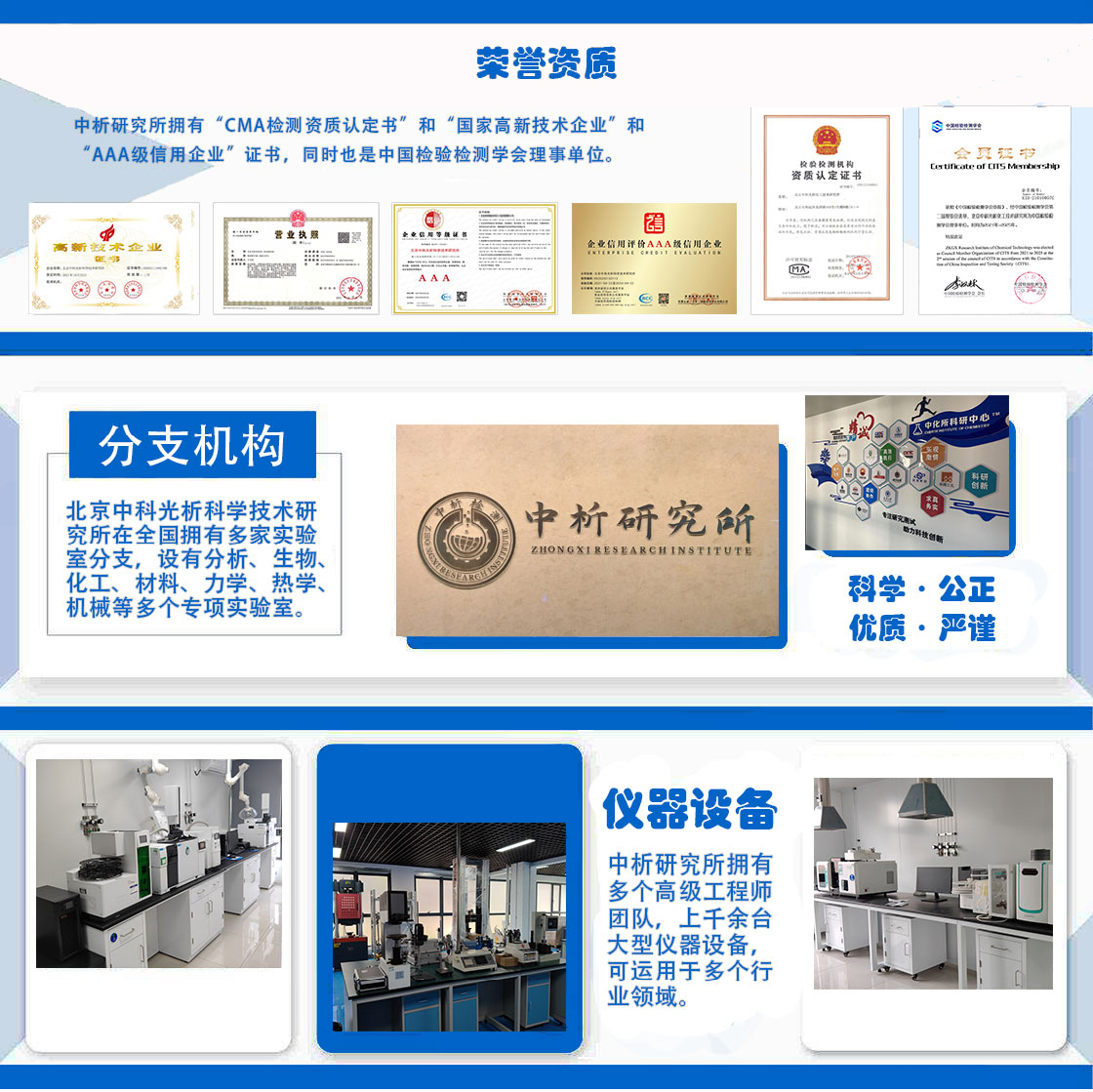
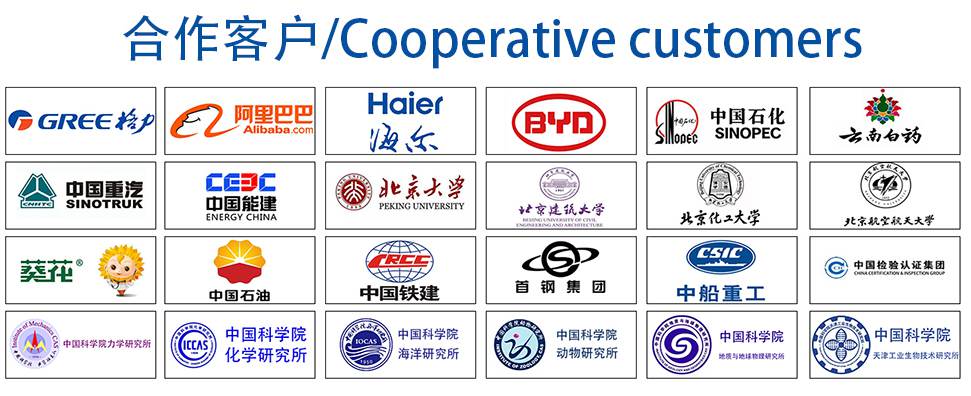