作为高速铁路轨道结构中的核心部件,扣件系统承担着固定钢轨位置、传递列车载荷、吸收振动能量的重要功能。其性能直接关系着轨道几何形位的稳定性与列车运行安全性。我国高铁网络日均发送旅客超700万人次,钢轨扣件长期承受着高频次、高强度的动态载荷,在复杂气候环境和地质条件下极易出现疲劳损伤、螺栓松动、绝缘失效等问题。为确保高铁运营安全,铁路部门建立了覆盖全生命周期的扣件检测体系,形成了从生产质检到日常维护的多层级技术规范。
一、扣件外观质量检测
通过高清摄像系统与人工复核相结合的方式,对扣件表面进行360°扫描检测。重点检查弹条表面是否存在裂纹、锈蚀、镀层剥落,轨距块是否发生塑性变形,锚固螺栓螺纹完整度,尼龙套管老化程度等可视缺陷。采用图像识别算法自动标记异常区域,对直径≥0.5mm的表面裂纹实现99.3%的检出率。
二、机械性能参数检测
在万能材料试验机上开展扣件系统力学测试:弹条需满足≥18kN的扣压力要求,经过300万次疲劳试验后残余变形量不超过1mm;轨距挡板承受60kN横向力时位移量≤2mm;绝缘垫板在25MPa压强下的压缩永久变形不超过5%。所有测试数据需符合TB/T3395-2015《高速铁路扣件系统》技术标准。
三、绝缘电阻性能检测
使用500V兆欧表在相对湿度85%环境下测量扣件系统各组件间绝缘电阻值。轨距块与铁垫板间的绝缘电阻应≥10⁹Ω,尼龙套管绝缘阻抗需>5×10¹⁰Ω。特别在潮湿多雨地区,需增加盐雾试验验证,确保在模拟沿海气候条件下2000小时测试后绝缘性能不衰减。
四、安装状态动态监测
采用智能扭矩扳手结合应力波检测技术,对线路扣件实施紧固力普查。弹条扣压力需保持在8-12kN范围,锚固螺栓扭矩值应达250-300N·m。通过安装微型传感器实时监测扣件位移变化,当弹条与轨距挡板间隙超过1.5mm时触发预警,定位精度可达±0.1mm。
五、无损探伤深度检测
针对服役中的扣件系统,采用阵列涡流检测技术探查弹条内部缺陷,可识别深度2mm以内的皮下裂纹。对铁垫板等铸件使用工业CT扫描,检测最小0.1mm的气孔夹杂缺陷。相控阵超声波技术可穿透30mm厚部件,实现螺栓根部裂纹的三维成像检测。
当前我国高铁扣件检测已形成智能化技术体系,综合运用机器视觉、物联网传感、大数据分析等手段,检测效率较传统方式提升12倍。新建线路扣件合格率稳定在99.98%以上,运营线路故障率控制在0.03次/万公里以下,有力支撑着中国高铁的世界领先地位。
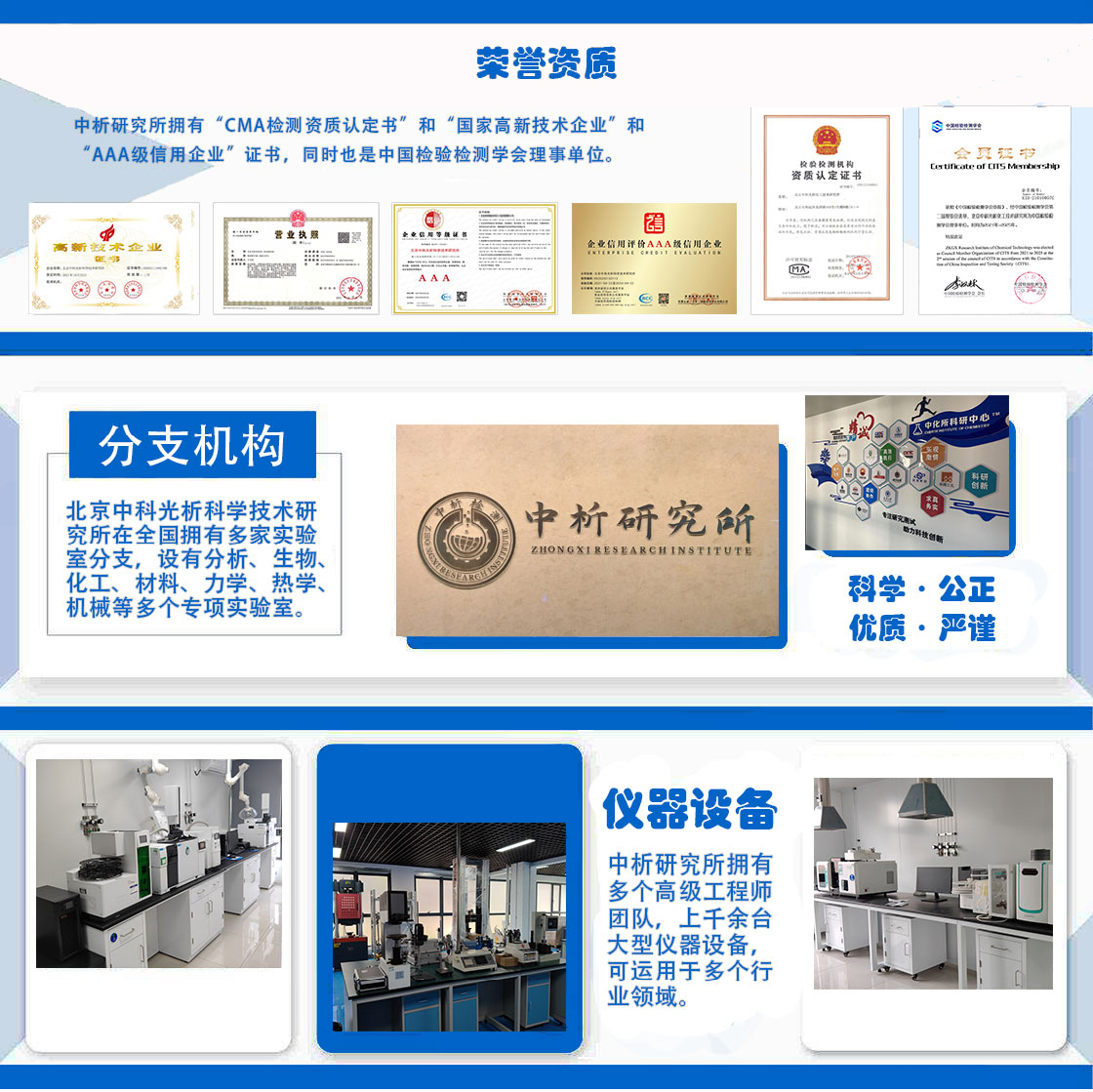
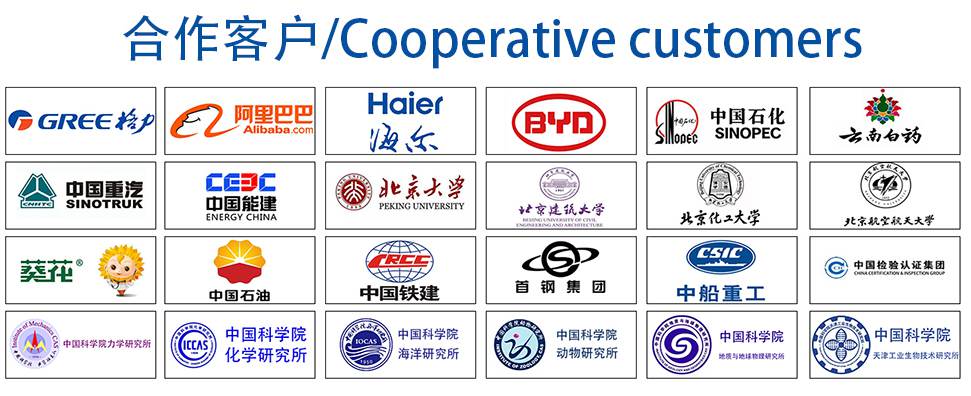