往复运动密封圈橡胶材料检测的必要性与关键项目
往复运动密封圈是液压系统、气动装置及机械传动设备中的核心部件,其性能直接影响设备的密封性、使用寿命和运行效率。橡胶材料作为密封圈的主要原料,需在动态摩擦、高压冲击、温度变化等复杂工况下保持稳定的物理化学特性。为确保密封圈的可靠性,对其橡胶材料的检测需覆盖力学性能、耐介质性、耐磨性、热稳定性等关键指标,并通过标准化测试方法验证是否符合行业规范(如GB/T、ISO、ASTM等)。
核心检测项目及技术要求
1. 物理机械性能检测
包括拉伸强度、断裂伸长率、硬度(邵氏A)和压缩永久变形测试。其中,压缩永久变形反映材料在长期压缩后恢复原状的能力,直接影响密封圈在往复运动中的回弹性能。测试需模拟实际工况条件,如高温环境下的压缩率测试(典型标准:GB/T 7759)。
2. 耐介质性能测试
密封圈常接触液压油、润滑油或腐蚀性介质,需检测材料在液体浸泡后的体积变化率、质量变化率和力学性能衰减。例如,根据ASTM D471标准,浸泡72小时后体积膨胀率应≤10%,且硬度变化不超过±5 IRHD。
3. 动态摩擦与耐磨性评估
通过往复式摩擦试验机模拟密封圈的实际运动状态,测量动态摩擦系数和磨损量。高精度传感器可记录摩擦力波动,结合表面形貌分析(如SEM扫描电镜),评估材料抗磨粒磨损和黏着磨损的能力。
4. 热稳定性与低温性能
测试材料在高温(如150℃×72h)下的热老化性能,以及低温(-40℃)下的弹性保持率。热重分析(TGA)可检测材料分解温度,而低温脆性试验(GB/T 15256)则验证其抗寒脆裂能力。
5. 耐臭氧与抗老化性能
针对户外或臭氧环境应用,需进行臭氧老化试验(ASTM D1149)。将试样暴露于50pphm臭氧浓度、40℃环境中72小时,观察表面是否出现龟裂,评估材料抗氧化降解能力。
检测结果与质量控制
通过以上项目综合评估,可建立橡胶材料的性能数据库,指导配方优化和生产工艺调整。企业需结合产品使用场景制定检测标准,例如工程机械密封圈需强化耐磨和耐高压检测,而食品级设备密封圈则需额外通过FDA或LFGB认证的化学安全性测试。
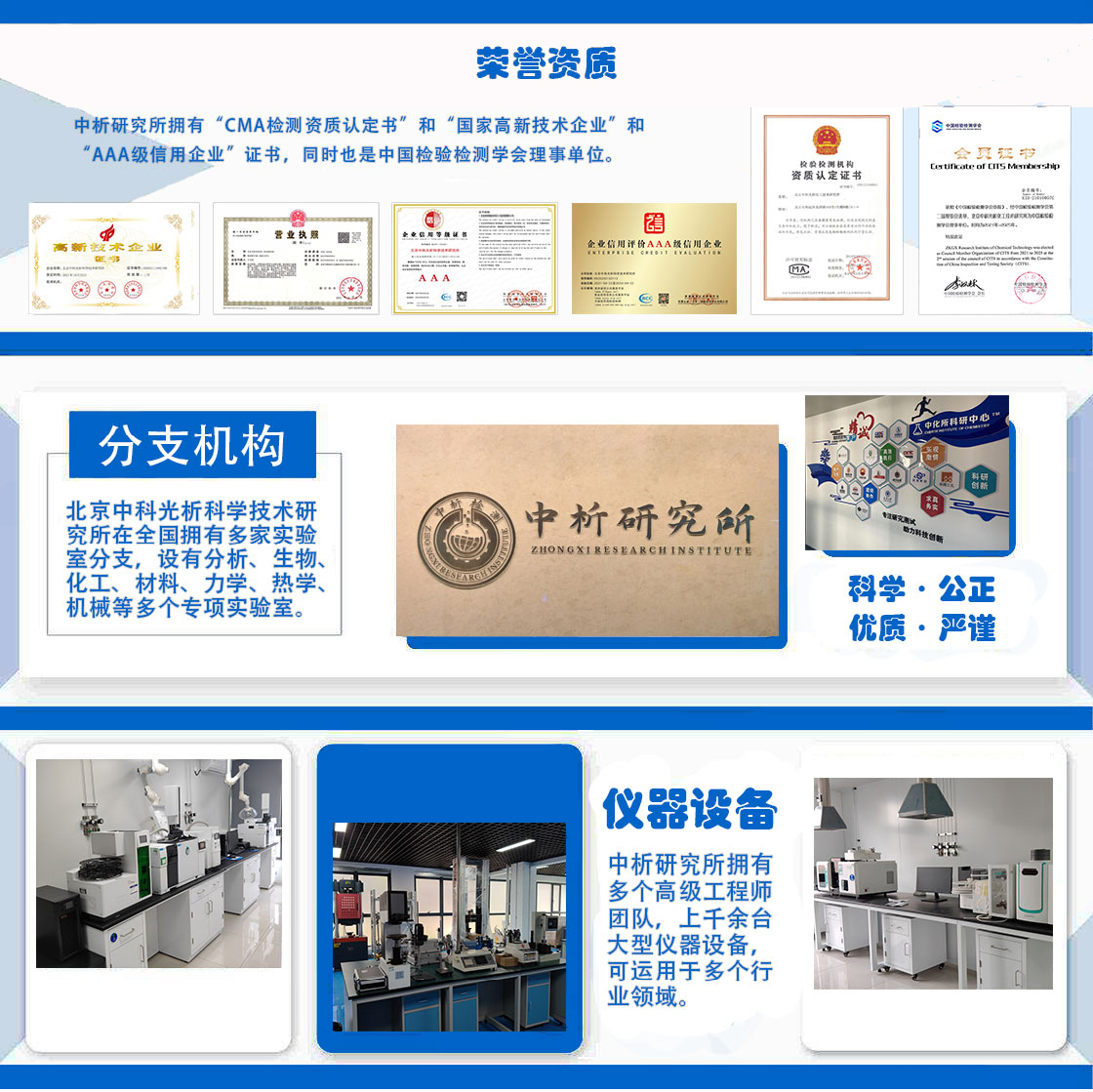
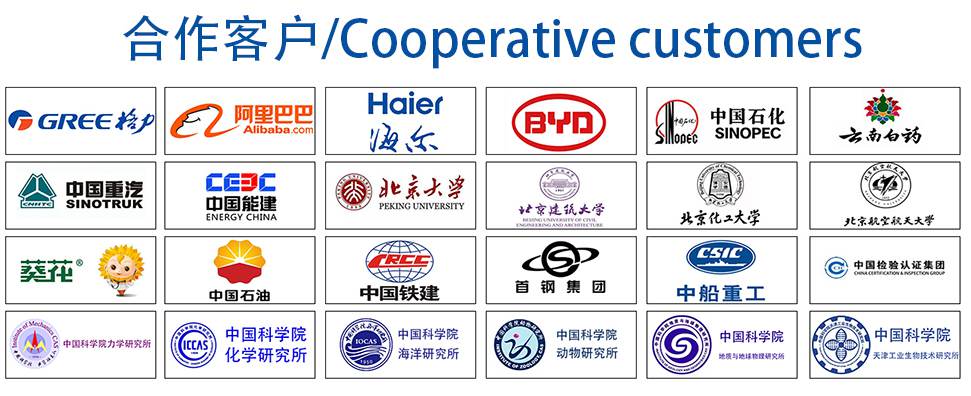