圆块孔式不透性石墨降膜吸收器检测概述
圆块孔式不透性石墨降膜吸收器是一种广泛应用于化工、制药、环保等领域的特种设备,其核心材料为不透性石墨,具有优异的耐腐蚀性、导热性和化学稳定性。该设备通过降膜吸收原理实现气液传质过程,常用于酸性气体(如HCl、SO3等)的吸收与处理。为确保设备长期稳定运行及安全生产,定期开展全面检测至关重要。检测内容需覆盖材料性能、结构完整性、工艺参数匹配性及安全可靠性等多个维度,以预防泄漏、堵塞或材料劣化等潜在风险。
关键检测项目及方法
1. 材料性能检测
重点评估不透性石墨的理化特性,包括抗压强度(≥25MPa)、孔隙率(≤0.5%)及浸渍剂残留量检测。通过X射线衍射(XRD)分析石墨晶体结构,结合热重分析(TGA)验证材料在高温工况下的稳定性。同时需检测石墨块与黏结剂(如酚醛树脂)的界面结合强度,确保无分层或裂纹缺陷。
2. 孔道结构检查
采用工业内窥镜对降膜孔、冷却孔的分布均匀性及孔径精度(±0.1mm)进行可视化检测,配合激光扫描测量孔道倾斜角度(通常为3°-5°)。检查孔道内壁是否存在结垢、腐蚀或异物堵塞,必要时进行高压水射流清洗前后的压降对比测试。
3. 密封性能验证
按照HG/T 2370标准进行水压试验(1.5倍设计压力)和气密性试验(0.6MPa保压30分钟)。重点检测石墨块拼接缝、法兰连接处及管口密封点的泄漏情况,使用氦质谱检漏仪对微泄漏进行定量分析,泄漏率应≤1×10^-6 Pa·m³/s。
4. 工艺参数匹配性检测
通过模拟工况测试液膜分布均匀性,采用高速摄像技术观察降膜形成状态,确保液膜厚度保持在0.5-1.2mm范围内。检测气液比(通常控制在1:2至1:5)、吸收效率(≥95%)及出口气体残余浓度,验证设备与工艺条件的适配性。
5. 腐蚀与老化评估
定期进行壁厚测量(精度±0.1mm)及表面硬度测试(巴氏硬度≥50HBa),利用电化学工作站检测材料极化曲线。对使用5年以上的设备,需进行渗透探伤(PT)或超声波探伤(UT)以发现内部微裂纹。同时检测密封垫片(如PTFE)的压缩永久变形率(≤15%)。
6. 安全附件与控制系统检测
校验压力表、温度传感器及液位计的精度等级(不低于1.6级),测试紧急切断阀的响应时间(≤3秒)。对自动控制系统进行联锁逻辑验证,包括超温报警(设定值±2℃)、流量异常保护等功能测试。
检测周期与标准依据
推荐每12个月进行定期检测,连续运行工况下应缩短至6个月。检测过程需严格参照《压力容器安全技术监察规程》(TSG 21-2016)、《石墨制化工设备技术条件》(HG/T 2370-2017)等标准。对于检测中发现的气孔率超标、应力腐蚀裂纹等缺陷,应根据NB/T 47013进行安全等级评定,并制定修复或更换方案。
总结
圆块孔式不透性石墨降膜吸收器的系统化检测是保障装置长周期安全运行的核心措施。通过多维度的检测数据采集与综合分析,可有效预判设备老化趋势,优化维护策略。建议企业建立数字化检测档案,结合运行数据实现预测性维护,最大限度降低非计划停机风险,提升经济效益。
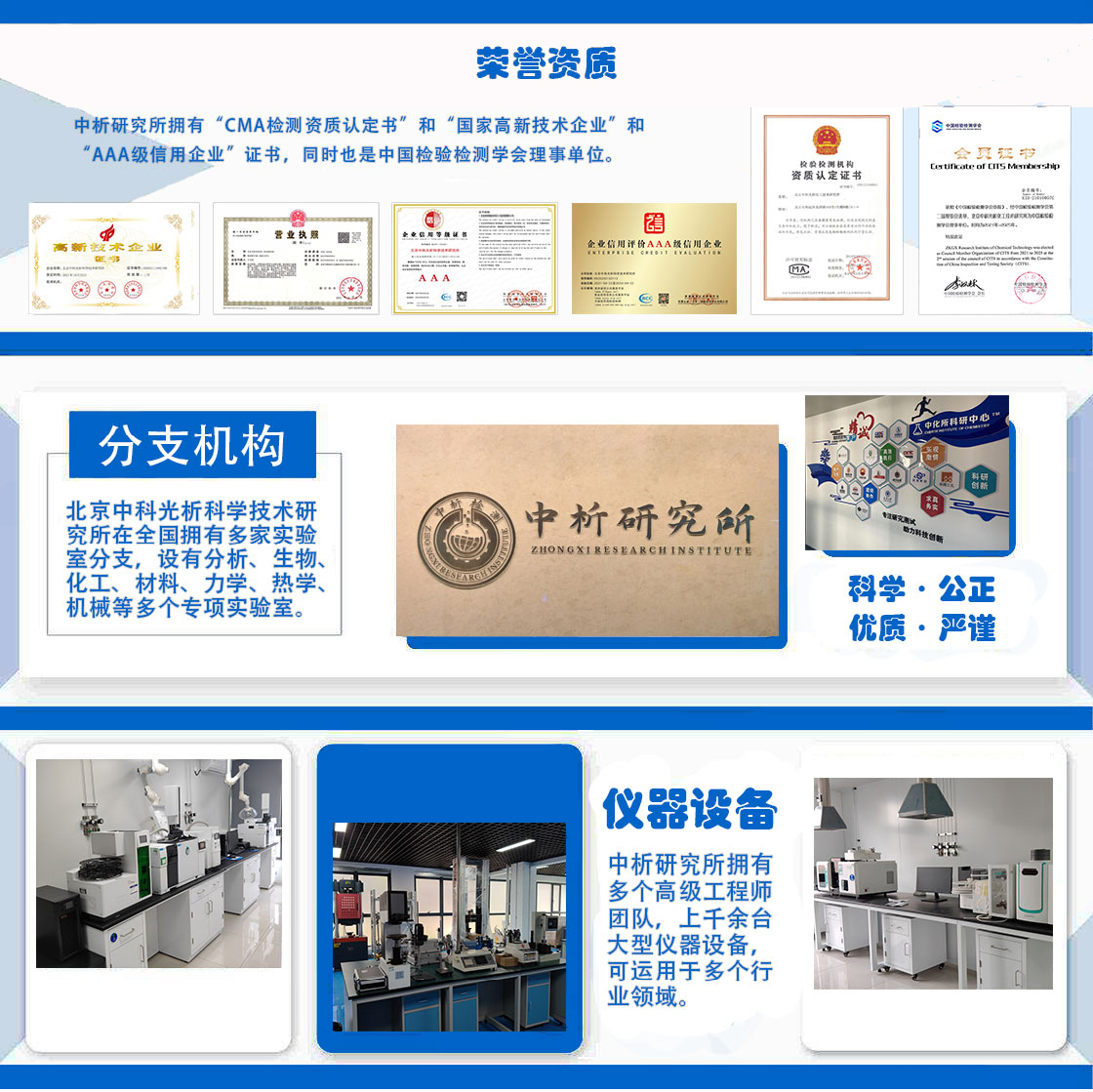
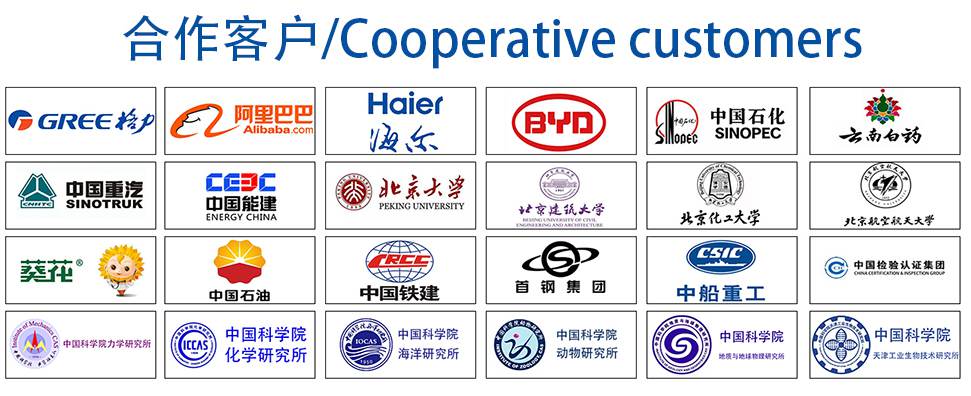