空气压缩机及供气系统节能监测检测的重要性
空气压缩机作为工业领域重要的动力设备,其能耗约占工业企业总用电量的10%-30%。供气系统的运行效率直接影响企业能源成本与碳排放水平。随着"双碳"目标推进,开展空气压缩机及供气系统的节能监测检测已成为企业实现能效提升、降低运营成本的关键举措。通过系统化的检测分析,可精准识别设备老化、管网泄漏、控制策略不合理等典型问题,为制定节能改造方案提供科学依据。
核心检测项目与实施要点
1. 压缩机运行参数监测
重点检测排气压力、排气温度、电流电压等实时数据,结合设备额定参数评估运行状态。采用智能电表连续记录能耗数据,分析加载/卸载时间比,判断是否存在空载损耗。通过红外热像仪检测电机温升情况,评估机械传动系统效率。
2. 管网系统泄漏检测
运用超声波检漏仪对管道、阀门、法兰等连接部位进行全面扫描,量化泄漏量。统计管网压力损失,结合压降曲线分析管道布局合理性。检测储气罐排水阀启闭状态,评估无效排气损失。
3. 系统能效评估
依据GB 19153《容积式空气压缩机能效限定值及能效等级》标准,计算机组比功率(kW/m³·min)。对比设备铭牌参数与实际运行数据,绘制能耗负荷曲线。通过流量计测量有效供气量,核算系统整体能效比率。
4. 控制策略分析
检测压力带设置合理性,评估多机联控策略的有效性。检查变频器调节范围与负载匹配度,分析PID控制参数优化空间。验证智能控制系统对用气波动的响应能力,识别人工干预导致的效率损失。
检测后的节能优化方向
基于检测结果,企业可针对性实施节能改造:修复管网泄漏点可降低5-15%能耗;优化压力设定每降低0.1MPa可节约7%电耗;采用高效变频控制系统可实现20-30%节能量;余热回收系统可将70%废热转化为可利用能源。定期开展能效检测与设备维护,可确保系统持续保持最佳运行状态。
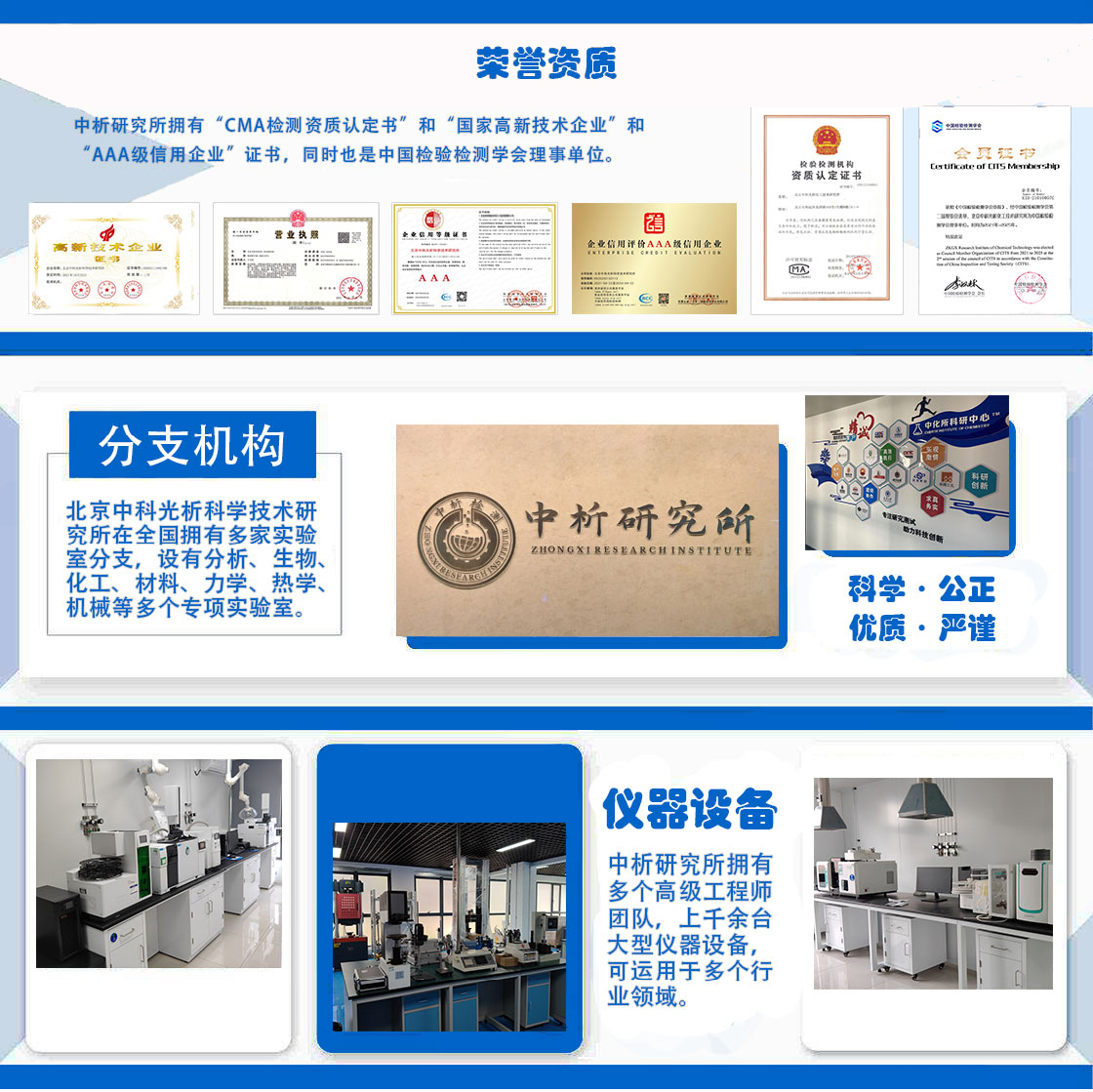
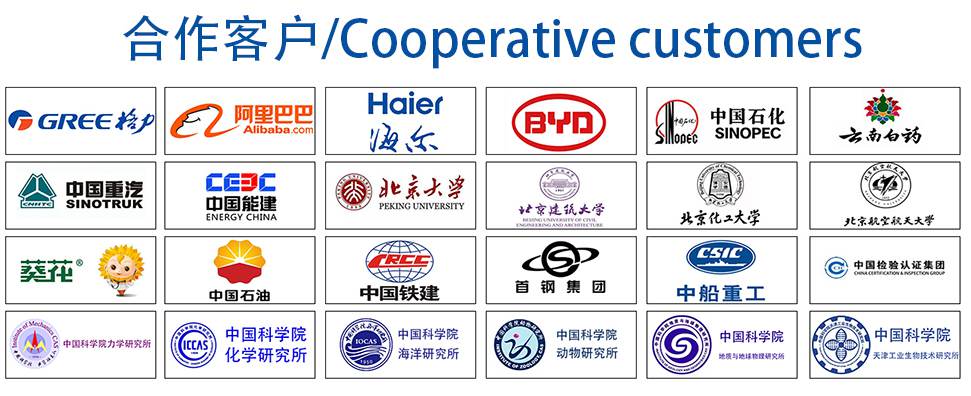