耐磨氧化铝球检测的核心意义
耐磨氧化铝球作为工业研磨领域的关键耗材,广泛应用于矿山、化工、陶瓷、电子材料等行业的粉体加工环节。其性能优劣直接影响生产效率和产品质量,而检测是确保材料性能达标的核心手段。通过系统化的检测项目,可验证氧化铝球的化学成分、物理强度、耐磨性能及微观结构是否满足行业标准(如GB/T 14398-2015《工业氧化铝陶瓷研磨介质》),从而避免因研磨介质失效导致的设备磨损、能耗增加或产品污染。当前行业内对氧化铝球的检测要求已从单一指标验证转向全生命周期性能评估,检测技术也逐步向自动化、高精度方向发展。
核心检测项目与技术要求
1. 化学成分分析:通过X射线荧光光谱仪(XRF)测定Al₂O₃含量(一般要求≥92%),同时检测SiO₂、Fe₂O₃等杂质元素占比。高纯度氧化铝可提升球体硬度和耐磨性,而杂质超标会导致晶界脆化。
2. 物理性能检测: - 体积密度测试:采用阿基米德排水法,要求≥3.60g/cm³ - 洛氏硬度检测(HRA≥85) - 抗压强度测试:单球破碎强度需>1500N - 真圆度检测:球体直径偏差需控制在±0.2mm以内
3. 耐磨性专项测试: - 落砂法磨损量检测:采用石英砂为磨料,测试万次冲击后质量损失率 - 湿磨试验:模拟实际工况进行24小时连续研磨,检测表面磨损形貌
4. 微观结构分析: - SEM扫描电镜观察晶粒尺寸(理想值2-5μm) - XRD检测α-Al₂O₃相含量(要求≥95%) - 气孔率测定(需<0.5%)
检测技术创新与行业趋势
随着智能制造的发展,耐磨氧化铝球检测呈现三个新特征:一是引入AI图像识别技术实现磨损形貌的智能分级;二是开发在线监测系统实时追踪研磨过程的性能衰减;三是建立材料数据库实现检测数据与生产工艺的联动优化。第三方检测机构现已普遍采用ISO 9001质量管理体系,部分企业开始推行ASTM E384显微硬度测试等国际标准,推动行业检测水平与国际接轨。
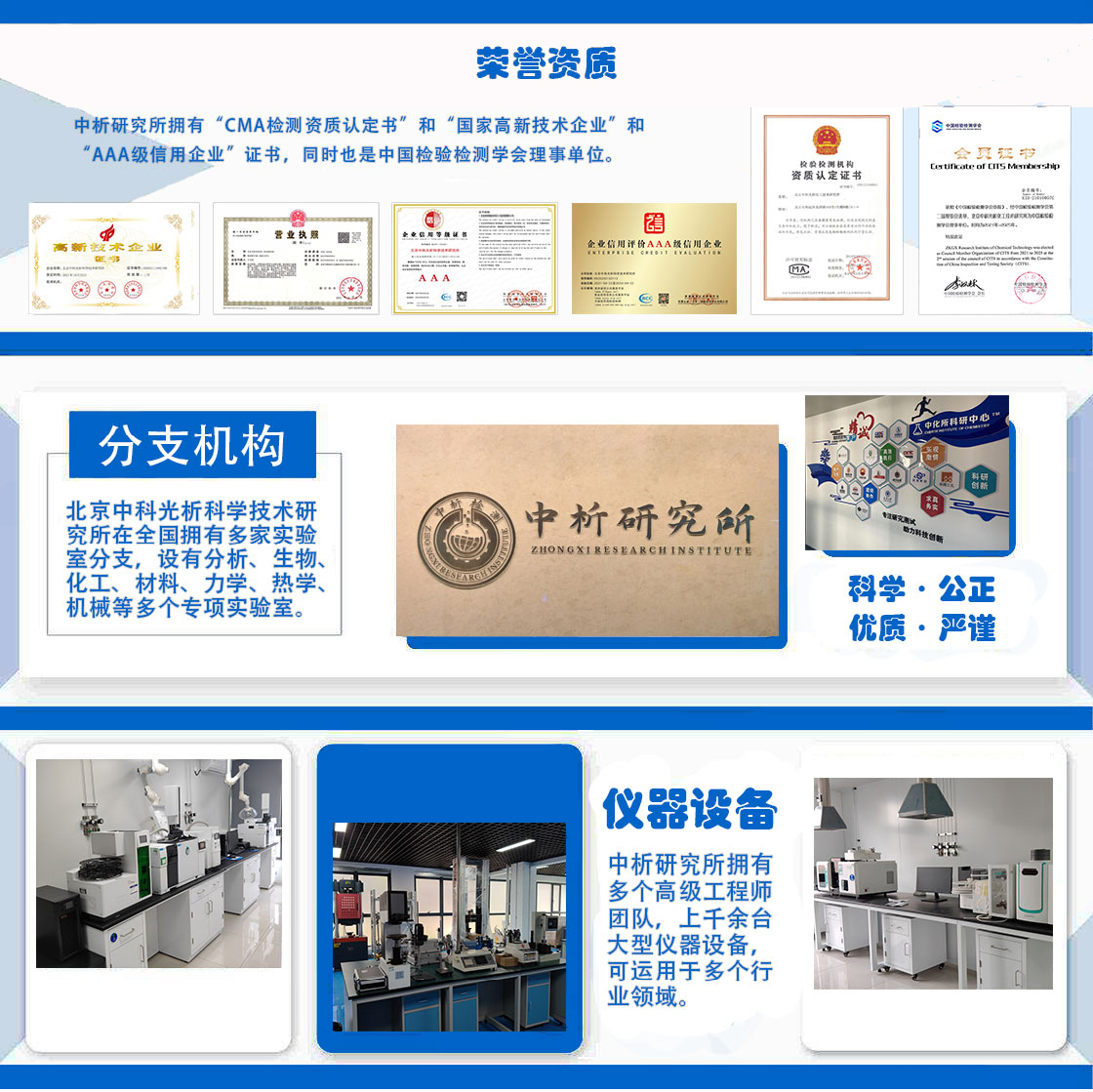
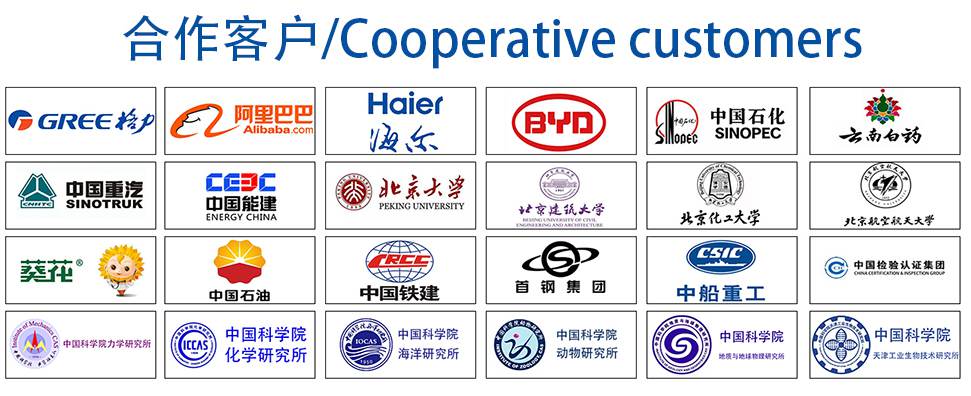