正多面棱体检测:确保几何精度的关键环节
正多面棱体是一种广泛应用于精密机械制造、光学仪器和测量设备的高精度多面体结构,其每个面均具有严格的几何形状与角度要求。在航空航天、数控机床、高精度分度装置等领域,正多面棱体的加工精度直接影响设备的整体性能。因此,通过系统性检测验证其平面度、角度偏差、表面粗糙度等参数,是保障产品质量的核心步骤。检测过程需结合光学、机械和数字化测量技术,确保各面之间的角度误差控制在微米级甚至更高精度范围内。
检测项目一:平面度误差分析
正多面棱体的每个工作面需满足严格的平面度要求。检测时通常采用激光平面干涉仪或高精度平晶,通过观察干涉条纹的形态判断平面平整度。对于大尺寸棱体,可使用三坐标测量机(CMM)进行多点采样,生成三维平面模型并计算最大偏差值。允许误差范围根据应用场景不同,通常控制在0.1-1μm/m²内。
检测项目二:相邻面角度偏差测量
各工作面间的角度精度是正多面棱体的核心参数。检测时需使用分度误差≤0.5角秒的高精度分度台,配合自准直仪或光电自准直仪进行逐面角度比对。针对n面棱体,理论相邻面夹角为360°/n,实测值与理论值的偏差需符合GB/T 17163-2008《多面棱体》规定的精度等级(如0级≤±1角秒,1级≤±3角秒)。
检测项目三:工作面平行度与垂直度验证
对于具有轴向延伸结构的正多面棱柱体,需额外检测端面与侧面的平行度及相邻面的垂直度。采用气浮转台搭配电感测微仪,可在旋转过程中实时监测各面的位置偏差。典型检测流程包含轴向加载定位、多点循环测量及数据滤波处理,以消除环境振动带来的干扰。
检测项目四:表面粗糙度与材质均匀性评估
工作面表面粗糙度(Ra值)直接影响测量信号的反射质量,通常要求Ra≤0.05μm。采用白光干涉仪或原子力显微镜(AFM)进行微观形貌分析,同时配合金相显微镜检测材料晶粒结构,避免因内部应力不均导致的角度稳定性劣化。对于金属材质棱体,还需通过超声波探伤仪检测内部缺陷。
数字化检测技术的创新应用
随着工业4.0的发展,基于机器视觉的在线检测系统逐渐普及。通过多轴机器人搭载激光跟踪仪,可实现正多面棱体的全自动快速检测,结合数字孪生技术同步生成三维误差云图。德国PTB等机构已开发出基于量子测量的角度基准装置,将检测不确定度推进至0.01角秒量级,为超精密制造提供技术支撑。
检测标准与质量控制体系
正多面棱体检测需严格遵循ISO 8512-3:2019《多面棱体的验收试验条件》及JJG 472-2007《多齿分度台检定规程》。企业应建立包含来料检测、过程监控和出厂终检的三级质量体系,关键参数采用SPC统计过程控制,确保批量产品的一致性。定期参与NIST或 组织的实验室比对,验证检测系统的溯源性。
结语
正多面棱体的检测技术融合了几何计量、材料科学和自动控制等多学科知识,其精度水平直接反映一个国家高端装备制造业的竞争力。随着新型光学材料和智能传感器的发展,未来检测将向非接触式、实时反馈的方向演进,为量子测量、光刻机等尖端领域提供更可靠的基础元件保障。
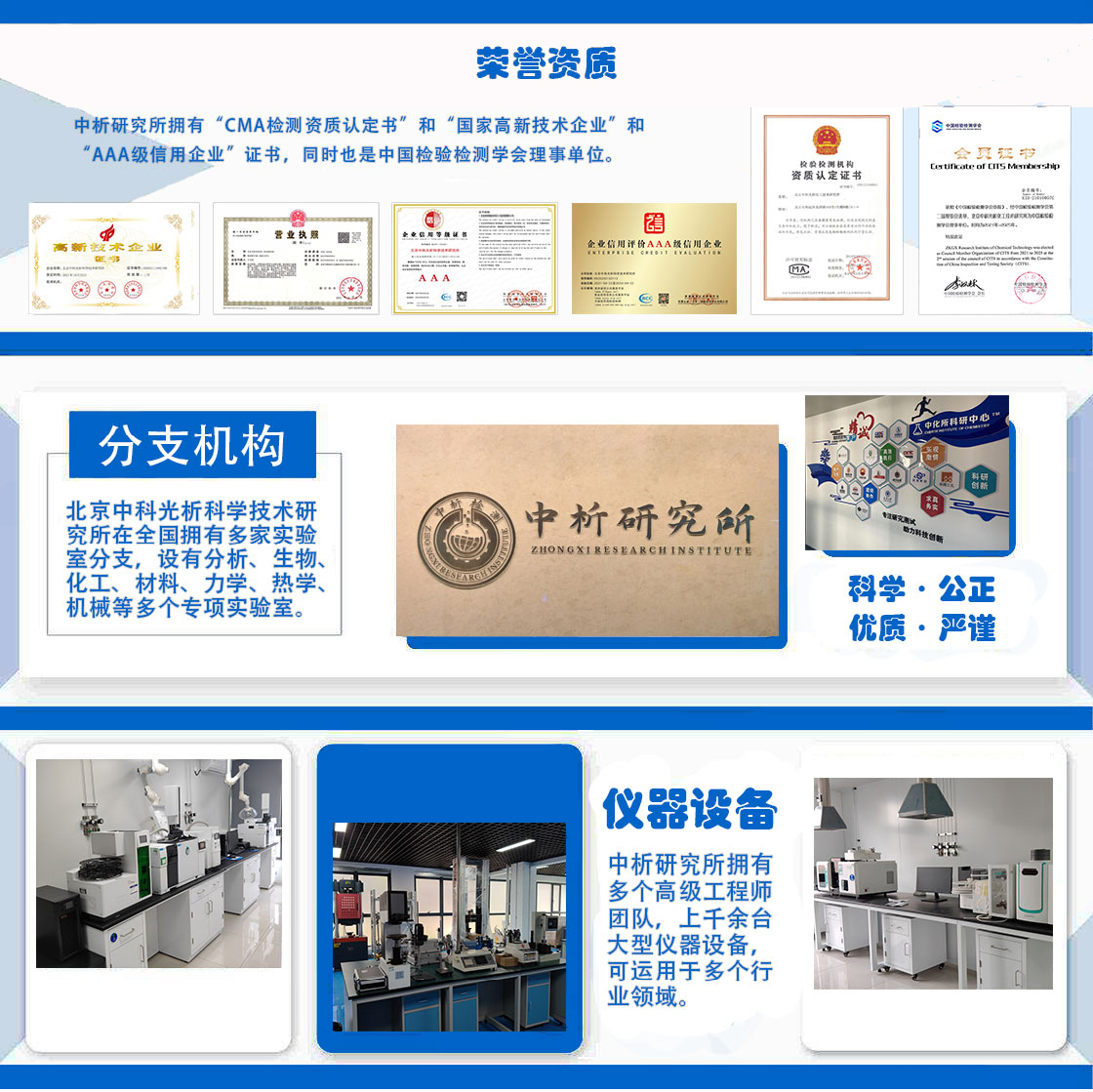
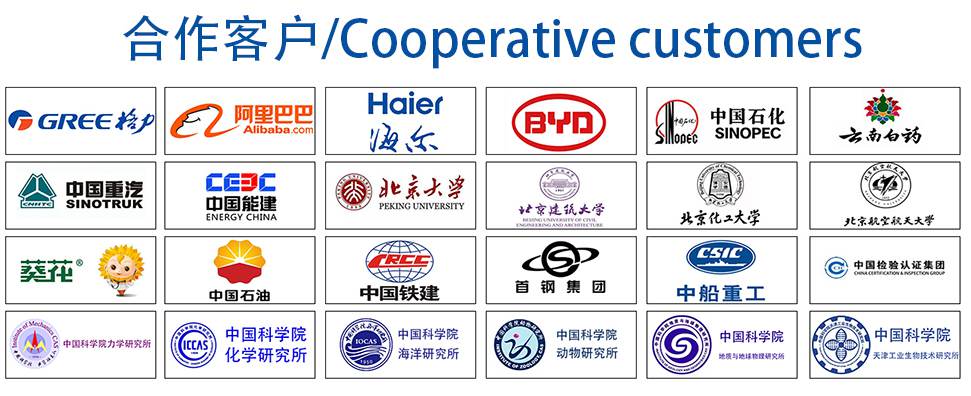