旋转电机热保护检测的重要性
旋转电机作为工业生产和设备运行的核心动力源,其长期稳定运行对生产效率与安全性至关重要。在实际工作中,电机因过载、散热不良或环境温度过高等因素引发的过热问题,可能导致绝缘材料老化、轴承损坏甚至设备烧毁等严重后果。热保护检测通过实时监测电机运行温度,结合智能控制手段,能够有效预防过热风险,延长设备寿命。随着工业自动化水平的提升,热保护检测技术已成为电机安全运维的关键环节,其检测项目的全面性与准确性直接影响设备管理效能。
核心检测项目及技术方法
1. 温度传感器校准与分布检测
通过校验嵌入式温度传感器(如PT100、热电偶)的精度误差是否在±1℃范围内,确保数据采集可靠性。需验证传感器在定子绕组、轴承座等关键部位的安装密度与覆盖范围,典型配置要求每相绕组至少设置2个监测点。
2. 热保护阈值动态测试
采用模拟负载法逐步提升电机功率至额定值的115%-130%,记录热继电器动作时间与温度曲线。要求保护装置在绝缘材料极限温度(如F级155℃)前触发停机,响应延迟不得超过20秒。
3. 散热系统效能评估
使用红外热像仪监测散热风扇转速与风道气流分布,验证强制冷却条件下温升速率是否≤3℃/min。同步检测散热片表面积尘量,规定粉尘覆盖率超过15%需触发清洁预警。
4. 绝缘材料热稳定性分析
通过步进升温试验测量绕组绝缘电阻变化率,在130℃恒温环境下保持4小时后,介质损耗因数(tanδ)增幅应小于初始值的30%。采用局部放电检测仪捕捉200℃阈值前的放电量突变信号。
5. 热-机耦合形变监测
利用光纤光栅传感器阵列检测定转子受热膨胀量差异,当轴向偏移超过0.15mm或径向间隙变化量达设计值的5%时,自动启动热平衡调节程序,防止机械卡阻故障。
智能诊断与趋势预测技术
现代检测系统集成大数据分析平台,通过机器学习算法建立温度-振动-电流的多参数关联模型。当检测到绕组热点温升速率异常(如>5℃/s)或三相温差持续超过8K时,系统可提前30分钟预测过热风险并生成维护工单。
结语
旋转电机热保护检测需综合运用传感技术、热力学建模与智能诊断手段,通过标准化的检测项目体系实现从被动保护到主动预防的转变。随着物联网与数字孪生技术的应用,未来检测精度与响应速度将进一步提升,为工业设备安全运行提供更强保障。
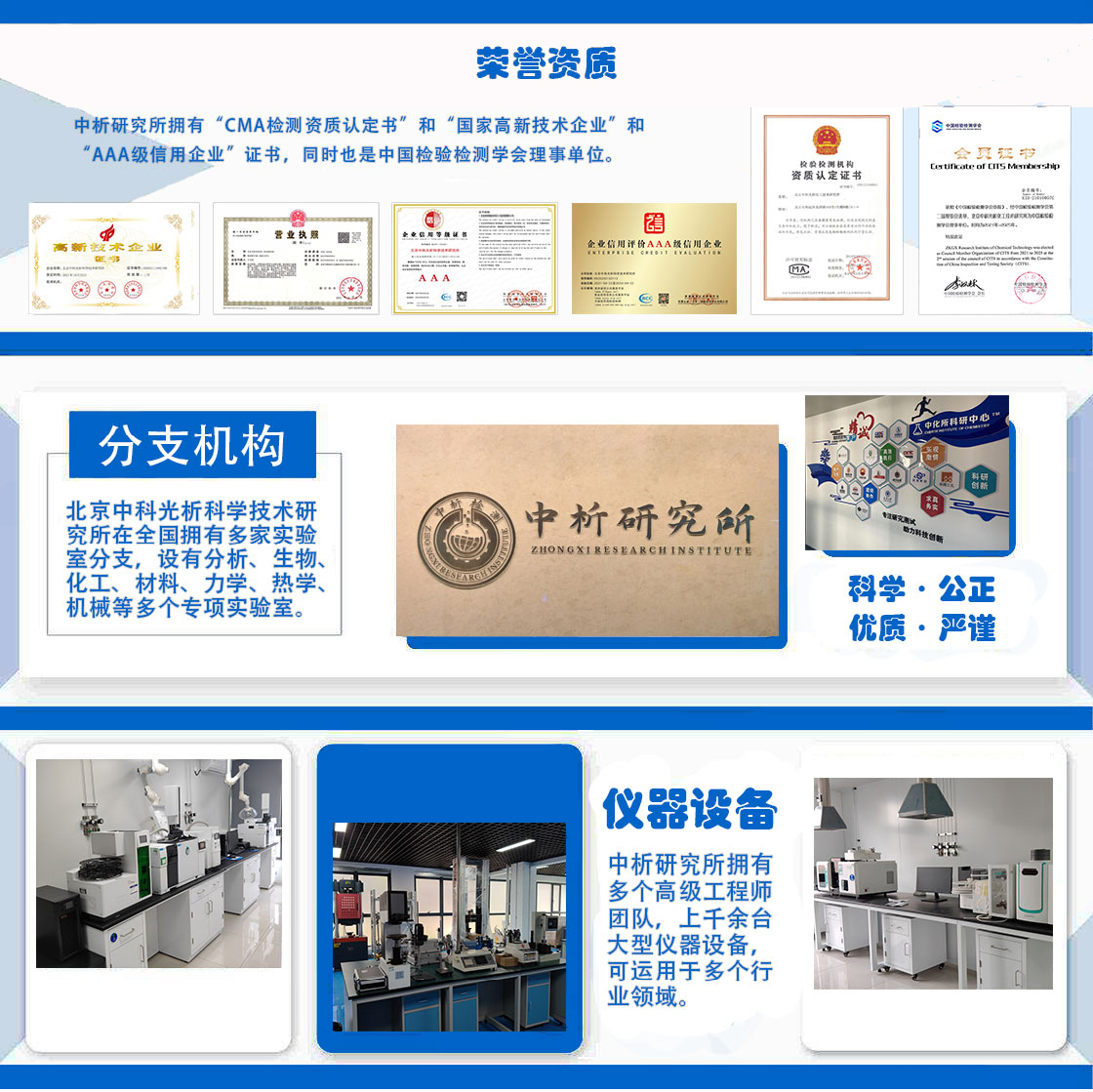
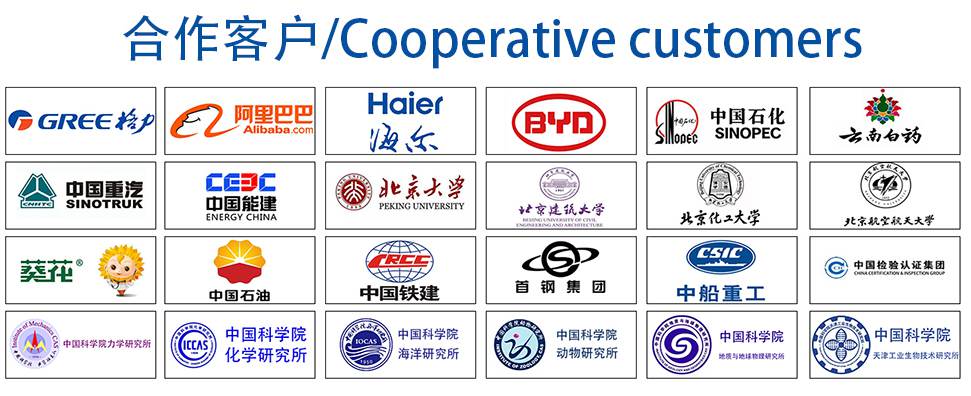