几何尺寸检测的核心价值与技术框架
在精密制造与质量控制领域,几何尺寸检测作为产品验收的核心环节,直接决定着机械零部件的装配精度和使用性能。这项检测通过数字化手段对工件的形状、尺寸、位置等特征进行量化分析,确保每个生产批次满足设计图纸的严苛要求。从航空航天发动机涡轮叶片的微米级公差控制,到汽车覆盖件的曲面匹配验证,几何尺寸检测贯穿于产品全生命周期,已成为现代智能制造体系中不可或缺的质量保障手段。ISO/TS 16949、AS9100等行业标准均对此类检测提出了系统化规范要求。
核心检测项目体系
1. 基本线性尺寸验证
涵盖长度、宽度、高度等一维参数的精确测量,使用数显卡尺、高度规等常规量具,或通过三坐标测量机(CMM)进行自动化检测。尤其在阶梯轴、箱体类零件的多尺寸验证中,需建立多测点关联分析模型。
2. 形状公差检测网络
针对平面度、圆度、圆柱度等形位特征建立评估矩阵:平面度检测常采用激光干涉仪建立基准平面;圆度测量依赖高精度转台与电感测头系统;圆柱度评价则需构建轴向多截面扫描数据云。
3. 空间位置关系判定
通过建立特征坐标系解析位置公差:平行度检测需构建双基准面投影系统;垂直度验证依赖直角规与光学自准直仪的协同测量;同轴度判定采用双测头同步跟踪技术,特别适用于长轴类零件的在线检测。
4. 曲面轮廓匹配分析
应用蓝光扫描或激光跟踪仪获取三维点云数据,通过NURBS曲面重建技术实现实际轮廓与CAD模型的偏差比对,在汽车覆盖件、涡轮叶片等自由曲面的质量控制中具有关键作用。
5. 动态尺寸链仿真
基于蒙特卡洛法的虚拟装配分析,预测多零件累积公差对整机性能的影响。该技术已广泛应用于发动机缸体-曲轴系统、精密减速机等复杂装配体的公差分配优化。
智能化检测发展趋势
随着工业4.0技术的深入应用,基于机器视觉的在线检测系统与数字孪生技术的结合,正在重构传统检测模式。智能量仪通过5G传输实时数据至MES系统,结合AI算法实现测量数据自解析,显著提升缺陷识别效率和过程控制能力。这种数字化检测体系不仅缩短了产品验证周期,更为智能制造闭环控制提供了关键数据支撑。
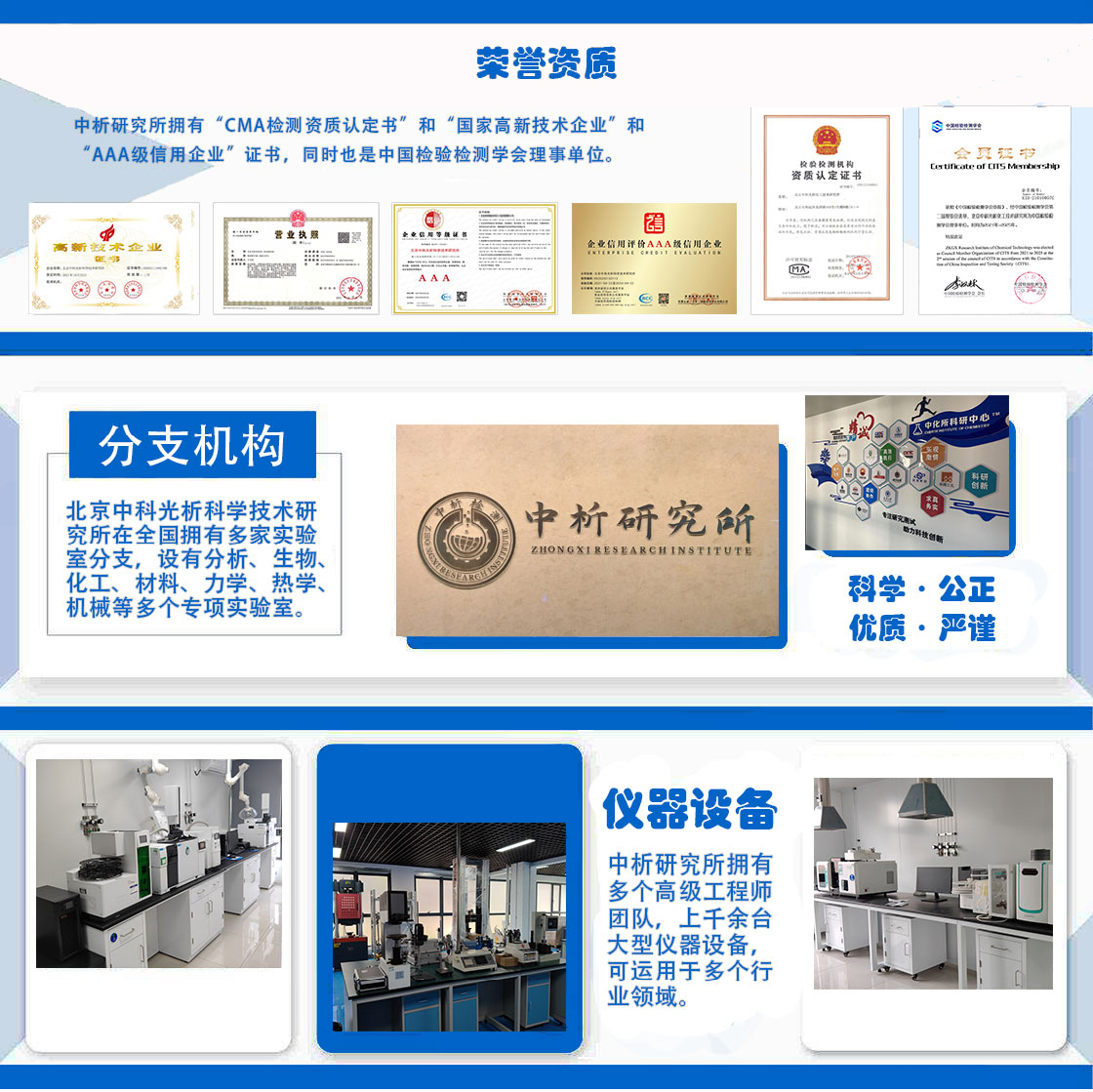
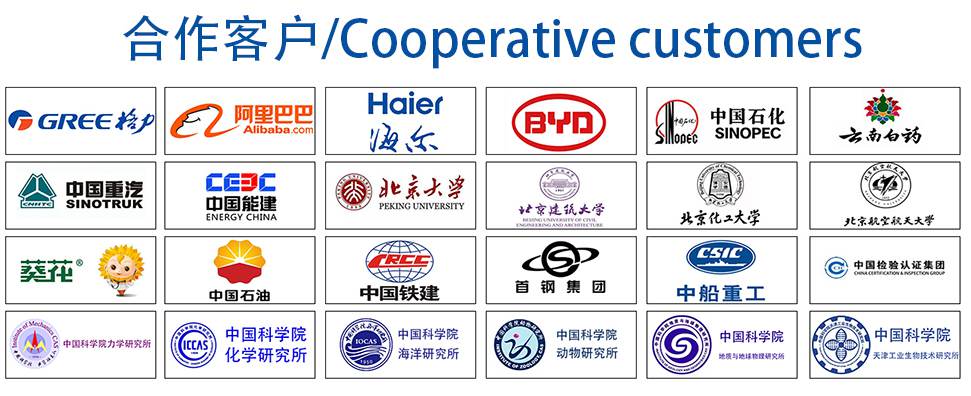