流量计量式间歇水添加系统检测的必要性与应用背景
流量计量式间歇水添加系统作为现代工业自动化控制的关键设备,广泛应用于农业灌溉、化工生产、食品加工及环保水处理等领域。该系统通过精准的流量传感器、控制模块与执行机构协同工作,实现预设周期内定量水资源的自动化投放。随着行业对用水效率、工艺精度及环保合规性要求的提升,系统性能的稳定性与计量准确性直接影响生产质量与资源利用率。因此,定期开展系统性检测不仅是设备维护的基础要求,更是确保工艺流程合规、规避生产风险的核心措施。
核心检测项目与技术要求
1. 流量计量精度验证
采用标准流量校准装置(如质量-时间法校准仪)对系统流量计进行全量程标定,要求示值误差不超过±1.5%(依据JJG 1038-2008《电磁流量计检定规程》)。重点检测低流速区间(<10%量程)的线性度及高流速段重复性误差。
2. 间歇控制时序同步性测试
通过多通道数据采集仪记录PLC指令信号、阀门动作响应时间及实际水流启动延迟,系统整体响应时间应≤500ms。需模拟不同工作周期(1-30分钟)下的启停循环,验证时序控制的稳定性和抗干扰能力。
3. 密封性及耐压试验
使用氮气保压法对管路系统进行1.5倍工作压力测试(最低不低于0.6MPa),保压30分钟压降不超过2%。同时检测电磁阀、快速接头等易泄漏部位的密封性能,确保无渗漏现象。
4. 人机交互功能验证
检查HMI界面参数设置逻辑、报警阈值设定(如流量超限、压力异常)及历史数据存储功能。需重点测试突发断电情况下数据保存完整性,确保累计流量数据偏差≤0.3%。
5. 环境适应性评估
在模拟工况环境(温度-20℃~50℃、湿度95%RH)下测试系统运行稳定性,验证流量计温度补偿功能有效性。振动试验需符合GB/T 2423.10标准,确保设备在4Hz~150Hz频率范围内无结构松动或测量漂移。
检测流程与周期建议
常规检测应遵循"静态校验-动态联调-环境模拟"三阶段流程,新装设备需进行72小时连续运行测试,年度复检周期不超过12个月。对于高腐蚀性介质环境或连续生产场景,建议缩短至6个月/次,并增加在线监测模块实施实时数据校核。
常见问题与改进方向
检测中多发的流量计电极结垢、电磁阀响应迟滞等问题,可通过增加预处理过滤器、优化控制算法(如PID参数自整定)等方式改善。新一代系统已引入物联网技术,支持远程校准与预测性维护,显著提升检测效率与系统可靠性。
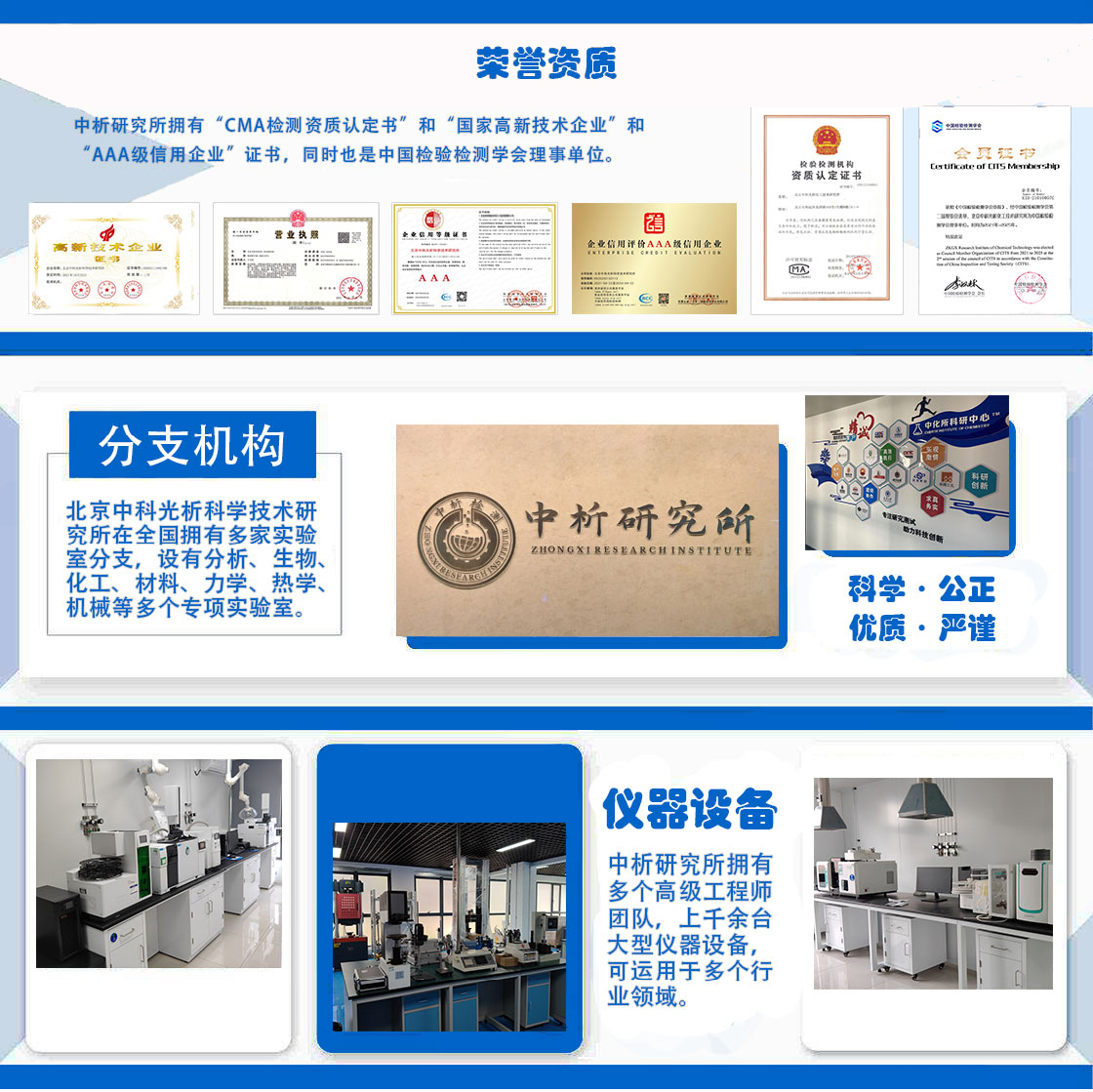
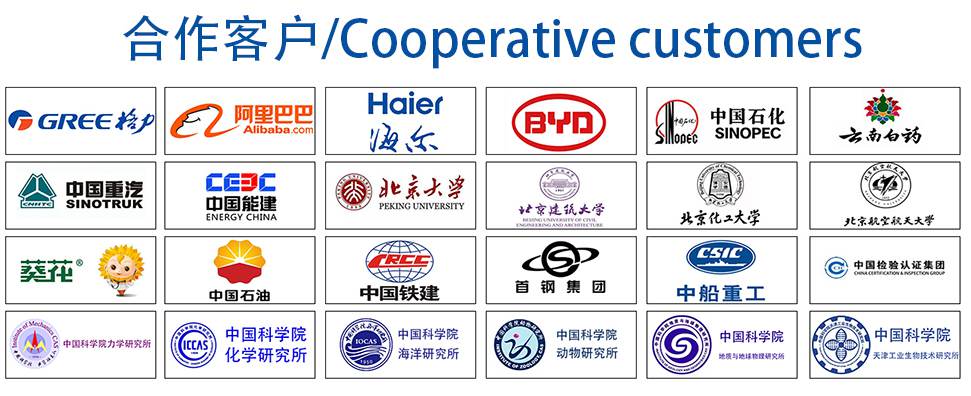