内燃机进、排气门检测的重要性与核心项目
在内燃机的工作过程中,进、排气门是控制气体交换的核心组件,其性能直接影响发动机的动力输出、燃油效率和排放水平。气门通过精确的开闭时序,确保新鲜空气或混合气进入气缸,并将燃烧后的废气排出。然而,在高温、高压和高速运动的工况下,气门容易发生磨损、变形、密封失效等问题。因此,定期对进、排气门进行系统性检测,是保障发动机可靠性和延长使用寿命的关键措施。
检测过程需覆盖气门的几何精度、材料性能、密封能力及动态响应等多个维度。以下为内燃机进、排气门检测的主要项目和技术要点:
一、气门密封性能检测
气门与气门座圈的密封性是检测的重点。常用方法包括:
1. 气压法:将气门安装至专用夹具,通入压缩空气后观察压力表数值变化,若压力下降速率超过标准值,表明密封不良。
2. 煤油渗漏法:在气门锥面涂煤油后倒置气门,若煤油在5分钟内渗漏至另一侧,判定为密封失效。
3. 接触带宽度测量:通过显微镜或投影仪检测气门锥面与座圈的接触带宽度,理想范围为1.2-2.0mm,过宽或过窄均需调整研磨工艺。
二、气门几何尺寸检测
几何精度直接影响气门与导管的配合及密封效果,主要检测项包括:
1. 气门杆直径:使用千分尺测量杆部多个位置的直径,偏差需控制在±0.01mm以内。
2. 气门头部厚度:厚度不足会导致热传导能力下降,需通过卡尺或影像仪检测。
3. 气门锥角:利用角度规或三坐标测量仪验证锥面角度(通常为45°或30°),角度偏差应小于±0.5°。
三、气门材料性能检测
气门需具备耐高温、抗氧化和抗冲击性能,检测项目涵盖:
1. 硬度测试:使用洛氏硬度计检测气门杆端部(HRC 30-40)和锥面(HRC 50-55)。
2. 金相组织分析:通过金相显微镜观察材料晶粒度及是否有脱碳、裂纹等缺陷。
3. 高温蠕变试验:模拟高温工况下气门的变形量,评估长期使用稳定性。
四、气门动态特性检测
动态性能检测主要针对气门运动规律,包括:
1. 升程曲线验证:采用位移传感器记录气门实际升程与理论曲线的匹配度。
2. 落座冲击力测试:通过加速度传感器监测气门闭合瞬间的冲击力,避免因弹簧疲劳导致密封失效。
3. 气门间隙检查:使用塞尺测量冷态下气门杆端与摇臂的间隙,确保符合发动机设计要求。
五、表面缺陷与磨损检测
气门表面状态直接影响使用寿命,需进行以下检测:
1. 磁粉探伤:检测气门杆部及过渡区域的微观裂纹。
2. 锥面磨损量测量:通过对比新旧气门的锥面轮廓,评估磨损是否超限(一般不超过0.1mm)。
3. 涂层完整性检查:对表面镀铬或氮化处理的气门,需确认涂层无剥落或局部腐蚀。
总结
内燃机进、排气门的检测需结合目视检查、精密测量与动态试验,覆盖从宏观尺寸到微观组织的全方位参数。随着检测技术的发展,激光三维扫描、声发射监测等齐全方法正逐步应用于气门质量控制中。通过系统性检测,可提前发现潜在故障,优化维修周期,最终实现发动机性能与可靠性的双重提升。
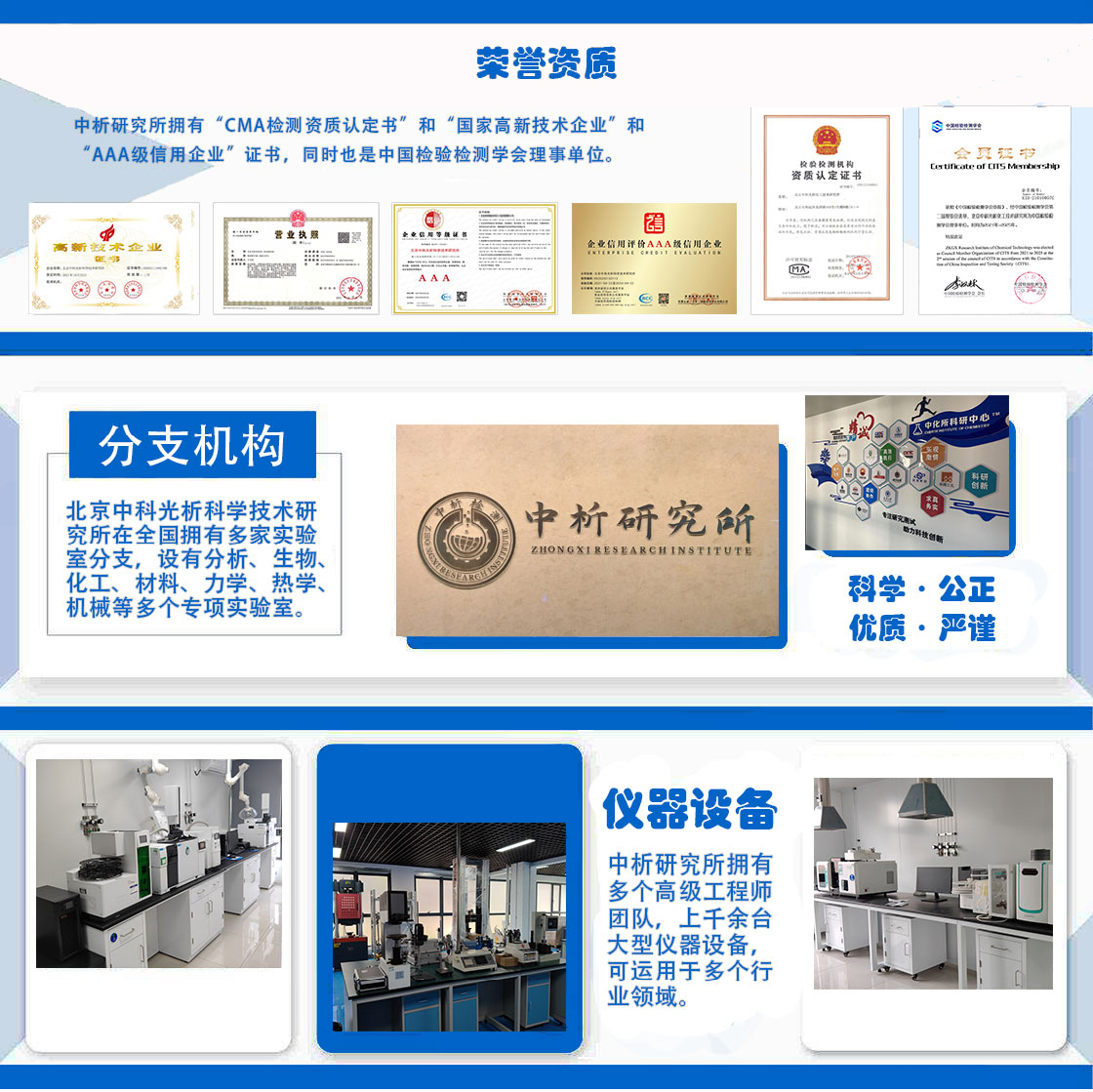
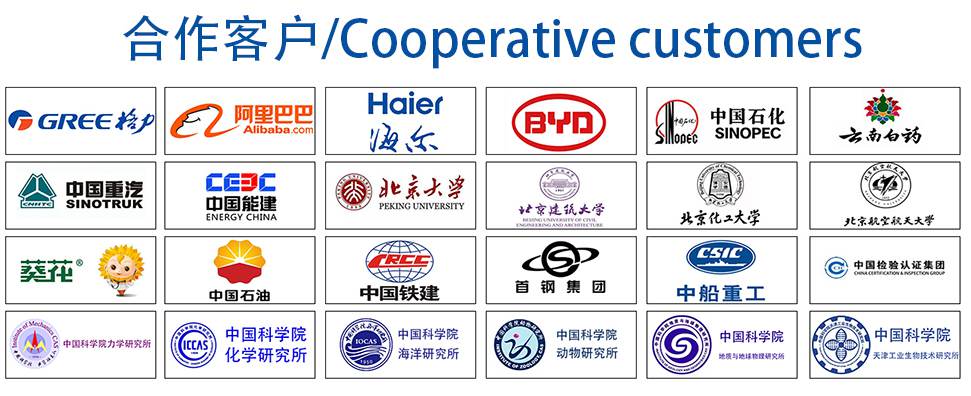