内燃机湿式铸铁气缸套检测的重要性
湿式铸铁气缸套作为内燃机的核心部件之一,承担着密封燃烧室、引导活塞运动以及传递热量的重要功能。其工作环境长期暴露在高温、高压、化学腐蚀和机械磨损的极端条件下,性能的稳定性直接关系到发动机的功率输出、燃油效率和整体寿命。由于湿式气缸套采用外壁直接接触冷却液的设计,其材料特性、加工精度及表面处理工艺的缺陷可能导致冷却液渗漏、缸体变形甚至发动机失效。因此,对湿式铸铁气缸套进行系统性检测,是确保内燃机可靠性和安全性的重要环节。
关键检测项目及技术要求
1. 外观与尺寸精度检测
通过三维测量仪和光学轮廓仪对气缸套的内径、外径、圆度、圆柱度进行精密测量,要求内径公差控制在±0.01mm以内。同时需检查表面是否存在砂眼、气孔、裂纹等铸造缺陷,特别是法兰与缸体接触面的加工质量需达到Ra1.6μm以下的表面粗糙度。
2. 材料成分与金相组织分析
采用直读光谱仪进行材料元素定量分析,重点检测碳(3.0-3.5%)、硅(1.8-2.5%)、锰(0.6-1.0%)的含量配比是否符合HT250或HT300灰铸铁标准。金相显微镜下观察石墨形态,要求A型石墨占比≥85%,珠光体含量需在95%以上,确保材料具备良好的导热性和抗变形能力。
3. 硬度与耐磨性测试
使用洛氏硬度计(HBW)在缸套轴向三点测量硬度值,要求布氏硬度范围180-240HB,同一工件硬度波动不超过15HB。通过往复式摩擦磨损试验机模拟工况,检测表面镀铬层或磷化处理层的耐磨性能,磨损量应小于0.05mm/100h。
4. 密封性与耐腐蚀检测
采用0.6MPa水压试验持续5分钟,检查冷却液腔道密封性,泄漏量不得超过5ml/min。盐雾试验需满足GB/T10125标准,经72小时中性盐雾测试后,表面腐蚀面积不超过5%。
5. 热疲劳与应力测试
通过高频感应加热装置模拟热循环工况,在300-500℃区间完成2000次冷热循环后,用超声波探伤仪检测微观裂纹。残余应力测试需控制在80-120MPa范围内,防止因应力集中导致的开裂风险。
检测技术发展趋势
随着工业CT、数字图像相关(DIC)等齐全检测技术的应用,现代检测体系正在向三维全尺寸数字化方向发展。智能制造背景下,在线检测系统可实时监控珩磨网纹角度(25-35°)、表面储油率(15-25%)等关键参数,结合大数据分析实现质量预测,推动气缸套检测进入智能化新阶段。
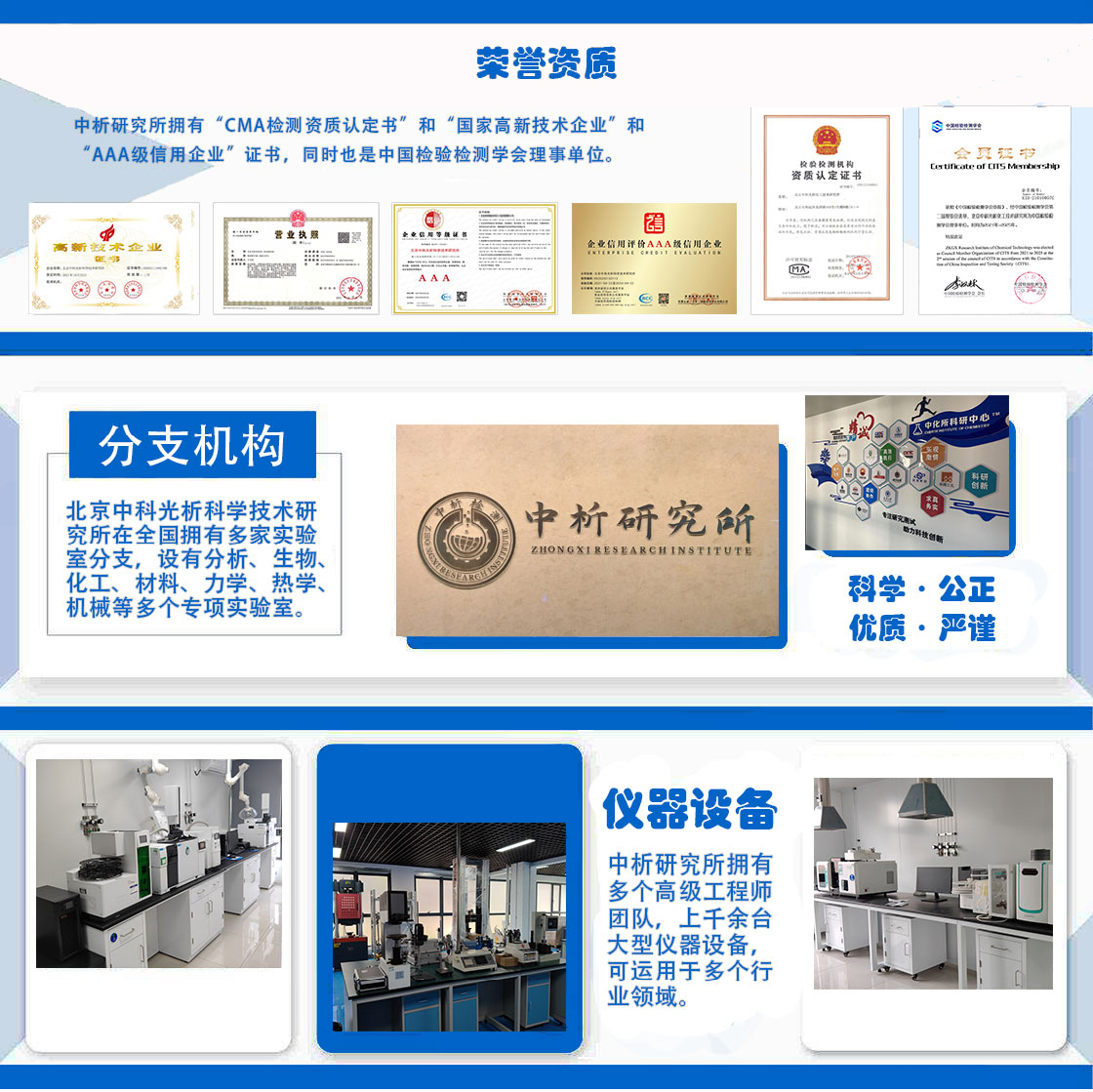
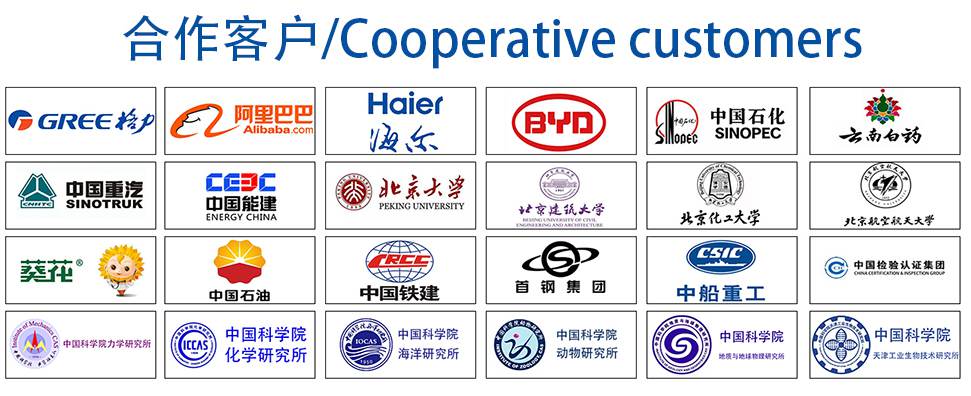