通用件检测的重要性与应用范围
通用件检测是制造业中确保零部件互换性、功能性和安全性的核心环节。通用件指在多种设备或系统中可重复使用的标准化部件,如螺栓、轴承、密封圈等。由于其广泛应用于汽车、航空、机械制造等领域,检测的精准性与全面性直接关系到设备运行效率和使用寿命。通过科学的检测手段,不仅能避免因零部件缺陷引发的设备故障,还能降低生产成本、提升供应链管理效率。
通用件检测的核心项目
1. 尺寸与几何精度检测
通过三坐标测量仪(CMM)、光学投影仪等设备,检测零部件的长度、直径、角度等参数是否满足公差要求,确保安装匹配度和功能稳定性。例如,轴承内径与外径的精度误差需控制在微米级。
2. 材料性能分析
利用光谱分析仪、硬度计等工具,验证材料的化学成分、抗拉强度、硬度及耐腐蚀性是否达标。对于高温或高压环境使用的通用件,还需进行金相组织观察以评估其微观结构稳定性。
3. 表面质量检测
通过粗糙度仪、电子显微镜等设备检查表面光洁度、划痕、裂纹及镀层厚度。例如,液压密封件表面若存在微小毛刺,可能导致密封失效引发泄漏。
4. 力学性能测试
模拟实际工况进行拉伸、压缩、扭转等试验,评估零部件的承载能力与疲劳寿命。弹簧类通用件需重点检测弹性模量和循环载荷下的变形量。
5. 互换性验证
将通用件与标准件进行装配测试,确认其在多品牌设备中的适配性。此环节对国际标准件(如ISO规格零件)尤为重要,需同时满足多国认证要求。
6. 环境耐受性试验
通过盐雾试验箱、高低温循环箱等设备模拟极端环境,检测零部件的抗老化、耐候性及温度适应性。例如,汽车通用线束需通过85℃高温老化测试。
检测技术的智能化升级
随着工业4.0的推进,机器视觉、AI算法和在线监测系统正在革新传统检测模式。智能检测平台可实现24小时自动化数据采集与分析,将检测效率提升50%以上,同时通过大数据预测零部件的潜在失效风险。
结语
通用件检测贯穿于设计验证、生产质控和售后维护全流程,是保障工业体系高效运转的基础。企业需根据产品特性建立定制化检测体系,并持续引入齐全技术,以应对日益复杂的质量挑战。
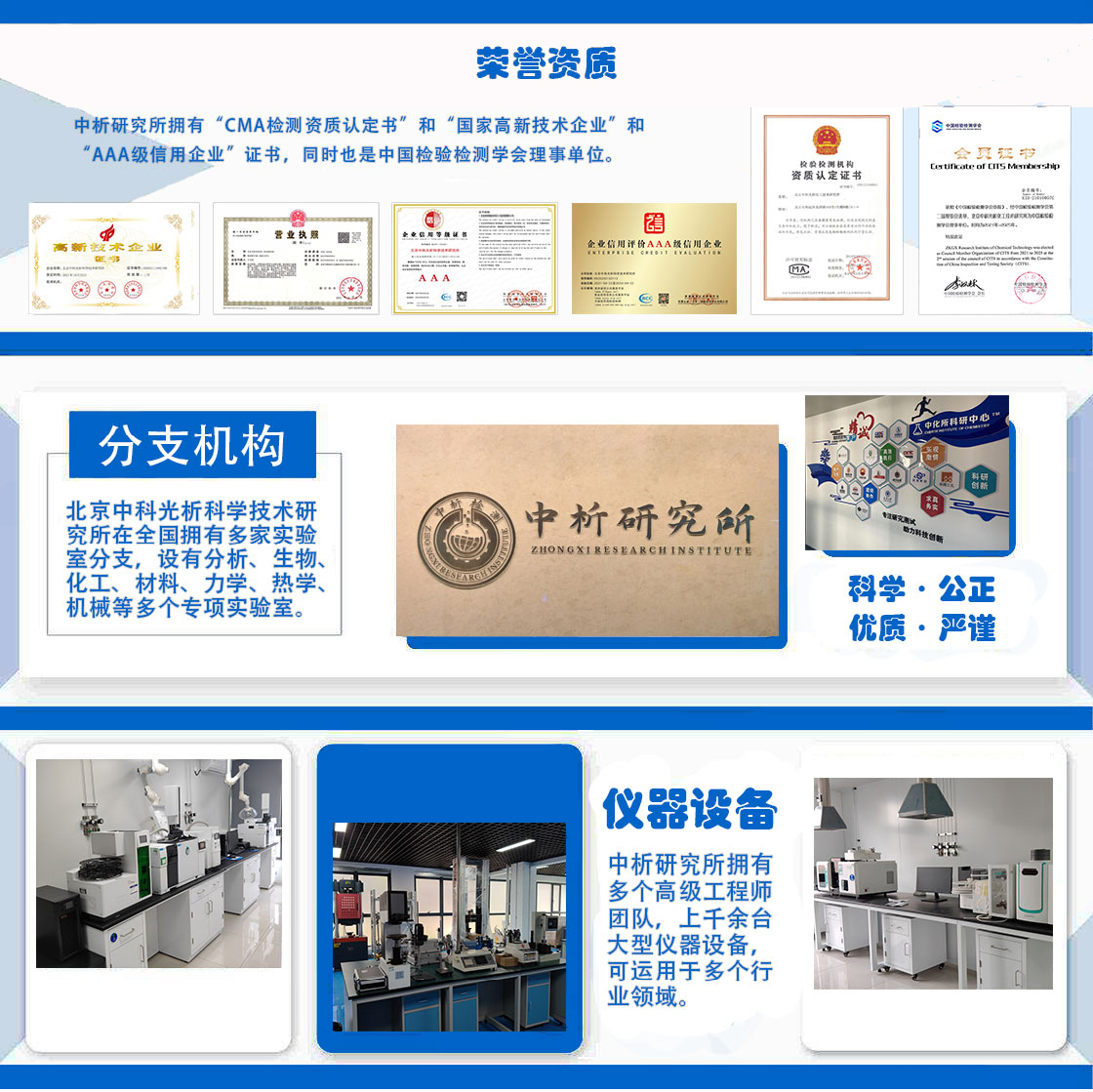
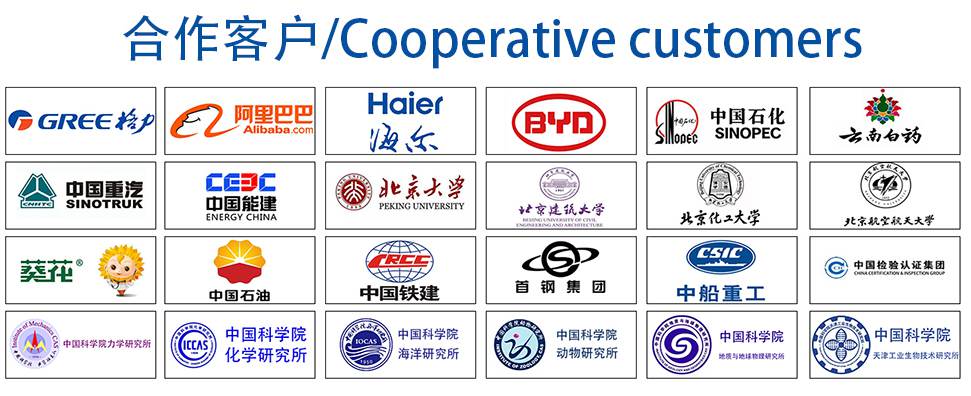