内燃机单体铸造活塞环检测的重要性
内燃机作为现代动力装置的核心部件,其性能与可靠性直接依赖于关键零部件的制造精度与质量。单体铸造活塞环作为气缸密封的核心组件,承担着高温、高压、高速摩擦等多重严苛工况的考验。其制造质量直接影响发动机的燃油效率、排放水平和运行寿命。由于活塞环在装配后难以直接观察或修复,出厂前的检测环节成为保障其功能性和安全性的最后一道防线。通过系统的检测项目,可有效排查铸造缺陷、尺寸偏差、材料性能不足等问题,从而避免因活塞环失效导致的发动机故障甚至灾难性事故。
核心检测项目分类
1. 几何尺寸与形位公差检测
采用高精度三坐标测量仪对活塞环的开口间隙、径向厚度、自由状态开口量等关键尺寸进行全检。重点验证环高公差(±0.01mm)、径向弹力分布均匀性以及端面平面度(≤0.02mm)。通过激光轮廓扫描技术实现表面波纹度与圆度的数字化分析,确保与缸套的动态密封匹配性。
2. 材料性能检测
通过光谱分析仪对铸造材料的化学成分(如碳、硅、钼含量)进行定量检测,确保符合HT250或QT600-3等材质标准。金相显微镜观察石墨形态与基体组织,评估球化率(≥90%)和珠光体含量。配合显微硬度计(HV500载荷)进行多点硬度测试,验证表面硬化层深度(0.1-0.3mm)与芯部硬度的梯度分布合理性。
3. 表面处理质量检测
针对镀铬或等离子喷涂等表面强化工艺,使用X射线荧光测厚仪测量镀层厚度(50-150μm),结合划痕试验评估结合强度(≥60MPa)。通过白光干涉仪分析表面粗糙度(Ra≤0.4μm),并采用盐雾试验(72h)验证耐腐蚀性能。对于DLC类涂层还需进行摩擦系数测试(μ≤0.1)。
4. 力学性能测试
在万能材料试验机上完成弹性模量(100-150GPa)和抗弯强度(≥800MPa)测试。通过疲劳试验机模拟高频交变载荷(10^7次循环),检测裂纹萌生周期。同时开展热膨胀系数测定(11-13×10^-6/℃),确保高温工况下的尺寸稳定性。
5. 无损检测与功能性验证
利用涡流检测技术筛查表面微裂纹(深度>0.05mm),配合工业CT对内部气孔、夹渣等缺陷进行三维成像(缺陷尺寸<Φ0.3mm)。最终通过模拟台架试验,在200℃工作温度下检测漏气量(≤3L/min)和机油消耗率(<0.1g/kWh),实现功能性综合验证。
检测技术创新趋势
随着智能制造的推进,基于机器视觉的在线检测系统可实现每秒20个环的自动分选,AI算法可对X射线图像进行实时缺陷分类。数字孪生技术将检测数据与服役性能进行关联建模,推动检测标准从"符合性判定"向"寿命预测"升级。这些技术进步正在重构活塞环质量控制的体系架构。
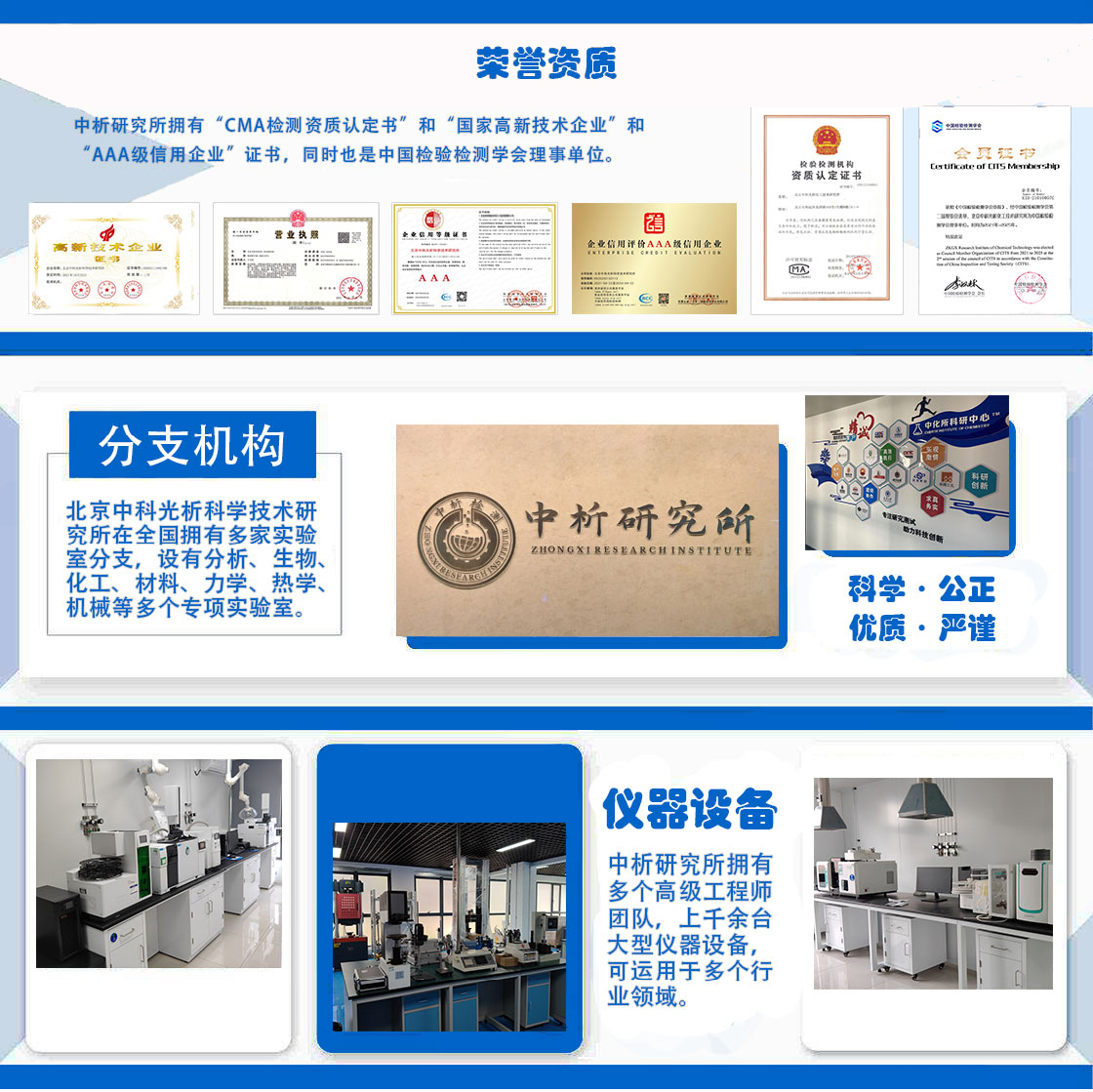
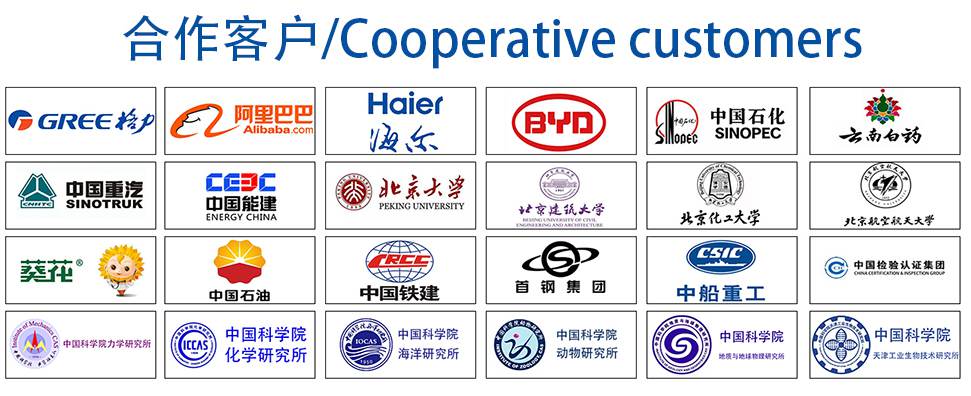