易拉罐灌装生产线检测的重要性与核心项目解析
在现代饮料工业中,易拉罐灌装生产线是保障产品效率与质量的核心环节。随着消费者对食品安全、包装密封性及产品一致性的要求日益严格,生产线的检测技术已成为企业竞争力的关键。一套完善的检测体系能够覆盖从罐体成型、灌装封盖到成品包装的全流程,通过自动化设备与智能算法精准识别缺陷,避免漏液、污染、标签错误等问题。据统计,高效检测系统可使生产线不良率降低70%以上,同时减少3%-8%的原料损耗。以下将针对易拉罐灌装生产线中关键检测项目展开详细剖析。
1. 密封性检测
灌装后的密封完整性直接决定产品保质期与安全性。检测系统通过负压测试、视觉检测双重验证:负压测试仪对罐体施加压力,监测压力变化以判断是否存在微孔或封盖不严;高分辨率工业相机则对罐口封边进行360°成像分析,识别卷封结构的尺寸偏差(如埋头深度、盖钩长度)及异物残留,精度可达±0.05mm。
2. 液位精度检测
灌装液位偏差超出±1.5mm即可能引发消费者投诉。X射线或超声波传感器实时扫描罐内液面高度,结合伺服电机动态调整灌装阀开度,确保每罐饮料容量符合GB/T 10792标准。系统同步记录波动数据,帮助追溯灌装压力、温度等参数异常,优化工艺稳定性。
3. 异物与污染物检测
金属碎屑、玻璃碎片等异物可能源自生产线磨损或原料杂质。X光异物检测机通过多能量射线扫描,可识别直径≥0.3mm的金属颗粒及密度异常物质;而近红外光谱仪则用于检测油污、清洗剂残留等化学污染物,检测限低至5ppm,确保产品符合FDA/GB 7101卫生标准。
4. 外观与标识检测
高速视觉系统(500罐/分钟)对罐体印刷质量进行全检:通过OCR技术核对生产日期、批号,字符识别准确率≥99.9%;色差分析模块监测LOGO色彩偏差(ΔE<1.5),同时检测凹痕、划痕等物理损伤,缺陷品通过气动喷嘴自动剔除,避免流入包装环节。
5. 生产线效能监控
集成化传感器网络实时采集OEE(设备综合效率)数据:灌装头每分钟动作频次、传送带速度波动、封盖机扭矩曲线等关键参数均被同步分析。当某工段效率低于设定阈值(如85%)时,系统自动触发预警并生成维护建议,帮助实现预测性保养,减少非计划停机时间。
未来趋势:智能化检测升级
随着工业4.0技术的渗透,基于深度学习的缺陷分类算法正在替代传统规则判断,可自主学习新型缺陷模式;数字孪生技术则通过3D建模实现虚拟调试,使检测系统调试周期缩短40%。企业通过部署MES系统整合检测数据,可构建完整的质量追溯链,最终达成零缺陷生产目标。
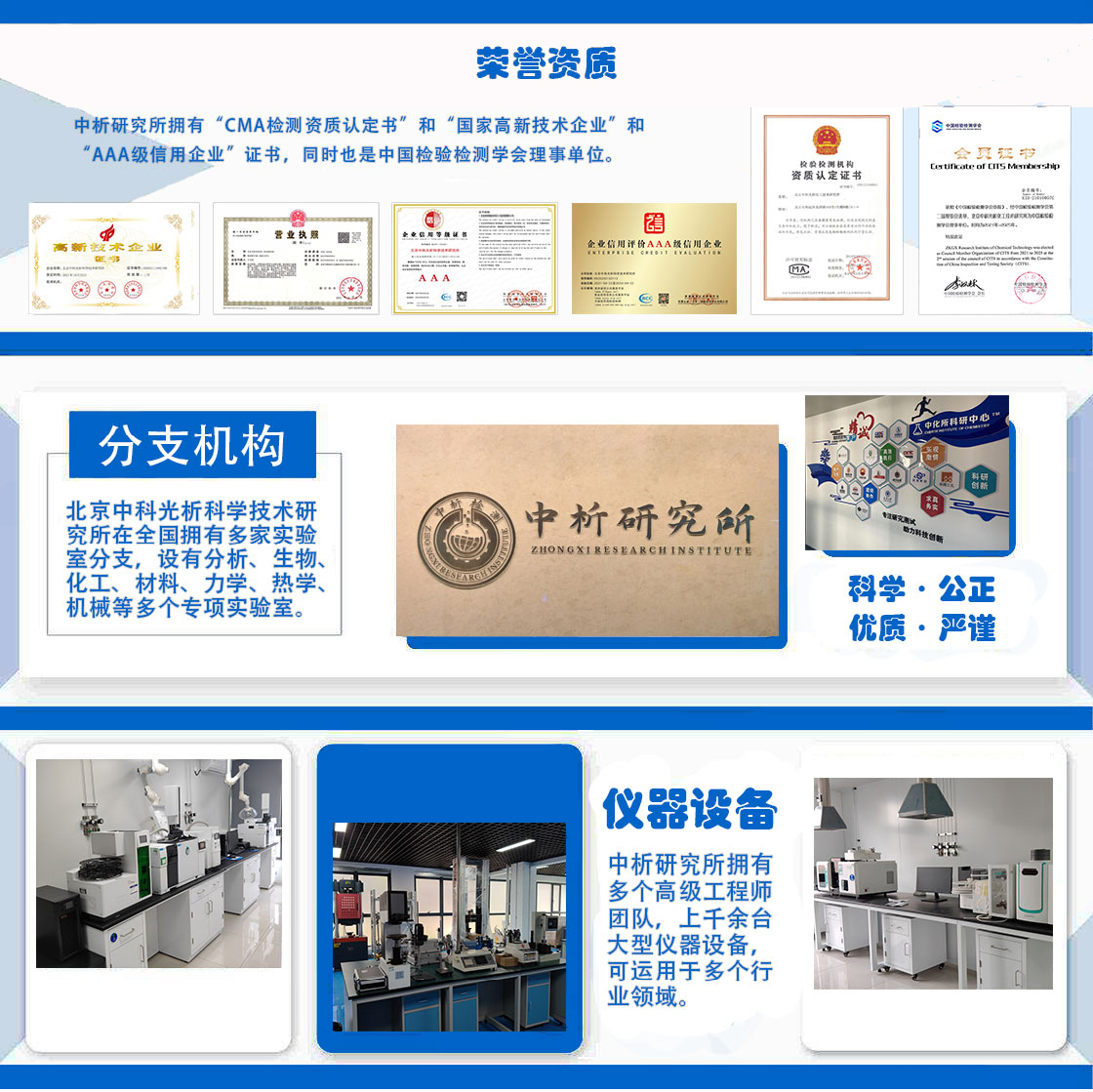
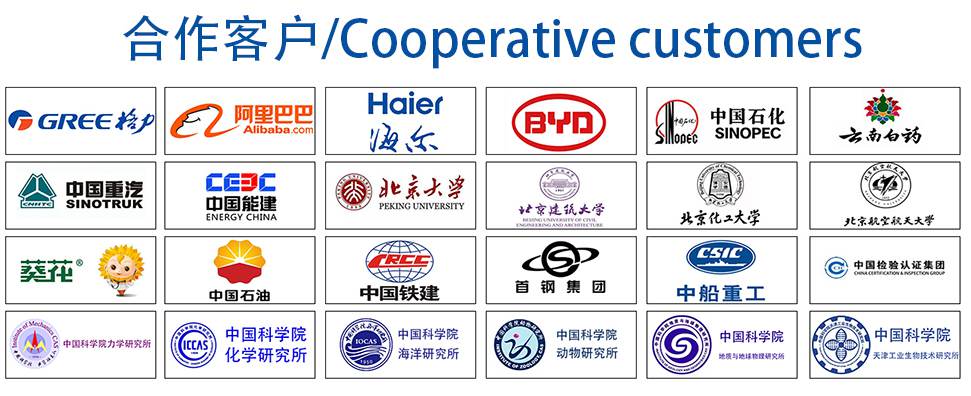