气弹簧检测的重要性与核心项目解析
气弹簧作为一种以压缩气体为储能介质的弹性元件,广泛应用于汽车、工业设备、家具及航空航天等领域。其核心功能是提供稳定的支撑力、缓冲振动并实现机械部件的精准定位。由于气弹簧的性能直接影响设备安全性、使用寿命及用户体验,出厂前及使用过程中的质量检测至关重要。通过科学规范的检测流程,可确保产品符合行业标准(如GB/T 25751-2010《气弹簧技术条件》),同时为故障诊断和优化设计提供数据支持。
气弹簧核心检测项目分类
1. 外观与结构检测
通过目视检查或光学仪器分析气弹簧表面是否存在划痕、锈蚀、变形等问题,同时验证密封圈、活塞杆等关键部件的装配完整性。此项目可排除因运输或制造工艺缺陷导致的初期故障。
2. 气密性测试
采用压力衰减法或氦质谱检漏法,在规定压力(通常为1.5倍工作压力)下保持30分钟,检测压力下降值是否超过允许范围(一般≤5%)。该测试能有效发现微小泄漏点,避免因气体泄露导致的支撑力衰减。
3. 动态特性检测
包括行程-力值曲线测试、阻尼特性分析及启动力检测。通过伺服液压试验机模拟实际工况,记录气弹簧在伸缩过程中的力值变化,验证其是否满足设计的线性度要求,并检测是否存在卡滞或异常振动现象。
4. 耐久性试验
在恒定频率(通常2-5Hz)下进行10万次以上循环测试,评估气弹簧的疲劳寿命。试验后需复测关键参数(如力值衰减率≤15%、泄漏量≤3%),以确认产品在长期使用中的可靠性。
5. 环境适应性验证
涵盖高低温冲击试验(-40℃至+80℃)、盐雾腐蚀测试(96小时)及湿热老化试验,评估极端环境下密封性能、材料强度及表面涂层的耐久性,确保产品在复杂工况下的稳定性。
6. 力学性能检测
包括静态压缩强度测试(破坏压力≥2倍工作压力)、抗侧向力测试(施加30%轴向力值的侧向载荷),检验气弹簧在过载或异常受力情况下的结构安全性。
智能化检测技术发展趋势
随着工业4.0的推进,气弹簧检测正逐步向自动化、数字化方向升级。基于机器视觉的缺陷识别系统可实现外观检测效率提升300%,而搭载多通道传感器的综合测试平台能同步采集20+项参数并生成3D力-位移图谱。通过大数据分析,企业可建立产品全生命周期质量档案,实现预测性维护和工艺优化。
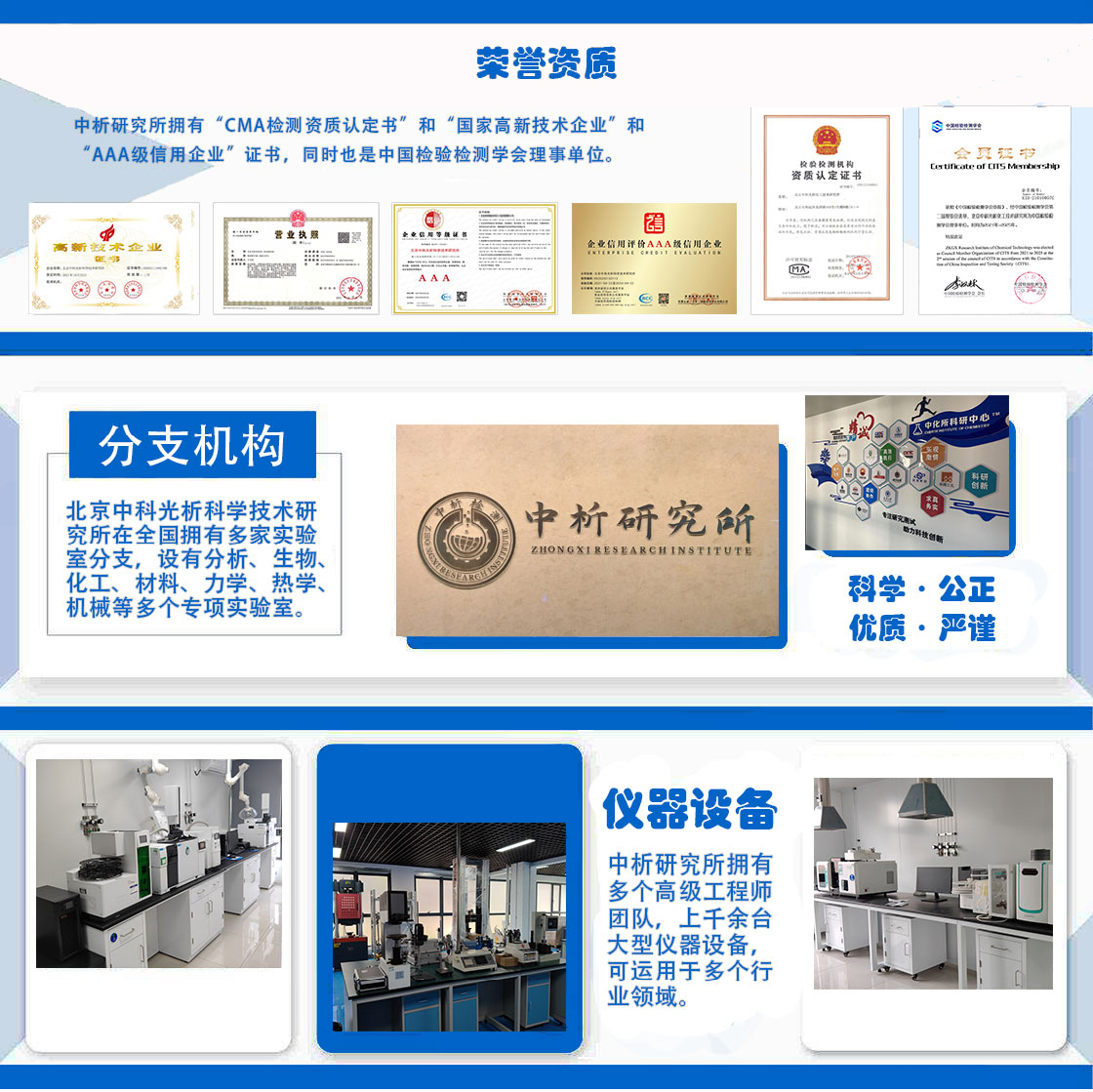
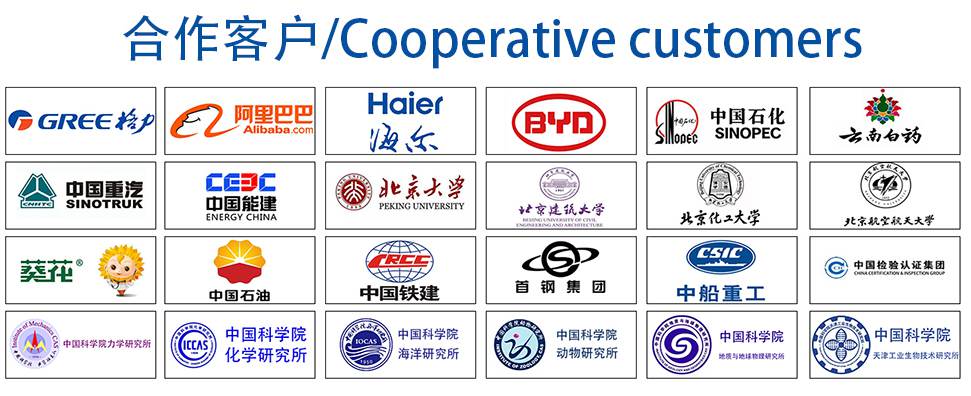