焊接件质量检测的意义与重要性
焊接作为制造业中广泛应用的连接工艺,其质量直接关系到产品的安全性、可靠性和使用寿命。焊接件若存在未熔合、裂纹、气孔、夹杂等缺陷,可能导致结构强度下降、密封性失效或疲劳寿命缩短,甚至引发严重事故。因此,焊接件质量检测是产品出厂前至关重要的环节,需通过系统性检测手段对焊缝及热影响区的物理性能、化学成分和几何精度进行全面评估,确保其符合相关技术标准(如ISO 3834、AWS D1.1等)和设计要求。
焊接件质量检测的核心项目
1. 外观检查
通过目视或放大镜观察焊缝表面是否存在咬边、焊瘤、凹陷、飞溅等缺陷,同时使用焊缝量规测量余高、宽度、错边量等几何参数。外观检查可快速识别表面不连续性缺陷,是检测流程的第一步。
2. 无损检测(NDT)
包含多种非破坏性检测技术:
- 射线检测(RT):利用X/γ射线穿透焊缝生成影像,检测内部气孔、夹渣等体积型缺陷。
- 超声波检测(UT):通过高频声波反射判断裂纹、未熔合等平面型缺陷的位置和尺寸。
- 磁粉检测(MT):适用于铁磁性材料表面及近表面裂纹检测。
- 渗透检测(PT):通过显色剂揭示开放性表面缺陷。
3. 力学性能测试
通过拉伸试验、弯曲试验、冲击试验等验证焊接接头的强度、塑性和韧性。例如依据ISO 4136标准进行横向拉伸试验,测定抗拉强度是否达标。
4. 化学成分分析
使用光谱仪对焊缝金属进行元素分析,检测碳当量、合金元素含量是否符合母材匹配要求,避免因成分偏差导致脆化或腐蚀倾向。
5. 尺寸精度测量
借助三坐标测量仪、激光扫描仪等设备,评估焊接结构的形位公差、装配尺寸是否符合设计图纸,确保后续组装的兼容性。
6. 气密性试验
对压力容器、管道等承压部件进行水压试验或气压试验,验证焊缝的密封性能,检测压力保持期间是否存在渗漏现象。
7. 金相检验
通过显微组织分析观察焊缝区、热影响区的晶粒度、相组成及缺陷分布,判断焊接工艺参数(如热输入、冷却速率)是否合理。
8. 焊接工艺评定(WPS/PQR)
依据ASME IX或EN ISO 15614标准,对焊接工艺规程进行验证试验,确保工艺参数能够稳定生产合格焊件,并建立可追溯的技术档案。
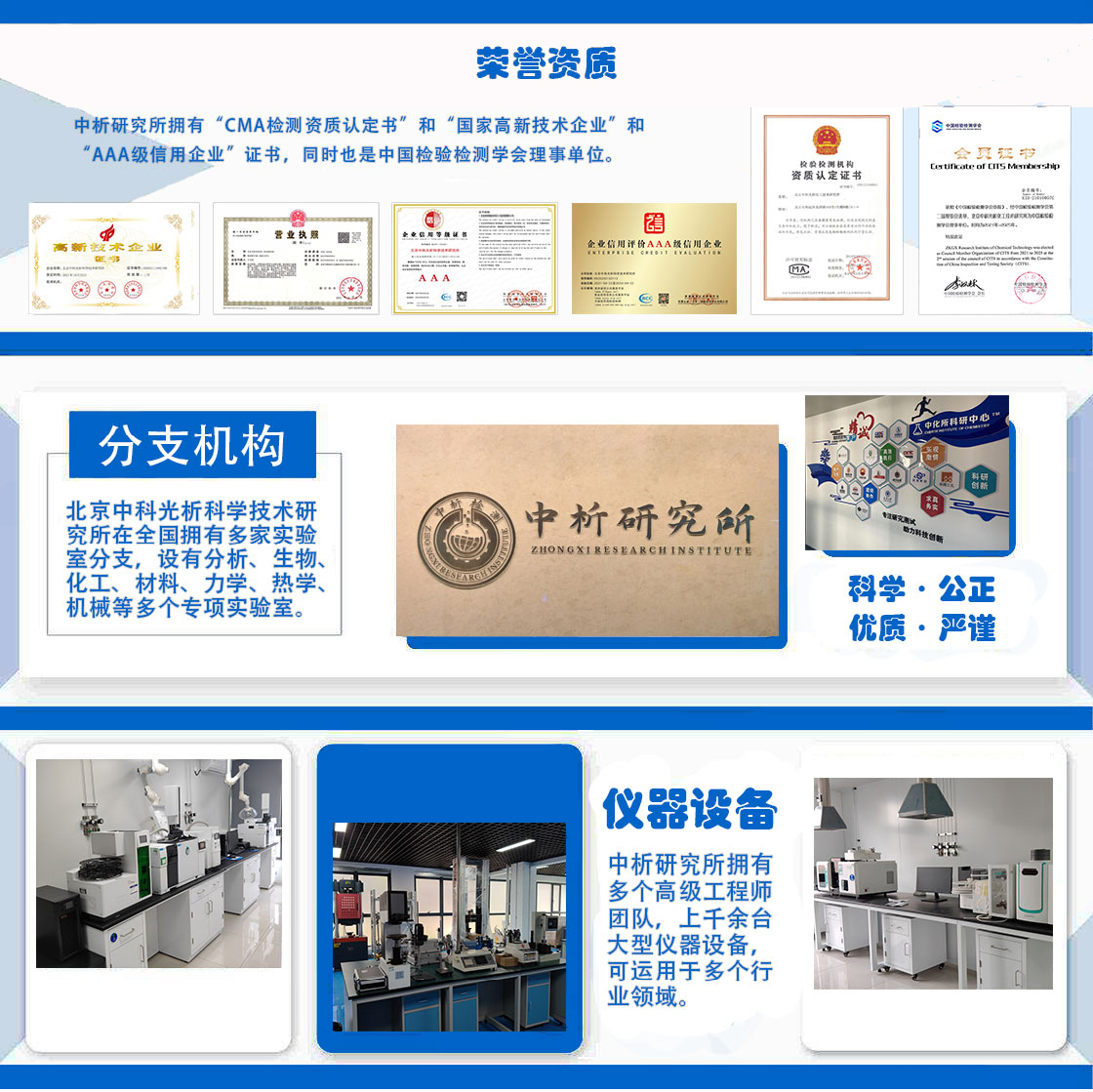
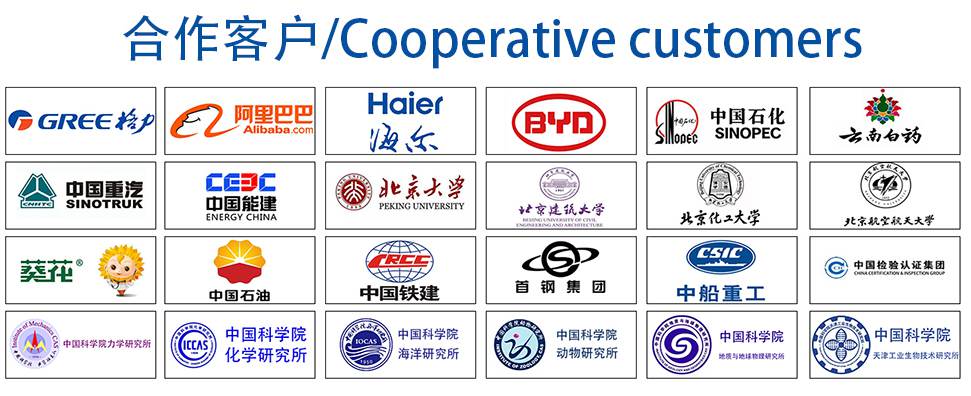